Filter News
Area of Research
- (-) Advanced Manufacturing (22)
- (-) Computer Science (5)
- (-) Materials for Computing (11)
- Biology and Environment (18)
- Building Technologies (1)
- Clean Energy (122)
- Electricity and Smart Grid (3)
- Energy Frontier Research Centers (1)
- Functional Materials for Energy (1)
- Fusion and Fission (6)
- Fusion Energy (1)
- Materials (70)
- National Security (10)
- Neutron Science (19)
- Nuclear Science and Technology (4)
- Quantum information Science (9)
- Sensors and Controls (1)
- Supercomputing (40)
News Topics
- (-) 3-D Printing/Advanced Manufacturing (26)
- (-) Grid (2)
- (-) Nanotechnology (7)
- (-) Quantum Science (6)
- Advanced Reactors (1)
- Artificial Intelligence (7)
- Big Data (4)
- Bioenergy (2)
- Biology (1)
- Biomedical (2)
- Buildings (1)
- Chemical Sciences (4)
- Climate Change (1)
- Composites (4)
- Computer Science (23)
- Coronavirus (3)
- Cybersecurity (2)
- Decarbonization (1)
- Energy Storage (6)
- Environment (2)
- Exascale Computing (1)
- Fusion (1)
- High-Performance Computing (2)
- Isotopes (1)
- Machine Learning (5)
- Materials (16)
- Materials Science (21)
- Microscopy (4)
- National Security (1)
- Neutron Science (7)
- Nuclear Energy (2)
- Polymers (6)
- Quantum Computing (1)
- Security (1)
- Simulation (1)
- Space Exploration (2)
- Summit (2)
- Sustainable Energy (12)
- Transformational Challenge Reactor (1)
- Transportation (5)
Media Contacts

Scientists at ORNL have developed 3D-printed collimator techniques that can be used to custom design collimators that better filter out noise during different types of neutron scattering experiments
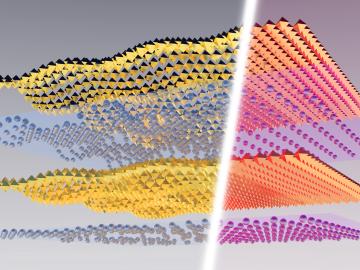
A study by researchers at the ORNL takes a fresh look at what could become the first step toward a new generation of solar batteries.
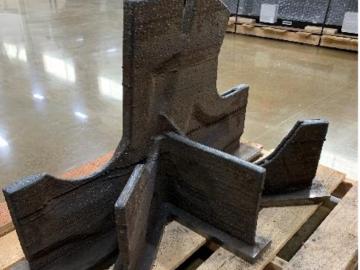
Oak Ridge National Laboratory researchers recently used large-scale additive manufacturing with metal to produce a full-strength steel component for a wind turbine, proving the technique as a viable alternative to
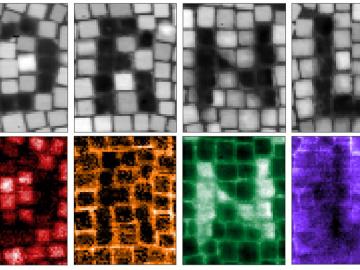
Drilling with the beam of an electron microscope, scientists at ORNL precisely machined tiny electrically conductive cubes that can interact with light and organized them in patterned structures that confine and relay light’s electromagnetic signal.
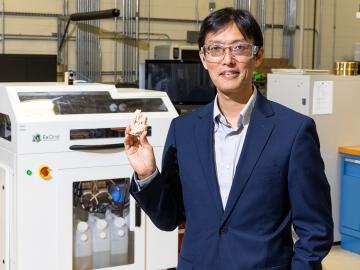
Researchers at ORNL designed a novel polymer to bind and strengthen silica sand for binder jet additive manufacturing, a 3D-printing method used by industries for prototyping and part production.

A team led by the U.S. Department of Energy’s Oak Ridge National Laboratory demonstrated the viability of a “quantum entanglement witness” capable of proving the presence of entanglement between magnetic particles, or spins, in a quantum material.

Oak Ridge National Laboratory, University of Tennessee and University of Central Florida researchers released a new high-performance computing code designed to more efficiently examine power systems and identify electrical grid disruptions, such as
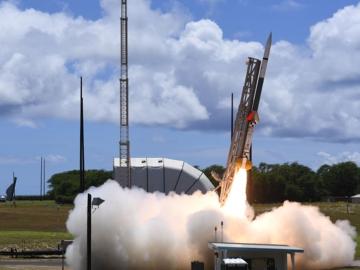
Oak Ridge National Laboratory researchers have developed a novel process to manufacture extreme heat resistant carbon-carbon composites. The performance of these materials will be tested in a U.S. Navy rocket that NASA will launch this fall.
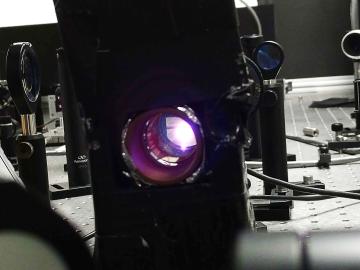
To minimize potential damage from underground oil and gas leaks, Oak Ridge National Laboratory is co-developing a quantum sensing system to detect pipeline leaks more quickly.

A research team at Oak Ridge National Laboratory have 3D printed a thermal protection shield, or TPS, for a capsule that will launch with the Cygnus cargo spacecraft as part of the supply mission to the International Space Station.