Filter News
Area of Research
- (-) Advanced Manufacturing (6)
- (-) Materials for Computing (4)
- Biological Systems (2)
- Biology and Environment (88)
- Biology and Soft Matter (1)
- Clean Energy (76)
- Climate and Environmental Systems (2)
- Computational Biology (1)
- Computational Engineering (2)
- Computer Science (6)
- Electricity and Smart Grid (1)
- Functional Materials for Energy (1)
- Fusion and Fission (11)
- Fusion Energy (7)
- Isotopes (25)
- Materials (45)
- Mathematics (1)
- National Security (24)
- Neutron Science (16)
- Nuclear Science and Technology (17)
- Nuclear Systems Modeling, Simulation and Validation (1)
- Quantum information Science (1)
- Sensors and Controls (1)
- Supercomputing (63)
News Topics
- (-) Advanced Reactors (1)
- (-) Artificial Intelligence (1)
- (-) Bioenergy (2)
- (-) Climate Change (1)
- (-) Composites (4)
- (-) Isotopes (1)
- (-) Security (1)
- 3-D Printing/Advanced Manufacturing (26)
- Biology (1)
- Biomedical (2)
- Chemical Sciences (4)
- Computer Science (8)
- Coronavirus (3)
- Cybersecurity (1)
- Decarbonization (1)
- Energy Storage (4)
- Environment (1)
- Fusion (1)
- Machine Learning (1)
- Materials (16)
- Materials Science (20)
- Microscopy (4)
- Nanotechnology (7)
- National Security (1)
- Neutron Science (7)
- Nuclear Energy (2)
- Polymers (6)
- Quantum Computing (1)
- Quantum Science (3)
- Simulation (1)
- Space Exploration (2)
- Summit (1)
- Sustainable Energy (10)
- Transformational Challenge Reactor (1)
- Transportation (5)
Media Contacts
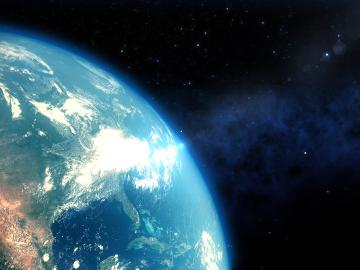
Tackling the climate crisis and achieving an equitable clean energy future are among the biggest challenges of our time.
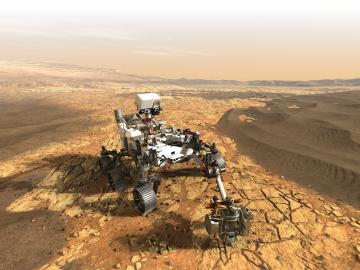
More than 50 current employees and recent retirees from ORNL received Department of Energy Secretary’s Honor Awards from Secretary Jennifer Granholm in January as part of project teams spanning the national laboratory system. The annual awards recognized 21 teams and three individuals for service and contributions to DOE’s mission and to the benefit of the nation.
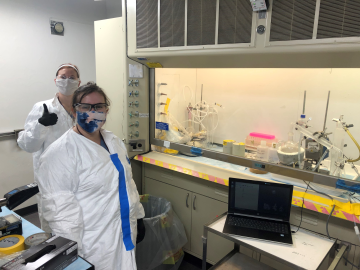
In experiment after experiment, the synthetic radioisotope actinium-225 has shown promise for targeting and attacking certain types of cancer cells.
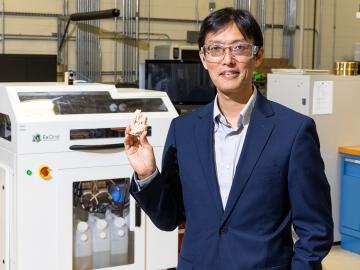
Researchers at ORNL designed a novel polymer to bind and strengthen silica sand for binder jet additive manufacturing, a 3D-printing method used by industries for prototyping and part production.

A research team at Oak Ridge National Laboratory have 3D printed a thermal protection shield, or TPS, for a capsule that will launch with the Cygnus cargo spacecraft as part of the supply mission to the International Space Station.
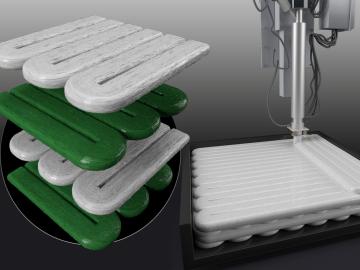
Oak Ridge National Laboratory researchers combined additive manufacturing with conventional compression molding to produce high-performance thermoplastic composites reinforced with short carbon fibers.
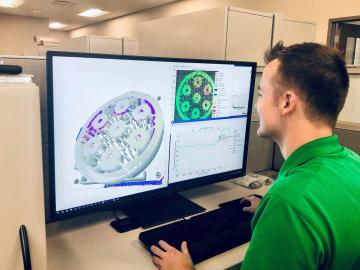
Oak Ridge National Laboratory researchers have developed artificial intelligence software for powder bed 3D printers that assesses the quality of parts in real time, without the need for expensive characterization equipment.
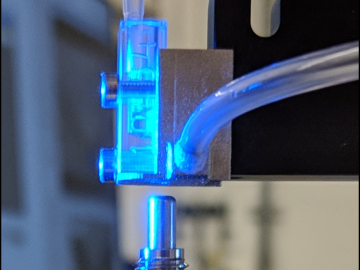
Researchers at the Department of Energy’s Oak Ridge National Laboratory have received five 2019 R&D 100 Awards, increasing the lab’s total to 221 since the award’s inception in 1963.
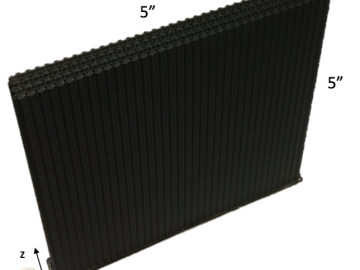
A team including Oak Ridge National Laboratory and University of Tennessee researchers demonstrated a novel 3D printing approach called Z-pinning that can increase the material’s strength and toughness by more than three and a half times compared to conventional additive manufacturing processes.
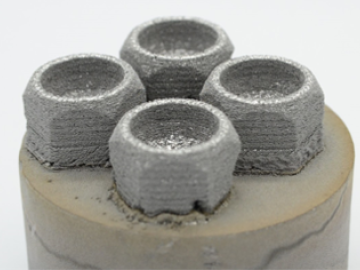
Using additive manufacturing, scientists experimenting with tungsten at Oak Ridge National Laboratory hope to unlock new potential of the high-performance heat-transferring material used to protect components from the plasma inside a fusion reactor. Fusion requires hydrogen isotopes to reach millions of degrees.