Filter News
Area of Research
- (-) Advanced Manufacturing (22)
- (-) Fusion and Fission (29)
- (-) Transportation Systems (2)
- Biology and Environment (40)
- Building Technologies (1)
- Clean Energy (163)
- Computational Biology (2)
- Computational Engineering (3)
- Computer Science (7)
- Electricity and Smart Grid (1)
- Fuel Cycle Science and Technology (1)
- Functional Materials for Energy (1)
- Fusion Energy (11)
- Isotope Development and Production (1)
- Isotopes (25)
- Materials (71)
- Materials for Computing (10)
- Mathematics (1)
- National Security (35)
- Neutron Science (25)
- Nuclear Science and Technology (38)
- Nuclear Systems Modeling, Simulation and Validation (1)
- Quantum information Science (2)
- Supercomputing (86)
News Topics
- (-) 3-D Printing/Advanced Manufacturing (25)
- (-) Artificial Intelligence (2)
- (-) Cybersecurity (1)
- (-) Isotopes (1)
- (-) Nuclear Energy (28)
- (-) Transportation (4)
- Advanced Reactors (7)
- Bioenergy (2)
- Biology (1)
- Biomedical (1)
- Buildings (1)
- Chemical Sciences (4)
- Composites (4)
- Computer Science (3)
- Critical Materials (1)
- Decarbonization (3)
- Energy Storage (4)
- Environment (2)
- Exascale Computing (1)
- Fossil Energy (1)
- Frontier (1)
- Fusion (23)
- Grid (2)
- High-Performance Computing (2)
- ITER (6)
- Machine Learning (1)
- Materials (7)
- Materials Science (10)
- Microscopy (1)
- Nanotechnology (1)
- Net Zero (1)
- Neutron Science (3)
- Partnerships (3)
- Physics (1)
- Security (2)
- Simulation (3)
- Space Exploration (2)
- Sustainable Energy (9)
- Transformational Challenge Reactor (1)
Media Contacts
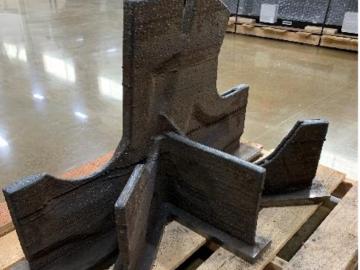
Oak Ridge National Laboratory researchers recently used large-scale additive manufacturing with metal to produce a full-strength steel component for a wind turbine, proving the technique as a viable alternative to
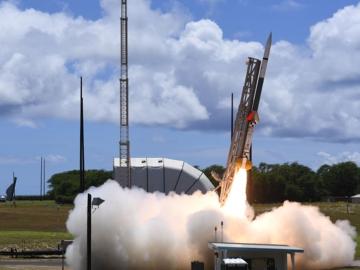
Oak Ridge National Laboratory researchers have developed a novel process to manufacture extreme heat resistant carbon-carbon composites. The performance of these materials will be tested in a U.S. Navy rocket that NASA will launch this fall.
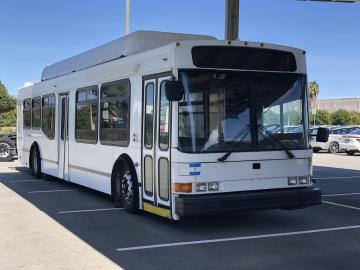
Oak Ridge National Laboratory researchers developed and demonstrated algorithm-based controls for a hybrid electric bus that yielded up to 30% energy savings compared with existing controls.
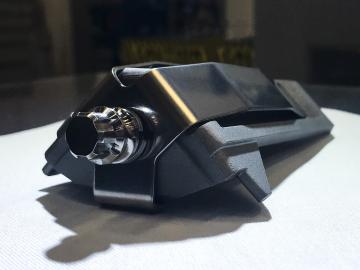
Four first-of-a-kind 3D-printed fuel assembly brackets, produced at the Department of Energy’s Manufacturing Demonstration Facility at Oak Ridge National Laboratory, have been installed and are now under routine operating

A research team at Oak Ridge National Laboratory have 3D printed a thermal protection shield, or TPS, for a capsule that will launch with the Cygnus cargo spacecraft as part of the supply mission to the International Space Station.
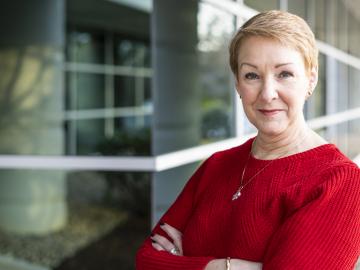
Kathy McCarthy, associate laboratory director for Fusion and Fission Energy and Science at the Department of Energy’s Oak Ridge National Laboratory, has been elected fellow of the American Nuclear Society for her nationally and internationally recognized leadership in nuclear energy and fusion.
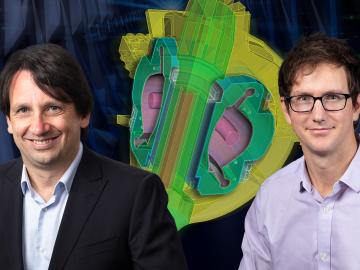
Oak Ridge National Laboratory expertise in fission and fusion has come together to form a new collaboration, the Fusion Energy Reactor Models Integrator, or FERMI
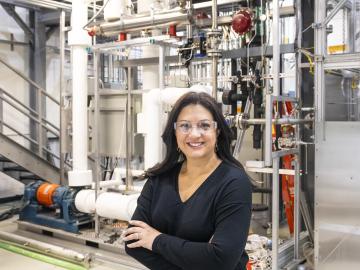
Toward the goal of bringing the next generation of nuclear power reactor technology online this decade, ORNL and Analysis and Measurement Services Corporation have successfully completed loop testing of instrument and control sensors for an advanced reactor design for small modular reactors.
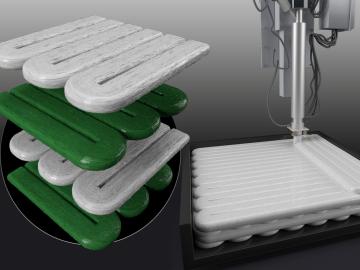
Oak Ridge National Laboratory researchers combined additive manufacturing with conventional compression molding to produce high-performance thermoplastic composites reinforced with short carbon fibers.

A team of Oak Ridge National Laboratory researchers demonstrated that an additively manufactured hot stamping die – a tool used to create car body components – cooled faster than those produced by conventional manufacturing methods.