Filter News
Area of Research
- (-) Advanced Manufacturing (22)
- (-) Fusion and Fission (5)
- (-) Mathematics (1)
- (-) Neutron Science (23)
- Biological Systems (2)
- Biology and Environment (132)
- Biology and Soft Matter (1)
- Building Technologies (1)
- Clean Energy (151)
- Climate and Environmental Systems (5)
- Computational Biology (1)
- Computational Engineering (3)
- Computer Science (6)
- Electricity and Smart Grid (1)
- Functional Materials for Energy (1)
- Fusion Energy (2)
- Isotopes (1)
- Materials (45)
- Materials for Computing (6)
- National Security (22)
- Nuclear Science and Technology (6)
- Quantum information Science (1)
- Supercomputing (77)
News Topics
- (-) 3-D Printing/Advanced Manufacturing (29)
- (-) Bioenergy (8)
- (-) Environment (11)
- (-) Machine Learning (4)
- (-) Summit (6)
- Advanced Reactors (8)
- Artificial Intelligence (8)
- Big Data (2)
- Biology (5)
- Biomedical (12)
- Biotechnology (1)
- Buildings (1)
- Chemical Sciences (6)
- Clean Water (3)
- Climate Change (2)
- Composites (5)
- Computer Science (16)
- Coronavirus (8)
- Critical Materials (1)
- Cybersecurity (2)
- Decarbonization (4)
- Energy Storage (10)
- Exascale Computing (1)
- Fossil Energy (2)
- Frontier (2)
- Fusion (23)
- Grid (2)
- High-Performance Computing (4)
- Isotopes (1)
- ITER (6)
- Materials (18)
- Materials Science (28)
- Mathematics (2)
- Microscopy (4)
- Nanotechnology (11)
- National Security (2)
- Net Zero (1)
- Neutron Science (99)
- Nuclear Energy (31)
- Partnerships (3)
- Physics (10)
- Polymers (1)
- Quantum Computing (1)
- Quantum Science (7)
- Security (3)
- Simulation (3)
- Space Exploration (4)
- Sustainable Energy (11)
- Transformational Challenge Reactor (1)
- Transportation (7)
Media Contacts

Scientists at ORNL have developed 3D-printed collimator techniques that can be used to custom design collimators that better filter out noise during different types of neutron scattering experiments

In fiscal year 2023 — Oct. 1–Sept. 30, 2023 — Oak Ridge National Laboratory was awarded more than $8 million in technology maturation funding through the Department of Energy’s Technology Commercialization Fund, or TCF.
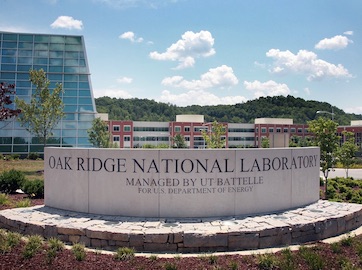
The Department of Energy’s Office of Science has selected three ORNL research teams to receive funding through DOE’s new Biopreparedness Research Virtual Environment initiative.
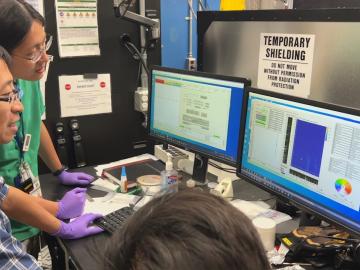
Neutron experiments can take days to complete, requiring researchers to work long shifts to monitor progress and make necessary adjustments. But thanks to advances in artificial intelligence and machine learning, experiments can now be done remotely and in half the time.
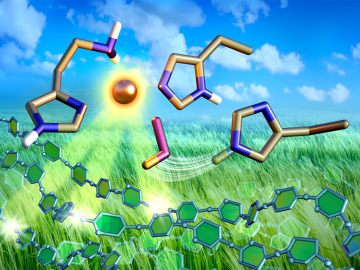
Nonfood, plant-based biofuels have potential as a green alternative to fossil fuels, but the enzymes required for production are too inefficient and costly to produce. However, new research is shining a light on enzymes from fungi that could make biofuels economically viable.
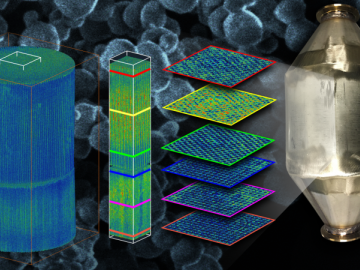
Natural gas furnaces not only heat your home, they also produce a lot of pollution. Even modern high-efficiency condensing furnaces produce significant amounts of corrosive acidic condensation and unhealthy levels of nitrogen oxides
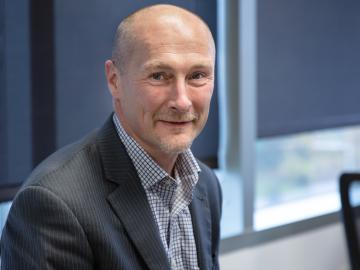
Paul Langan will join ORNL in the spring as associate laboratory director for the Biological and Environmental Systems Science Directorate.

Researchers in the geothermal energy industry are joining forces with fusion experts at ORNL to repurpose gyrotron technology, a tool used in fusion. Gyrotrons produce high-powered microwaves to heat up fusion plasmas.

ORNL researchers used the nation’s fastest supercomputer to map the molecular vibrations of an important but little-studied uranium compound produced during the nuclear fuel cycle for results that could lead to a cleaner, safer world.
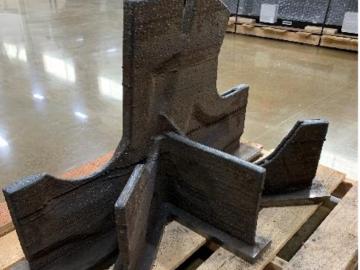
Oak Ridge National Laboratory researchers recently used large-scale additive manufacturing with metal to produce a full-strength steel component for a wind turbine, proving the technique as a viable alternative to