Filter News
Area of Research
- Advanced Manufacturing (12)
- Biology and Environment (60)
- Building Technologies (2)
- Clean Energy (140)
- Computational Engineering (2)
- Computer Science (12)
- Electricity and Smart Grid (3)
- Energy Sciences (1)
- Functional Materials for Energy (1)
- Fusion and Fission (10)
- Fusion Energy (4)
- Isotope Development and Production (1)
- Isotopes (2)
- Materials (105)
- Materials Characterization (1)
- Materials for Computing (18)
- Materials Under Extremes (1)
- Mathematics (1)
- National Security (24)
- Neutron Science (33)
- Nuclear Science and Technology (8)
- Quantum information Science (9)
- Sensors and Controls (1)
- Supercomputing (76)
- Transportation Systems (1)
News Topics
- (-) Clean Water (29)
- (-) Composites (26)
- (-) Exascale Computing (37)
- (-) Grid (62)
- (-) Machine Learning (47)
- (-) Materials Science (139)
- (-) Mathematics (7)
- (-) Molten Salt (8)
- (-) Quantum Science (68)
- (-) Statistics (3)
- (-) Sustainable Energy (125)
- 3-D Printing/Advanced Manufacturing (119)
- Advanced Reactors (34)
- Artificial Intelligence (91)
- Big Data (53)
- Bioenergy (91)
- Biology (98)
- Biomedical (58)
- Biotechnology (22)
- Buildings (57)
- Chemical Sciences (63)
- Climate Change (99)
- Computer Science (186)
- Coronavirus (46)
- Critical Materials (25)
- Cybersecurity (35)
- Decarbonization (79)
- Education (4)
- Element Discovery (1)
- Emergency (2)
- Energy Storage (108)
- Environment (194)
- Fossil Energy (5)
- Frontier (42)
- Fusion (53)
- High-Performance Computing (84)
- Hydropower (11)
- Irradiation (3)
- Isotopes (53)
- ITER (7)
- Materials (143)
- Mercury (12)
- Microelectronics (2)
- Microscopy (51)
- Nanotechnology (60)
- National Security (60)
- Net Zero (13)
- Neutron Science (131)
- Nuclear Energy (106)
- Partnerships (43)
- Physics (60)
- Polymers (33)
- Quantum Computing (33)
- Renewable Energy (2)
- Security (24)
- Simulation (46)
- Software (1)
- Space Exploration (25)
- Summit (57)
- Transformational Challenge Reactor (7)
- Transportation (96)
Media Contacts
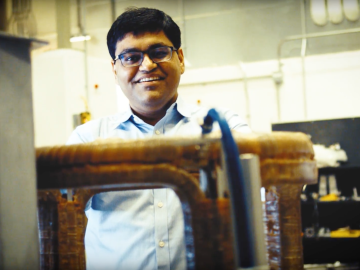
Raman. Heisenberg. Fermi. Wollan. From Kolkata to Göttingen, Chicago to Oak Ridge. Arnab Banerjee has literally walked in the footsteps of some of the greatest pioneers in physics history—and he’s forging his own trail along the way. Banerjee is a staff scientist working in the Neu...
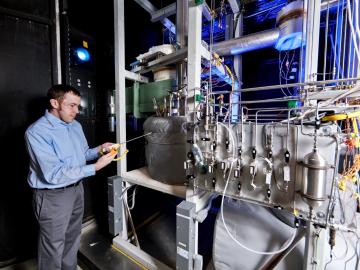
Thanks in large part to developing and operating a facility for testing molten salt reactor (MSR) technologies, nuclear experts at the Energy Department’s Oak Ridge National Laboratory (ORNL) are now tackling the next generation of another type of clean energy—concentrating ...
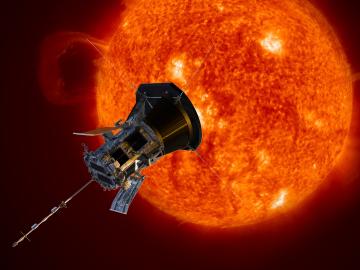
A shield assembly that protects an instrument measuring ion and electron fluxes for a NASA mission to touch the Sun was tested in extreme experimental environments at Oak Ridge National Laboratory—and passed with flying colors. Components aboard Parker Solar Probe, which will endure th...
