Filter News
Area of Research
- (-) Clean Energy (15)
- (-) Computer Science (6)
- Advanced Manufacturing (3)
- Biology and Environment (9)
- Computational Biology (1)
- Computational Engineering (1)
- Electricity and Smart Grid (1)
- Fuel Cycle Science and Technology (1)
- Functional Materials for Energy (1)
- Fusion and Fission (28)
- Fusion Energy (12)
- Isotope Development and Production (1)
- Isotopes (3)
- Materials (24)
- National Security (17)
- Neutron Science (10)
- Nuclear Science and Technology (38)
- Nuclear Systems Modeling, Simulation and Validation (2)
- Supercomputing (40)
News Topics
- (-) Advanced Reactors (6)
- (-) Artificial Intelligence (14)
- (-) Nuclear Energy (7)
- 3-D Printing/Advanced Manufacturing (78)
- Big Data (9)
- Bioenergy (26)
- Biology (11)
- Biomedical (6)
- Biotechnology (4)
- Buildings (36)
- Chemical Sciences (14)
- Clean Water (8)
- Climate Change (21)
- Composites (17)
- Computer Science (37)
- Coronavirus (12)
- Critical Materials (9)
- Cybersecurity (9)
- Decarbonization (33)
- Energy Storage (73)
- Environment (54)
- Exascale Computing (3)
- Fossil Energy (2)
- Frontier (2)
- Fusion (1)
- Grid (41)
- High-Performance Computing (8)
- Hydropower (2)
- Isotopes (1)
- Machine Learning (11)
- Materials (35)
- Materials Science (27)
- Mathematics (2)
- Mercury (3)
- Microelectronics (1)
- Microscopy (8)
- Molten Salt (1)
- Nanotechnology (8)
- National Security (5)
- Net Zero (3)
- Neutron Science (11)
- Partnerships (12)
- Physics (1)
- Polymers (11)
- Quantum Science (5)
- Renewable Energy (1)
- Security (6)
- Simulation (4)
- Space Exploration (3)
- Statistics (1)
- Summit (5)
- Sustainable Energy (69)
- Transformational Challenge Reactor (3)
- Transportation (65)
Media Contacts

ORNL is home to the world's fastest exascale supercomputer, Frontier, which was built in part to facilitate energy-efficient and scalable AI-based algorithms and simulations.

Like most scientists, Chengping Chai is not content with the surface of things: He wants to probe beyond to learn what’s really going on. But in his case, he is literally building a map of the world beneath, using seismic and acoustic data that reveal when and where the earth moves.
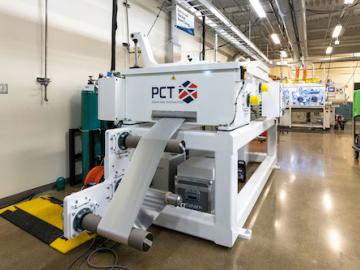
Researchers at the Department of Energy’s Oak Ridge National Laboratory and their technologies have received seven 2022 R&D 100 Awards, plus special recognition for a battery-related green technology product.
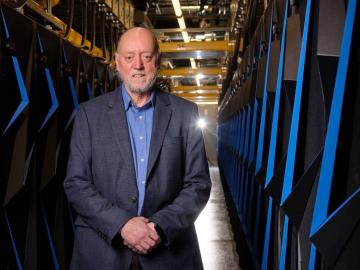
A force within the supercomputing community, Jack Dongarra developed software packages that became standard in the industry, allowing high-performance computers to become increasingly more powerful in recent decades.
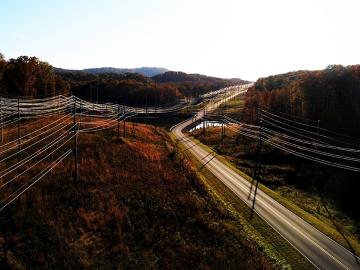
ORNL and the Tennessee Valley Authority, or TVA, are joining forces to advance decarbonization technologies from discovery through deployment through a new memorandum of understanding, or MOU.
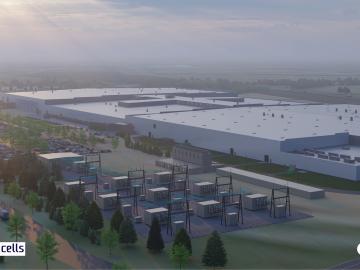
ORNL, TVA and TNECD were recognized by the Federal Laboratory Consortium for their impactful partnership that resulted in a record $2.3 billion investment by Ultium Cells, a General Motors and LG Energy Solution joint venture, to build a battery cell manufacturing plant in Spring Hill, Tennessee.
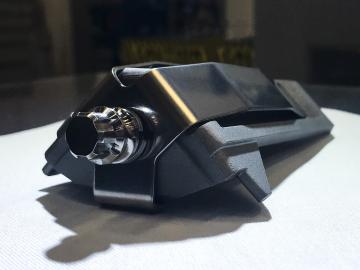
Four first-of-a-kind 3D-printed fuel assembly brackets, produced at the Department of Energy’s Manufacturing Demonstration Facility at Oak Ridge National Laboratory, have been installed and are now under routine operating
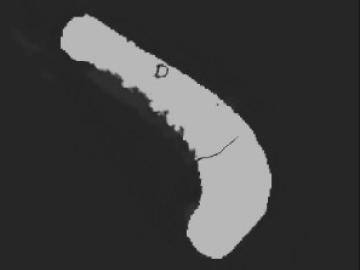
Algorithms developed at Oak Ridge National Laboratory can greatly enhance X-ray computed tomography images of 3D-printed metal parts, resulting in more accurate, faster scans.
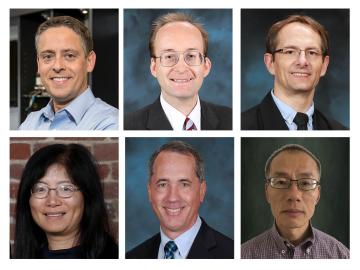
Six scientists at the Department of Energy’s Oak Ridge National Laboratory were named Battelle Distinguished Inventors, in recognition of obtaining 14 or more patents during their careers at the lab.
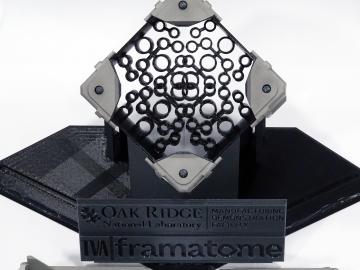
The Transformational Challenge Reactor, or TCR, a microreactor built using 3D printing and other new advanced technologies, could be operational by 2024.