Filter News
Area of Research
- (-) Advanced Manufacturing (7)
- (-) Computer Science (8)
- Biology and Environment (60)
- Biology and Soft Matter (1)
- Clean Energy (101)
- Climate and Environmental Systems (2)
- Computational Biology (1)
- Computational Engineering (2)
- Electricity and Smart Grid (3)
- Functional Materials for Energy (1)
- Fusion and Fission (11)
- Fusion Energy (7)
- Isotopes (2)
- Materials (58)
- Materials for Computing (8)
- Mathematics (1)
- National Security (30)
- Neutron Science (103)
- Nuclear Science and Technology (15)
- Nuclear Systems Modeling, Simulation and Validation (1)
- Quantum information Science (1)
- Sensors and Controls (2)
- Supercomputing (69)
News Topics
- (-) Advanced Reactors (1)
- (-) Artificial Intelligence (7)
- (-) Composites (3)
- (-) Grid (2)
- (-) Neutron Science (2)
- 3-D Printing/Advanced Manufacturing (22)
- Big Data (4)
- Bioenergy (1)
- Buildings (1)
- Computer Science (16)
- Cybersecurity (2)
- Energy Storage (2)
- Environment (1)
- Exascale Computing (1)
- Fusion (1)
- High-Performance Computing (2)
- Machine Learning (5)
- Materials (6)
- Materials Science (6)
- Nuclear Energy (2)
- Quantum Science (3)
- Space Exploration (1)
- Summit (1)
- Sustainable Energy (7)
- Transformational Challenge Reactor (1)
Media Contacts

Scientists at ORNL have developed 3D-printed collimator techniques that can be used to custom design collimators that better filter out noise during different types of neutron scattering experiments

ORNL is home to the world's fastest exascale supercomputer, Frontier, which was built in part to facilitate energy-efficient and scalable AI-based algorithms and simulations.
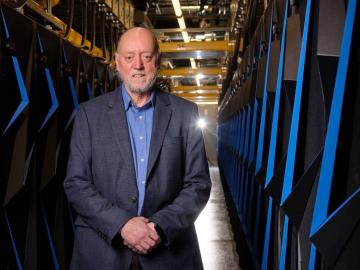
A force within the supercomputing community, Jack Dongarra developed software packages that became standard in the industry, allowing high-performance computers to become increasingly more powerful in recent decades.

Oak Ridge National Laboratory, University of Tennessee and University of Central Florida researchers released a new high-performance computing code designed to more efficiently examine

A research team at Oak Ridge National Laboratory have 3D printed a thermal protection shield, or TPS, for a capsule that will launch with the Cygnus cargo spacecraft as part of the supply mission to the International Space Station.
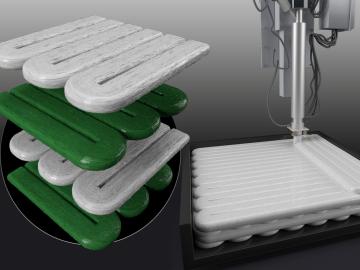
Oak Ridge National Laboratory researchers combined additive manufacturing with conventional compression molding to produce high-performance thermoplastic composites reinforced with short carbon fibers.

The ExOne Company, the global leader in industrial sand and metal 3D printers using binder jetting technology, announced it has reached a commercial license agreement with Oak Ridge National Laboratory to 3D print parts in aluminum-infiltrated boron carbide.
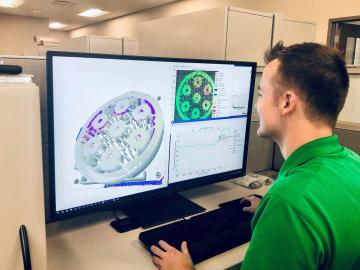
Oak Ridge National Laboratory researchers have developed artificial intelligence software for powder bed 3D printers that assesses the quality of parts in real time, without the need for expensive characterization equipment.
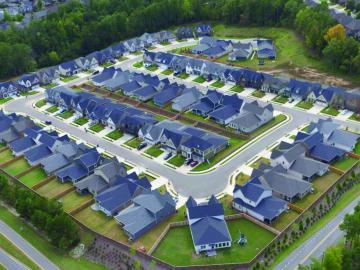
To better determine the potential energy cost savings among connected homes, researchers at Oak Ridge National Laboratory developed a computer simulation to more accurately compare energy use on similar weather days.
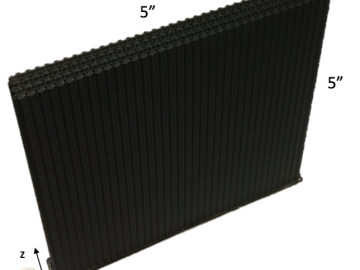
A team including Oak Ridge National Laboratory and University of Tennessee researchers demonstrated a novel 3D printing approach called Z-pinning that can increase the material’s strength and toughness by more than three and a half times compared to conventional additive manufacturing processes.