Filter News
Area of Research
- (-) Advanced Manufacturing (5)
- (-) Nuclear Science and Technology (10)
- Biological Systems (2)
- Biology and Environment (69)
- Clean Energy (112)
- Computational Biology (2)
- Computational Engineering (2)
- Computer Science (4)
- Fusion and Fission (5)
- Isotopes (5)
- Materials (61)
- Materials for Computing (13)
- National Security (12)
- Neutron Science (24)
- Quantum information Science (2)
- Supercomputing (50)
- Transportation Systems (2)
News Topics
- (-) Bioenergy (2)
- (-) Biomedical (2)
- (-) Composites (3)
- (-) Molten Salt (4)
- (-) Transformational Challenge Reactor (4)
- 3-D Printing/Advanced Manufacturing (25)
- Advanced Reactors (12)
- Artificial Intelligence (1)
- Computer Science (3)
- Coronavirus (1)
- Cybersecurity (2)
- Decarbonization (1)
- Environment (1)
- Fusion (9)
- Isotopes (5)
- Machine Learning (1)
- Materials (6)
- Materials Science (8)
- Neutron Science (7)
- Nuclear Energy (37)
- Physics (2)
- Space Exploration (6)
- Sustainable Energy (6)
Media Contacts

A research team at Oak Ridge National Laboratory have 3D printed a thermal protection shield, or TPS, for a capsule that will launch with the Cygnus cargo spacecraft as part of the supply mission to the International Space Station.
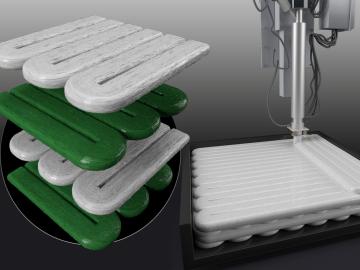
Oak Ridge National Laboratory researchers combined additive manufacturing with conventional compression molding to produce high-performance thermoplastic composites reinforced with short carbon fibers.
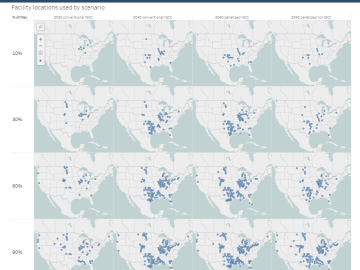
The combination of bioenergy with carbon capture and storage could cost-effectively sequester hundreds of millions of metric tons per year of carbon dioxide in the United States, making it a competitive solution for carbon management, according to a new analysis by ORNL scientists.
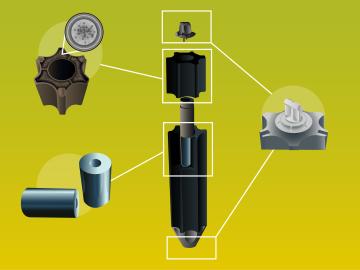
It’s a new type of nuclear reactor core. And the materials that will make it up are novel — products of Oak Ridge National Laboratory’s advanced materials and manufacturing technologies.
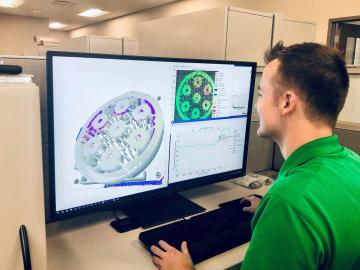
Oak Ridge National Laboratory researchers have developed artificial intelligence software for powder bed 3D printers that assesses the quality of parts in real time, without the need for expensive characterization equipment.
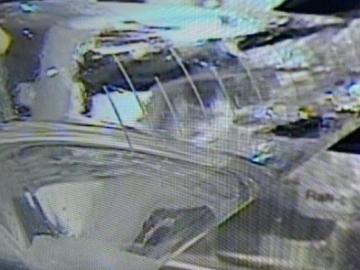
Oak Ridge National Laboratory researchers have discovered a better way to separate actinium-227, a rare isotope essential for an FDA-approved cancer treatment.
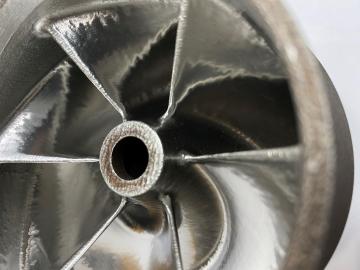
Scientists at the Department of Energy Manufacturing Demonstration Facility at ORNL have their eyes on the prize: the Transformational Challenge Reactor, or TCR, a microreactor built using 3D printing and other new approaches that will be up and running by 2023.

Researchers at the Department of Energy’s Oak Ridge National Laboratory are refining their design of a 3D-printed nuclear reactor core, scaling up the additive manufacturing process necessary to build it, and developing methods
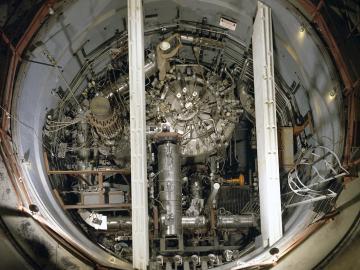
In the 1960s, Oak Ridge National Laboratory's four-year Molten Salt Reactor Experiment tested the viability of liquid fuel reactors for commercial power generation. Results from that historic experiment recently became the basis for the first-ever molten salt reactor benchmark.
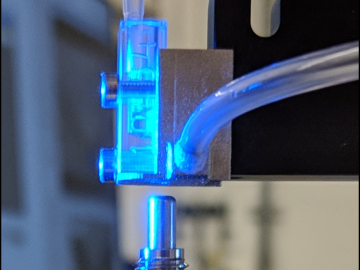
Researchers at the Department of Energy’s Oak Ridge National Laboratory have received five 2019 R&D 100 Awards, increasing the lab’s total to 221 since the award’s inception in 1963.