
Filter News
Area of Research
- (-) Clean Energy (69)
- (-) Computational Engineering (1)
- (-) National Security (19)
- Advanced Manufacturing (4)
- Biology and Environment (28)
- Building Technologies (3)
- Computational Biology (1)
- Computer Science (8)
- Electricity and Smart Grid (1)
- Functional Materials for Energy (1)
- Fusion and Fission (2)
- Materials (34)
- Materials for Computing (6)
- Neutron Science (9)
- Renewable Energy (1)
- Supercomputing (42)
News Topics
- (-) Artificial Intelligence (20)
- (-) Buildings (36)
- (-) Composites (17)
- (-) Hydropower (2)
- (-) Machine Learning (19)
- (-) Polymers (11)
- 3-D Printing/Advanced Manufacturing (80)
- Advanced Reactors (7)
- Big Data (12)
- Bioenergy (28)
- Biology (14)
- Biomedical (8)
- Biotechnology (5)
- Chemical Sciences (14)
- Clean Water (8)
- Climate Change (25)
- Computer Science (43)
- Coronavirus (14)
- Critical Materials (9)
- Cybersecurity (25)
- Decarbonization (34)
- Energy Storage (72)
- Environment (59)
- Exascale Computing (2)
- Fossil Energy (2)
- Frontier (2)
- Fusion (2)
- Grid (44)
- High-Performance Computing (11)
- Isotopes (1)
- Materials (36)
- Materials Science (29)
- Mathematics (2)
- Mercury (3)
- Microelectronics (1)
- Microscopy (8)
- Molten Salt (1)
- Nanotechnology (9)
- National Security (36)
- Net Zero (3)
- Neutron Science (15)
- Nuclear Energy (11)
- Partnerships (15)
- Physics (2)
- Quantum Science (3)
- Renewable Energy (1)
- Security (15)
- Simulation (4)
- Space Exploration (3)
- Statistics (1)
- Summit (7)
- Sustainable Energy (69)
- Transformational Challenge Reactor (3)
- Transportation (67)
Media Contacts

ORNL and The University of Toledo have entered into a memorandum of understanding for collaborative research.
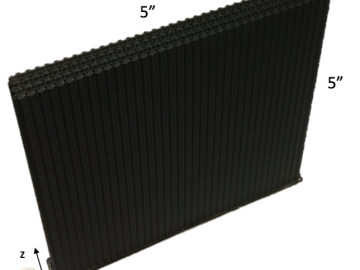
A team including Oak Ridge National Laboratory and University of Tennessee researchers demonstrated a novel 3D printing approach called Z-pinning that can increase the material’s strength and toughness by more than three and a half times compared to conventional additive manufacturing processes.
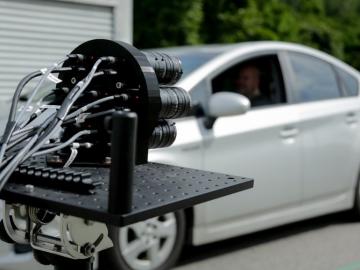
IDEMIA Identity & Security USA has licensed an advanced optical array developed at Oak Ridge National Laboratory. The portable technology can be used to help identify individuals in challenging outdoor conditions.

A team of researchers at Oak Ridge National Laboratory have demonstrated that designed synthetic polymers can serve as a high-performance binding material for next-generation lithium-ion batteries.
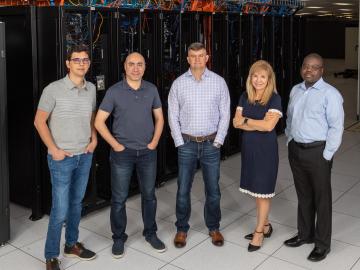
A study led by Oak Ridge National Laboratory explored the interface between the Department of Veterans Affairs’ healthcare data system and the data itself to detect the likelihood of errors and designed an auto-surveillance tool
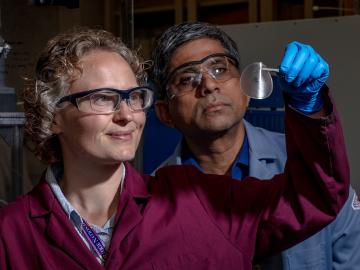
Oak Ridge National Laboratory scientists have developed a crucial component for a new kind of low-cost stationary battery system utilizing common materials and designed for grid-scale electricity storage. Large, economical electricity storage systems can benefit the nation’s grid ...
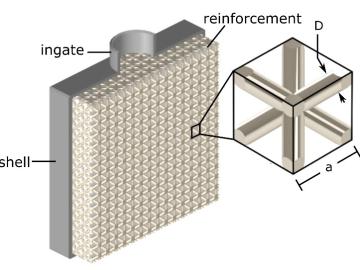
A new manufacturing method created by Oak Ridge National Laboratory and Rice University combines 3D printing with traditional casting to produce damage-tolerant components composed of multiple materials. Composite components made by pouring an aluminum alloy over a printed steel lattice showed an order of magnitude greater damage tolerance than aluminum alone.