Filter News
Area of Research
- (-) Biology and Soft Matter (1)
- (-) Building Technologies (1)
- (-) Fusion Energy (2)
- (-) Isotopes (2)
- Advanced Manufacturing (22)
- Biological Systems (2)
- Biology and Environment (135)
- Clean Energy (207)
- Climate and Environmental Systems (5)
- Computational Biology (2)
- Computational Engineering (3)
- Computer Science (10)
- Electricity and Smart Grid (1)
- Energy Sciences (1)
- Functional Materials for Energy (2)
- Fusion and Fission (8)
- Materials (76)
- Materials for Computing (9)
- Mathematics (1)
- National Security (30)
- Neutron Science (33)
- Nuclear Science and Technology (6)
- Quantum information Science (1)
- Supercomputing (98)
News Topics
- (-) 3-D Printing/Advanced Manufacturing (2)
- (-) Energy Storage (1)
- (-) Environment (2)
- (-) Summit (1)
- Advanced Reactors (7)
- Biomedical (5)
- Buildings (3)
- Chemical Sciences (1)
- Climate Change (2)
- Computer Science (4)
- Decarbonization (1)
- Frontier (1)
- Fusion (13)
- Irradiation (1)
- Isotopes (24)
- Materials (5)
- Materials Science (4)
- National Security (1)
- Nuclear Energy (13)
- Security (1)
- Space Exploration (4)
- Sustainable Energy (4)
Media Contacts
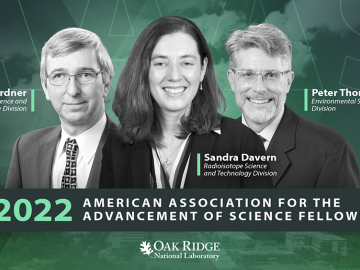
Three scientists from the Department of Energy’s Oak Ridge National Laboratory have been elected fellows of the American Association for the Advancement of Science, or AAAS.
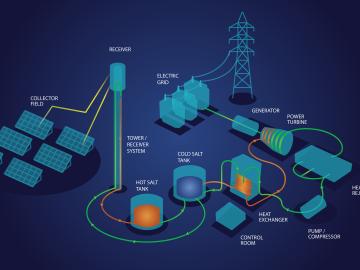
Oak Ridge National Laboratory scientists recently demonstrated a low-temperature, safe route to purifying molten chloride salts that minimizes their ability to corrode metals. This method could make the salts useful for storing energy generated from the sun’s heat.

ORNL biogeochemist Elizabeth Herndon is working with colleagues to investigate a piece of the puzzle that has received little attention thus far: the role of manganese in the carbon cycle.
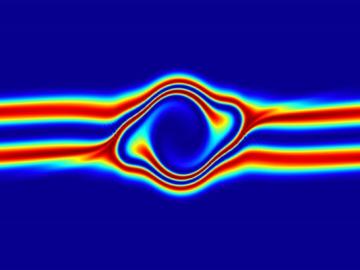
The prospect of simulating a fusion plasma is a step closer to reality thanks to a new computational tool developed by scientists in fusion physics, computer science and mathematics at ORNL.
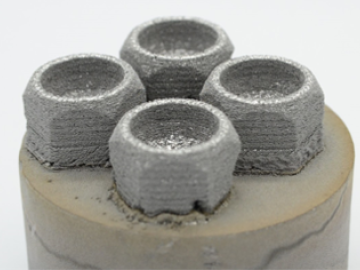
Using additive manufacturing, scientists experimenting with tungsten at Oak Ridge National Laboratory hope to unlock new potential of the high-performance heat-transferring material used to protect components from the plasma inside a fusion reactor. Fusion requires hydrogen isotopes to reach millions of degrees.

The construction industry may soon benefit from 3D printed molds to make concrete facades, promising lower cost and production time. Researchers at Oak Ridge National Laboratory are evaluating the performance of 3D printed molds used to precast concrete facades in a 42-story buildin...