Filter News
Area of Research
- Advanced Manufacturing (22)
- Biology and Environment (12)
- Building Technologies (1)
- Clean Energy (85)
- Fusion and Fission (8)
- Fusion Energy (7)
- Isotopes (1)
- Materials (26)
- Materials for Computing (5)
- National Security (13)
- Neutron Science (10)
- Nuclear Science and Technology (13)
- Nuclear Systems Modeling, Simulation and Validation (1)
- Sensors and Controls (1)
- Supercomputing (10)
News Topics
- (-) 3-D Printing/Advanced Manufacturing (119)
- (-) Advanced Reactors (34)
- (-) Fossil Energy (5)
- (-) Security (24)
- Artificial Intelligence (91)
- Big Data (53)
- Bioenergy (91)
- Biology (98)
- Biomedical (58)
- Biotechnology (22)
- Buildings (57)
- Chemical Sciences (63)
- Clean Water (29)
- Climate Change (99)
- Composites (26)
- Computer Science (186)
- Coronavirus (46)
- Critical Materials (25)
- Cybersecurity (35)
- Decarbonization (78)
- Education (4)
- Element Discovery (1)
- Emergency (2)
- Energy Storage (108)
- Environment (194)
- Exascale Computing (37)
- Frontier (42)
- Fusion (53)
- Grid (62)
- High-Performance Computing (84)
- Hydropower (11)
- Irradiation (3)
- Isotopes (52)
- ITER (7)
- Machine Learning (47)
- Materials (143)
- Materials Science (138)
- Mathematics (7)
- Mercury (12)
- Microelectronics (2)
- Microscopy (51)
- Molten Salt (8)
- Nanotechnology (60)
- National Security (60)
- Net Zero (13)
- Neutron Science (130)
- Nuclear Energy (106)
- Partnerships (42)
- Physics (59)
- Polymers (33)
- Quantum Computing (32)
- Quantum Science (67)
- Renewable Energy (2)
- Simulation (46)
- Software (1)
- Space Exploration (25)
- Statistics (3)
- Summit (57)
- Sustainable Energy (125)
- Transformational Challenge Reactor (7)
- Transportation (95)
Media Contacts

Scientists at ORNL have developed 3D-printed collimator techniques that can be used to custom design collimators that better filter out noise during different types of neutron scattering experiments
ORNL scientists have determined how to avoid costly and potentially irreparable damage to large metallic parts fabricated through additive manufacturing, also known as 3D printing, that is caused by residual stress in the material.
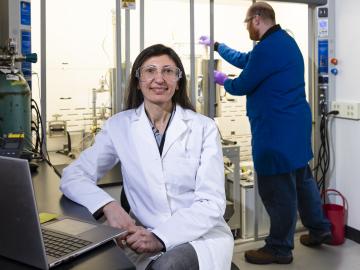
Canan Karakaya, a R&D Staff member in the Chemical Process Scale-Up group at ORNL, was inspired to become a chemical engineer after she experienced a magical transformation that turned ammonia gas into ammonium nitrate, turning a liquid into white flakes gently floating through the air.

SkyNano, an Innovation Crossroads alumnus, held a ribbon-cutting for their new facility. SkyNano exemplifies using DOE resources to build a successful clean energy company, making valuable carbon nanotubes from waste CO2.

An experiment by researchers at the Department of Energy’s Oak Ridge National Laboratory demonstrated advanced quantum-based cybersecurity can be realized in a deployed fiber link.
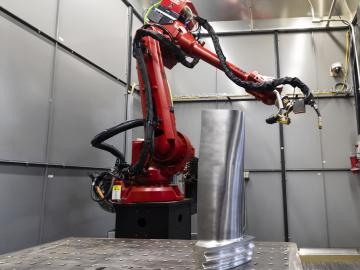
Researchers at ORNL became the first to 3D-print large rotating steam turbine blades for generating energy in power plants.

Four scientists affiliated with ORNL were named Battelle Distinguished Inventors during the lab’s annual Innovation Awards on Dec. 1 in recognition of being granted 14 or more United States patents.

Anne Campbell, a researcher at ORNL, recently won the Young Leaders Professional Development Award from the Minerals, Metals & Materials Society, or TMS, and has been chosen as the first recipient of the Young Leaders International Scholar Program award from TMS and the Korean Institute of Metals and Materials, or KIM.
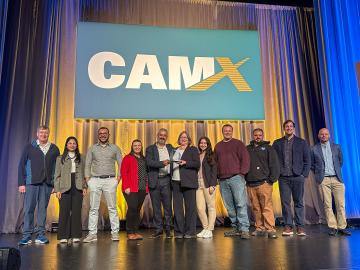
The Hub & Spoke Sustainable Materials & Manufacturing Alliance for Renewable Technologies, or SM2ART, program has been honored with the composites industry’s Combined Strength Award at the Composites and Advanced Materials Expo, or CAMX, 2023 in Atlanta. This distinction goes to the team that applies their knowledge, resources and talent to solve a problem by making the best use of composites materials.
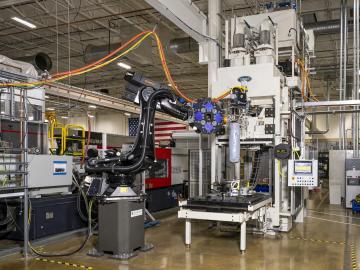
An Oak Ridge National Laboratory-developed advanced manufacturing technology, AMCM, was recently licensed by Orbital Composites and enables the rapid production of composite-based components, which could accelerate the decarbonization of vehicles