
Filter News
Area of Research
- Advanced Manufacturing (23)
- Biology and Environment (85)
- Building Technologies (4)
- Clean Energy (128)
- Climate and Environmental Systems (1)
- Computational Biology (2)
- Computer Science (1)
- Electricity and Smart Grid (1)
- Functional Materials for Energy (2)
- Fusion and Fission (5)
- Fusion Energy (2)
- Isotopes (4)
- Materials (91)
- Materials Characterization (2)
- Materials for Computing (14)
- Materials Under Extremes (1)
- National Security (9)
- Neutron Science (22)
- Nuclear Science and Technology (4)
- Supercomputing (31)
News Topics
- (-) 3-D Printing/Advanced Manufacturing (128)
- (-) Biology (102)
- (-) Buildings (67)
- (-) Materials (149)
- Advanced Reactors (35)
- Artificial Intelligence (102)
- Big Data (62)
- Bioenergy (92)
- Biomedical (62)
- Biotechnology (24)
- Chemical Sciences (74)
- Clean Water (31)
- Climate Change (106)
- Composites (30)
- Computer Science (199)
- Coronavirus (46)
- Critical Materials (29)
- Cybersecurity (35)
- Decarbonization (85)
- Education (5)
- Element Discovery (1)
- Emergency (2)
- Energy Storage (112)
- Environment (201)
- Exascale Computing (44)
- Fossil Energy (6)
- Frontier (46)
- Fusion (59)
- Grid (67)
- High-Performance Computing (94)
- Hydropower (11)
- Irradiation (3)
- Isotopes (57)
- ITER (7)
- Machine Learning (51)
- Materials Science (149)
- Mathematics (10)
- Mercury (12)
- Microelectronics (4)
- Microscopy (51)
- Molten Salt (9)
- Nanotechnology (60)
- National Security (73)
- Net Zero (14)
- Neutron Science (140)
- Nuclear Energy (111)
- Partnerships (51)
- Physics (64)
- Polymers (33)
- Quantum Computing (38)
- Quantum Science (72)
- Renewable Energy (2)
- Security (26)
- Simulation (53)
- Software (1)
- Space Exploration (25)
- Statistics (3)
- Summit (61)
- Sustainable Energy (130)
- Transformational Challenge Reactor (7)
- Transportation (99)
Media Contacts
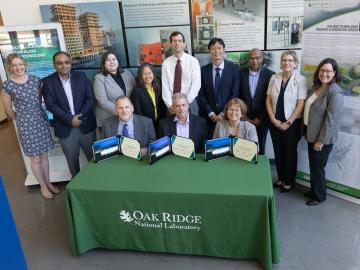
Flexcon Global has exclusively licensed two patented inventions to manufacture a self-healing barrier film from ORNL for research and development purposes. The film can be incorporated into vacuum insulation panels to increase the efficiency of buildings during retrofits. Under a cooperative research and development agreement that began in 2021, Flexcon and ORNL have been exploring the capabilities of the technology and fine-tuning its properties.
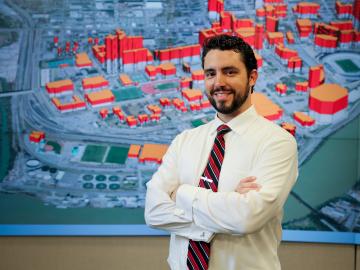
ORNL’s Joshua New was named the 2024 Researcher of the Year by R&D World magazine as part of its R&D 100 Professional Award winners.

A digital construction platform in development at Oak Ridge National Laboratory is boosting the retrofitting of building envelopes and giving builders the tools to automate the process from design to installation with the assistance of a cable-driven robotic crane.

At ORNL, a group of scientists used neutron scattering techniques to investigate a relatively new functional material called a Weyl semimetal. These Weyl fermions move very quickly in a material and can carry electrical charge at room temperature. Scientists think that Weyl semimetals, if used in future electronics, could allow electricity to flow more efficiently and enable more energy-efficient computers and other electronic devices.
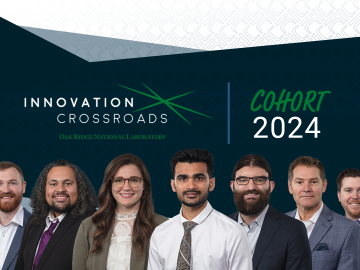
Seven entrepreneurs comprise the next cohort of Innovation Crossroads, a DOE Lab-Embedded Entrepreneurship Program node based at ORNL. The program provides energy-related startup founders from across the nation with access to ORNL’s unique scientific resources and capabilities, as well as connect them with experts, mentors and networks to accelerate their efforts to take their world-changing ideas to the marketplace.
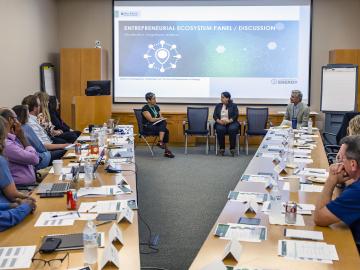
Five researchers at the Department of Energy’s Oak Ridge National Laboratory recently completed an eight-week pilot commercialization coaching program as part of Safari, a program funded by DOE’s Office of Technology Transitions, or OTT, Practices to Accelerate the Commercialization of Technologies, or PACT.
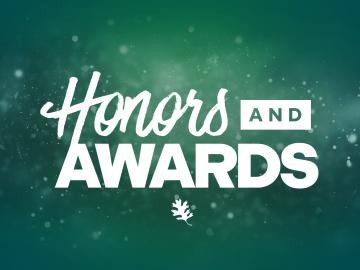
Two additive manufacturing researchers from ORNL received prestigious awards from national organizations. Amy Elliott and Nadim Hmeidat, who both work in the Manufacturing Science Division, were recognized recently for their early career accomplishments.

Brian Sanders is focused on impactful, multidisciplinary science at Oak Ridge National Laboratory, developing solutions for everything from improved imaging of plant-microbe interactions that influence ecosystem health to advancing new treatments for cancer and viral infections.
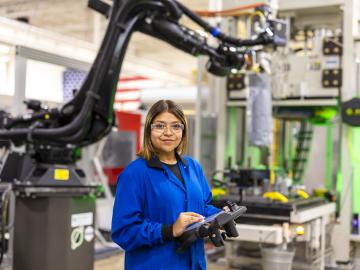
Brittany Rodriguez never imagined she would pursue a science career at a Department of Energy national laboratory. However, after some encouraging words from her mother, input from key mentors at the University of Texas Rio Grande Valley, or UTRGV, and a lot of hard work, Rodriguez landed at DOE’s Manufacturing Demonstration Facility, or MDF, at Oak Ridge National Laboratory.
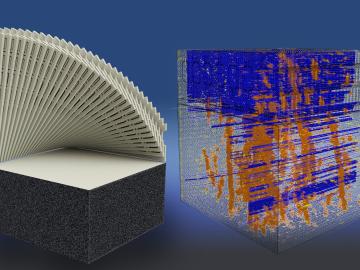
The Department of Energy’s Oak Ridge National Laboratory has publicly released a new set of additive manufacturing data that industry and researchers can use to evaluate and improve the quality of 3D-printed components. The breadth of the datasets can significantly boost efforts to verify the quality of additively manufactured parts using only information gathered during printing, without requiring expensive and time-consuming post-production analysis.