Filter News
Area of Research
- Advanced Manufacturing (22)
- Biology and Environment (27)
- Building Technologies (1)
- Clean Energy (153)
- Computational Engineering (1)
- Computer Science (2)
- Electricity and Smart Grid (1)
- Energy Sciences (1)
- Functional Materials for Energy (2)
- Fusion and Fission (6)
- Fusion Energy (1)
- Isotopes (1)
- Materials (61)
- Materials for Computing (7)
- Mathematics (1)
- National Security (4)
- Neutron Science (14)
- Nuclear Science and Technology (4)
- Supercomputing (12)
News Topics
- (-) 3-D Printing/Advanced Manufacturing (119)
- (-) Clean Water (29)
- (-) Composites (26)
- (-) Energy Storage (108)
- Advanced Reactors (34)
- Artificial Intelligence (91)
- Big Data (53)
- Bioenergy (91)
- Biology (98)
- Biomedical (58)
- Biotechnology (22)
- Buildings (57)
- Chemical Sciences (63)
- Climate Change (99)
- Computer Science (186)
- Coronavirus (46)
- Critical Materials (25)
- Cybersecurity (35)
- Decarbonization (78)
- Education (4)
- Element Discovery (1)
- Emergency (2)
- Environment (194)
- Exascale Computing (37)
- Fossil Energy (5)
- Frontier (42)
- Fusion (53)
- Grid (62)
- High-Performance Computing (84)
- Hydropower (11)
- Irradiation (3)
- Isotopes (52)
- ITER (7)
- Machine Learning (47)
- Materials (143)
- Materials Science (138)
- Mathematics (7)
- Mercury (12)
- Microelectronics (2)
- Microscopy (51)
- Molten Salt (8)
- Nanotechnology (60)
- National Security (60)
- Net Zero (13)
- Neutron Science (130)
- Nuclear Energy (106)
- Partnerships (42)
- Physics (59)
- Polymers (33)
- Quantum Computing (32)
- Quantum Science (67)
- Renewable Energy (2)
- Security (24)
- Simulation (46)
- Software (1)
- Space Exploration (25)
- Statistics (3)
- Summit (57)
- Sustainable Energy (125)
- Transformational Challenge Reactor (7)
- Transportation (95)
Media Contacts
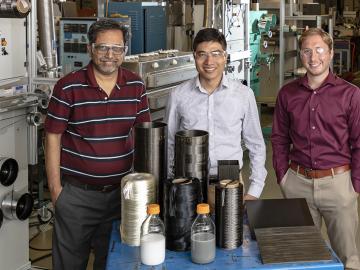
Carbon fiber composites—lightweight and strong—are great structural materials for automobiles, aircraft and other transportation vehicles. They consist of a polymer matrix, such as epoxy, into which reinforcing carbon fibers have been embedded. Because of differences in the mecha...
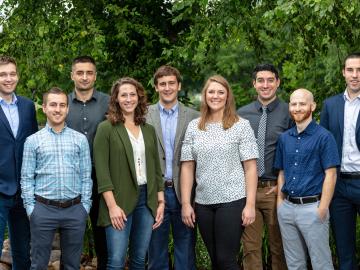
The next cohort of Innovation Crossroads fellows at Oak Ridge National Laboratory will receive support from the U.S. Department of Energy’s Advanced Manufacturing Office (AMO) and the Tennessee Valley Authority (TVA). Officials made the announcement today at th...
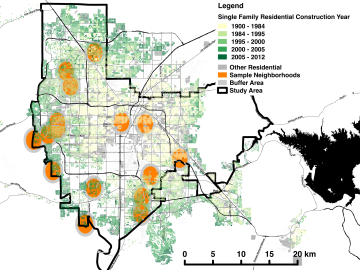
A team led by Oak Ridge National Laboratory has discovered that residents living in arid environments share a desire for water security, which can ultimately benefit entire neighborhoods. Las Vegas, Nevada’s water utility was the first utility in the United States to implement ...

The construction industry may soon benefit from 3D printed molds to make concrete facades, promising lower cost and production time. Researchers at Oak Ridge National Laboratory are evaluating the performance of 3D printed molds used to precast concrete facades in a 42-story buildin...
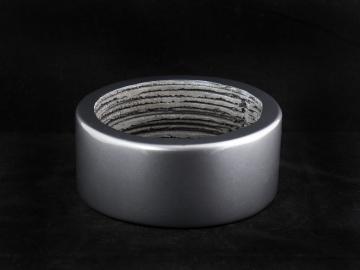
Oak Ridge National Laboratory scientists have improved a mixture of materials used to 3D print permanent magnets with increased density, which could yield longer lasting, better performing magnets for electric motors, sensors and vehicle applications. Building on previous research, ...
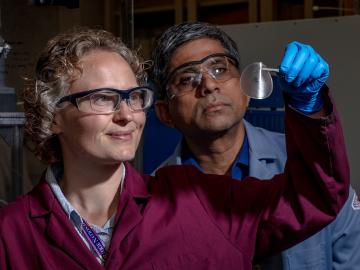
Oak Ridge National Laboratory scientists have developed a crucial component for a new kind of low-cost stationary battery system utilizing common materials and designed for grid-scale electricity storage. Large, economical electricity storage systems can benefit the nation’s grid ...
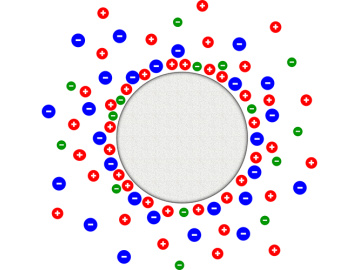
Energy storage could get a boost from new research of tailored liquid salt mixtures, the components of supercapacitors responsible for holding and releasing electrical energy. Oak Ridge National Laboratory’s Naresh Osti and his colleagues used neutrons at the lab’s Spallation Neutron ...
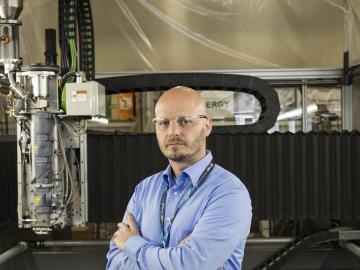
Vlastimil Kunc grew up in a family of scientists where his natural curiosity was encouraged—an experience that continues to drive his research today in polymer composite additive manufacturing at Oak Ridge National Laboratory. “I’ve been interested in the science of composites si...
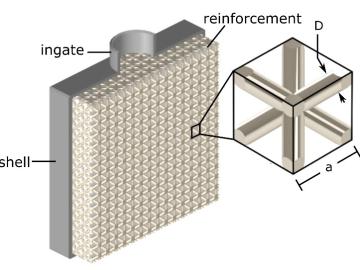
A new manufacturing method created by Oak Ridge National Laboratory and Rice University combines 3D printing with traditional casting to produce damage-tolerant components composed of multiple materials. Composite components made by pouring an aluminum alloy over a printed steel lattice showed an order of magnitude greater damage tolerance than aluminum alone.
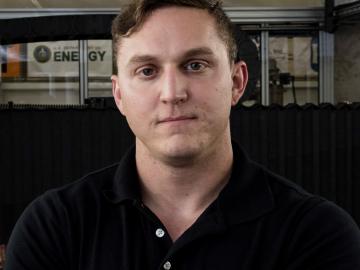
While serving in Kandahar, Afghanistan, U.S. Navy construction mechanic Matthew Sallas may not have imagined where his experience would take him next. But researchers at Oak Ridge National Laboratory certainly had the future in mind as they were creating programs to train men and wome...