
Filter News
Area of Research
- Advanced Manufacturing (1)
- Biology and Environment (15)
- Clean Energy (9)
- Electricity and Smart Grid (1)
- Functional Materials for Energy (1)
- Fusion and Fission (4)
- Materials (4)
- Materials for Computing (1)
- National Security (1)
- Neutron Science (1)
- Nuclear Science and Technology (3)
- Supercomputing (14)
News Topics
- (-) Fossil Energy (5)
- (-) Simulation (46)
- (-) Transformational Challenge Reactor (7)
- 3-D Printing/Advanced Manufacturing (119)
- Advanced Reactors (34)
- Artificial Intelligence (91)
- Big Data (53)
- Bioenergy (91)
- Biology (98)
- Biomedical (58)
- Biotechnology (22)
- Buildings (57)
- Chemical Sciences (63)
- Clean Water (29)
- Climate Change (99)
- Composites (26)
- Computer Science (186)
- Coronavirus (46)
- Critical Materials (25)
- Cybersecurity (35)
- Decarbonization (79)
- Education (4)
- Element Discovery (1)
- Emergency (2)
- Energy Storage (108)
- Environment (194)
- Exascale Computing (37)
- Frontier (42)
- Fusion (53)
- Grid (62)
- High-Performance Computing (84)
- Hydropower (11)
- Irradiation (3)
- Isotopes (53)
- ITER (7)
- Machine Learning (47)
- Materials (143)
- Materials Science (139)
- Mathematics (7)
- Mercury (12)
- Microelectronics (2)
- Microscopy (51)
- Molten Salt (8)
- Nanotechnology (60)
- National Security (60)
- Net Zero (13)
- Neutron Science (131)
- Nuclear Energy (106)
- Partnerships (43)
- Physics (60)
- Polymers (33)
- Quantum Computing (33)
- Quantum Science (68)
- Renewable Energy (2)
- Security (24)
- Software (1)
- Space Exploration (25)
- Statistics (3)
- Summit (57)
- Sustainable Energy (125)
- Transportation (96)
Media Contacts
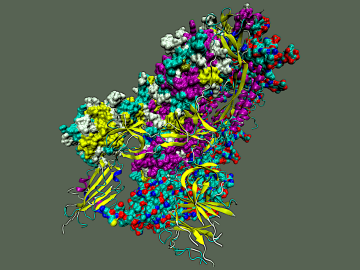
To explore the inner workings of severe acute respiratory syndrome coronavirus 2, or SARS-CoV-2, researchers from ORNL developed a novel technique.

A novel method to 3D print components for nuclear reactors, developed by the Department of Energy’s Oak Ridge National Laboratory, has been licensed by Ultra Safe Nuclear Corporation.
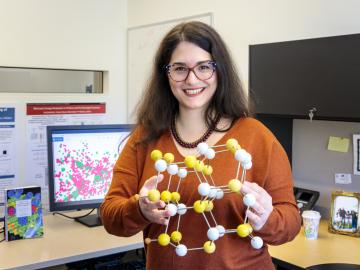
To advance sensor technologies, Oak Ridge National Laboratory researchers studied piezoelectric materials, which convert mechanical stress into electrical energy, to see how they could handle bombardment with energetic neutrons.
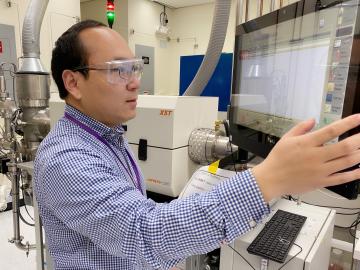
About 60 years ago, scientists discovered that a certain rare earth metal-hydrogen mixture, yttrium, could be the ideal moderator to go inside small, gas-cooled nuclear reactors.
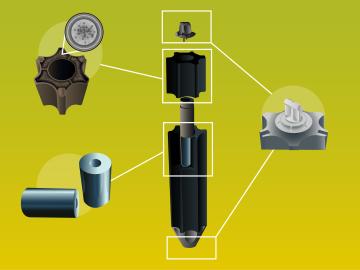
It’s a new type of nuclear reactor core. And the materials that will make it up are novel — products of Oak Ridge National Laboratory’s advanced materials and manufacturing technologies.
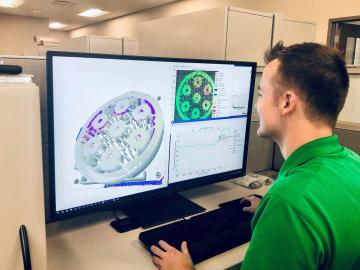
Oak Ridge National Laboratory researchers have developed artificial intelligence software for powder bed 3D printers that assesses the quality of parts in real time, without the need for expensive characterization equipment.
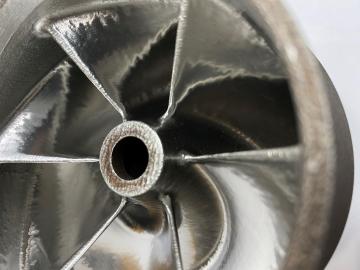
Scientists at the Department of Energy Manufacturing Demonstration Facility at ORNL have their eyes on the prize: the Transformational Challenge Reactor, or TCR, a microreactor built using 3D printing and other new approaches that will be up and running by 2023.

Researchers at the Department of Energy’s Oak Ridge National Laboratory are refining their design of a 3D-printed nuclear reactor core, scaling up the additive manufacturing process necessary to build it, and developing methods