
Filter News
Area of Research
News Topics
- (-) Critical Materials (25)
- (-) Fossil Energy (5)
- (-) Transformational Challenge Reactor (7)
- 3-D Printing/Advanced Manufacturing (119)
- Advanced Reactors (34)
- Artificial Intelligence (91)
- Big Data (53)
- Bioenergy (91)
- Biology (98)
- Biomedical (58)
- Biotechnology (22)
- Buildings (57)
- Chemical Sciences (63)
- Clean Water (29)
- Climate Change (99)
- Composites (26)
- Computer Science (187)
- Coronavirus (46)
- Cybersecurity (35)
- Decarbonization (79)
- Education (4)
- Element Discovery (1)
- Emergency (2)
- Energy Storage (108)
- Environment (194)
- Exascale Computing (37)
- Frontier (42)
- Fusion (53)
- Grid (62)
- High-Performance Computing (84)
- Hydropower (11)
- Irradiation (3)
- Isotopes (53)
- ITER (7)
- Machine Learning (47)
- Materials (143)
- Materials Science (139)
- Mathematics (7)
- Mercury (12)
- Microelectronics (2)
- Microscopy (51)
- Molten Salt (8)
- Nanotechnology (60)
- National Security (60)
- Net Zero (13)
- Neutron Science (131)
- Nuclear Energy (106)
- Partnerships (43)
- Physics (61)
- Polymers (33)
- Quantum Computing (34)
- Quantum Science (69)
- Renewable Energy (2)
- Security (24)
- Simulation (47)
- Software (1)
- Space Exploration (25)
- Statistics (3)
- Summit (57)
- Sustainable Energy (125)
- Transportation (97)
Media Contacts
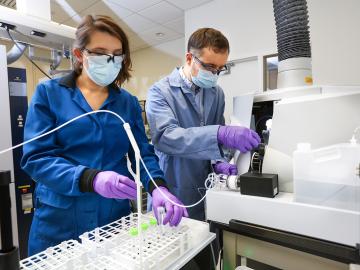
A new technology for rare-earth elements chemical separation has been licensed to Marshallton Research Laboratories, a North Carolina-based manufacturer of organic chemicals for a range of industries.
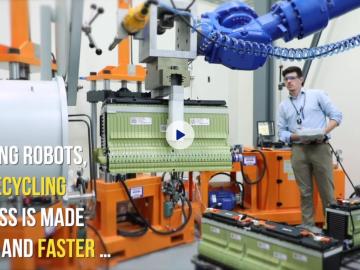
Researchers at ORNL have developed a robotic disassembly system for spent electric vehicle battery packs to safely and efficiently recycle and reuse critical materials while reducing toxic waste.
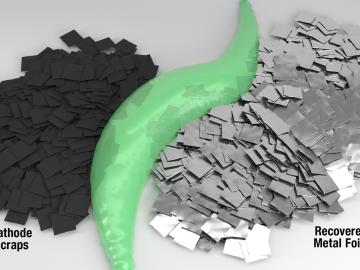
Scientists at Oak Ridge National Laboratory have developed a solvent that results in a more environmentally friendly process to recover valuable materials from used lithium-ion batteries, supports a stable domestic supply chain for new batteries

Scientists at Oak Ridge National Laboratory have devised a method to identify the unique chemical makeup of every lithium-ion battery around the world, information that could accelerate recycling, recover critical materials and resolve a growing waste stream.
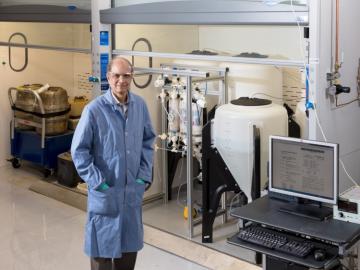
Momentum Technologies Inc., a Dallas, Texas-based materials science company that is focused on extracting critical metals from electronic waste, has licensed an Oak Ridge National Laboratory process for recovering cobalt and other metals from spent
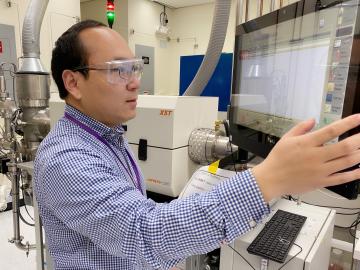
About 60 years ago, scientists discovered that a certain rare earth metal-hydrogen mixture, yttrium, could be the ideal moderator to go inside small, gas-cooled nuclear reactors.
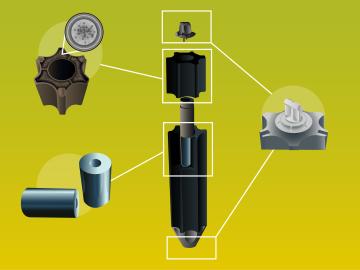
It’s a new type of nuclear reactor core. And the materials that will make it up are novel — products of Oak Ridge National Laboratory’s advanced materials and manufacturing technologies.
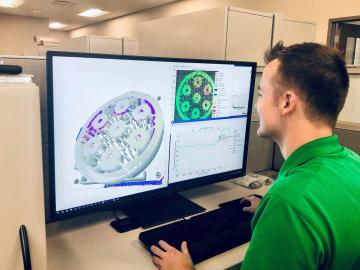
Oak Ridge National Laboratory researchers have developed artificial intelligence software for powder bed 3D printers that assesses the quality of parts in real time, without the need for expensive characterization equipment.
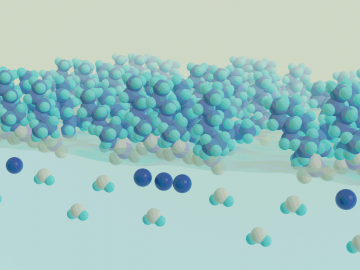
Real-time measurements captured by researchers at ORNL provide missing insight into chemical separations to recover cobalt, a critical raw material used to make batteries and magnets for modern technologies.
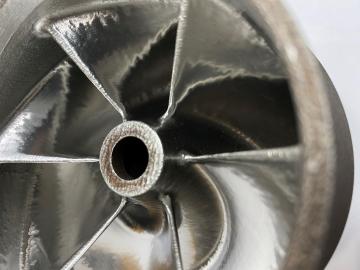
Scientists at the Department of Energy Manufacturing Demonstration Facility at ORNL have their eyes on the prize: the Transformational Challenge Reactor, or TCR, a microreactor built using 3D printing and other new approaches that will be up and running by 2023.