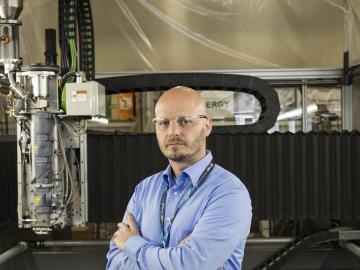
Vlastimil Kunc grew up in a family of scientists where his natural curiosity was encouraged—an experience that continues to drive his research today in polymer composite additive manufacturing at Oak Ridge National Laboratory. “I’ve been interested in the science of composites si...
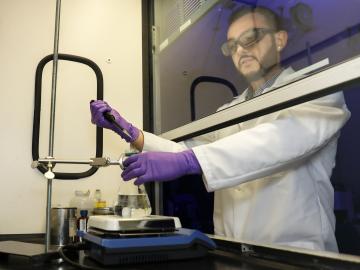
A novel method developed at Oak Ridge National Laboratory creates supertough renewable plastic with improved manufacturability. Working with polylactic acid, a biobased plastic often used in packaging, textiles, biomedical implants and 3D printing, the research team added tiny amo...
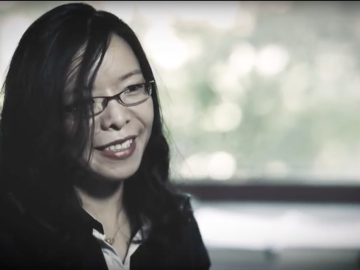
Material surfaces and interfaces may appear flat and void of texture to the naked eye, but a view from the nanoscale reveals an intricate tapestry of atomic patterns that control the reactions between the material and its environment. Electron microscopy allows researchers to probe...
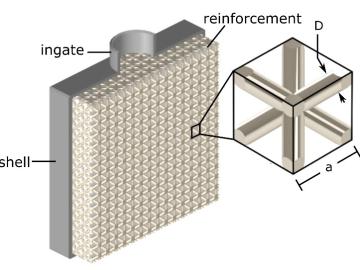
A new manufacturing method created by Oak Ridge National Laboratory and Rice University combines 3D printing with traditional casting to produce damage-tolerant components composed of multiple materials. Composite components made by pouring an aluminum alloy over a printed steel lattice showed an order of magnitude greater damage tolerance than aluminum alone.
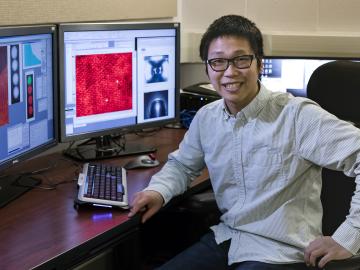
Researchers have long sought electrically conductive materials for economical energy-storage devices. Two-dimensional (2D) ceramics called MXenes are contenders. Unlike most 2D ceramics, MXenes have inherently good conductivity because they are molecular sheets made from the carbides ...
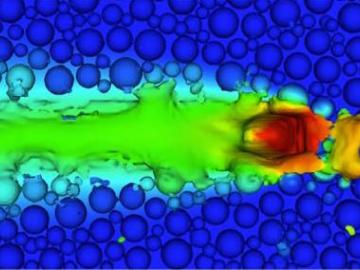
Oak Ridge National Laboratory experts are playing leading roles in the recently established Department of Energy’s (DOE’s) Exascale Computing Project (ECP), a multi-lab initiative responsible for developing the strategy, aligning the resources, and conducting the R&D necessary to achieve the nation’s imperative of delivering exascale computing by 2021.
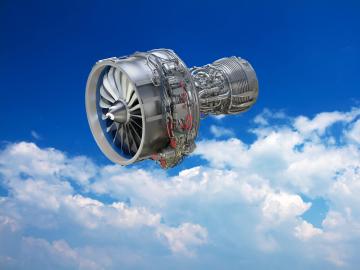
Ceramic matrix composite (CMC) materials are made of coated ceramic fibers surrounded by a ceramic matrix. They are tough, lightweight and capable of withstanding temperatures 300–400 degrees F hotter than metal alloys can endure. If certain components were made with CMCs instead o...