
Filter News
Area of Research
- (-) Clean Energy (26)
- (-) Nuclear Systems Modeling, Simulation and Validation (1)
- Advanced Manufacturing (4)
- Biology and Environment (18)
- Computational Biology (2)
- Computational Engineering (2)
- Computer Science (7)
- Electricity and Smart Grid (1)
- Fuel Cycle Science and Technology (1)
- Functional Materials for Energy (1)
- Fusion and Fission (28)
- Fusion Energy (11)
- Isotope Development and Production (1)
- Isotopes (25)
- Materials (40)
- Materials for Computing (2)
- National Security (33)
- Neutron Science (15)
- Nuclear Science and Technology (38)
- Quantum information Science (2)
- Supercomputing (80)
News Topics
- (-) Artificial Intelligence (8)
- (-) Cybersecurity (8)
- (-) Isotopes (1)
- (-) Nuclear Energy (8)
- (-) Summit (4)
- 3-D Printing/Advanced Manufacturing (78)
- Advanced Reactors (7)
- Big Data (5)
- Bioenergy (26)
- Biology (11)
- Biomedical (6)
- Biotechnology (4)
- Buildings (36)
- Chemical Sciences (14)
- Clean Water (8)
- Climate Change (21)
- Composites (17)
- Computer Science (25)
- Coronavirus (12)
- Critical Materials (9)
- Decarbonization (33)
- Energy Storage (72)
- Environment (54)
- Exascale Computing (2)
- Fossil Energy (2)
- Frontier (2)
- Fusion (1)
- Grid (40)
- High-Performance Computing (6)
- Hydropower (2)
- Machine Learning (7)
- Materials (35)
- Materials Science (26)
- Mathematics (2)
- Mercury (3)
- Microelectronics (1)
- Microscopy (8)
- Molten Salt (1)
- Nanotechnology (8)
- National Security (5)
- Net Zero (3)
- Neutron Science (11)
- Partnerships (12)
- Physics (1)
- Polymers (11)
- Quantum Science (2)
- Renewable Energy (1)
- Security (6)
- Simulation (4)
- Space Exploration (3)
- Statistics (1)
- Sustainable Energy (69)
- Transformational Challenge Reactor (3)
- Transportation (65)
Media Contacts
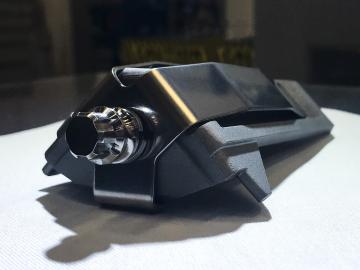
Four first-of-a-kind 3D-printed fuel assembly brackets, produced at the Department of Energy’s Manufacturing Demonstration Facility at Oak Ridge National Laboratory, have been installed and are now under routine operating
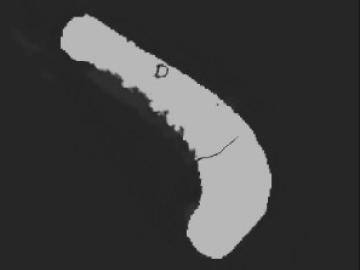
Algorithms developed at Oak Ridge National Laboratory can greatly enhance X-ray computed tomography images of 3D-printed metal parts, resulting in more accurate, faster scans.
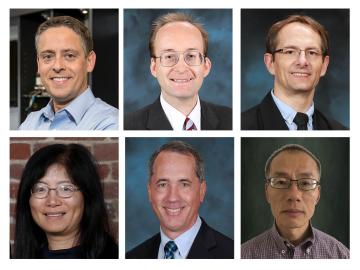
Six scientists at the Department of Energy’s Oak Ridge National Laboratory were named Battelle Distinguished Inventors, in recognition of obtaining 14 or more patents during their careers at the lab.

Researchers at Oak Ridge National Laboratory are developing a first-of-a-kind toolkit drawing on video game development software to visualize radiation data.
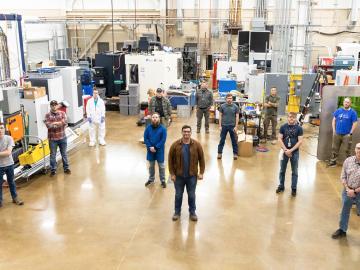
The University of Texas at San Antonio (UTSA) has formally launched the Cybersecurity Manufacturing Innovation Institute (CyManII), a $111 million public-private partnership.
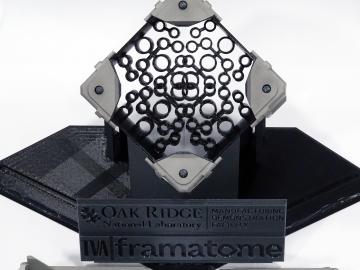
The Transformational Challenge Reactor, or TCR, a microreactor built using 3D printing and other new advanced technologies, could be operational by 2024.
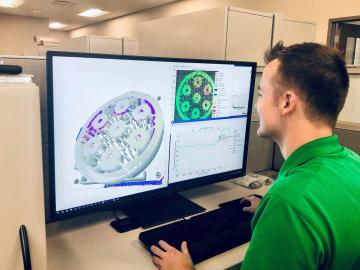
Oak Ridge National Laboratory researchers have developed artificial intelligence software for powder bed 3D printers that assesses the quality of parts in real time, without the need for expensive characterization equipment.
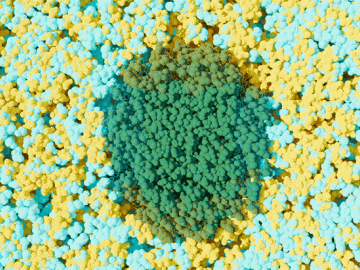
Scientists at ORNL used neutron scattering and supercomputing to better understand how an organic solvent and water work together to break down plant biomass, creating a pathway to significantly improve the production of renewable

Ada Sedova’s journey to Oak Ridge National Laboratory has taken her on the path from pre-med studies in college to an accelerated graduate career in mathematics and biophysics and now to the intersection of computational science and biology

Researchers at the Department of Energy’s Oak Ridge National Laboratory are refining their design of a 3D-printed nuclear reactor core, scaling up the additive manufacturing process necessary to build it, and developing methods