
Filter News
Area of Research
- (-) Advanced Manufacturing (22)
- (-) Building Technologies (1)
- (-) Neutron Science (19)
- (-) Sensors and Controls (1)
- (-) Supercomputing (34)
- Biology and Environment (23)
- Clean Energy (153)
- Computational Engineering (1)
- Computer Science (5)
- Electricity and Smart Grid (1)
- Fuel Cycle Science and Technology (1)
- Functional Materials for Energy (1)
- Fusion and Fission (29)
- Fusion Energy (10)
- Isotope Development and Production (1)
- Isotopes (26)
- Materials (66)
- Materials for Computing (11)
- National Security (40)
- Nuclear Science and Technology (38)
- Nuclear Systems Modeling, Simulation and Validation (1)
- Quantum information Science (2)
- Transportation Systems (2)
News Topics
- (-) 3-D Printing/Advanced Manufacturing (28)
- (-) Cybersecurity (9)
- (-) Isotopes (1)
- (-) Machine Learning (17)
- (-) Nuclear Energy (8)
- (-) Security (7)
- (-) Transportation (10)
- Advanced Reactors (3)
- Artificial Intelligence (40)
- Big Data (20)
- Bioenergy (13)
- Biology (14)
- Biomedical (25)
- Biotechnology (2)
- Buildings (7)
- Chemical Sciences (6)
- Clean Water (2)
- Climate Change (17)
- Composites (4)
- Computer Science (99)
- Coronavirus (17)
- Critical Materials (3)
- Decarbonization (7)
- Energy Storage (14)
- Environment (28)
- Exascale Computing (22)
- Fossil Energy (1)
- Frontier (29)
- Fusion (3)
- Grid (6)
- High-Performance Computing (39)
- Materials (32)
- Materials Science (37)
- Mathematics (1)
- Microscopy (8)
- Molten Salt (1)
- Nanotechnology (19)
- National Security (8)
- Net Zero (1)
- Neutron Science (101)
- Partnerships (1)
- Physics (16)
- Polymers (3)
- Quantum Computing (19)
- Quantum Science (29)
- Simulation (14)
- Software (1)
- Space Exploration (6)
- Summit (42)
- Sustainable Energy (17)
- Transformational Challenge Reactor (1)
Media Contacts
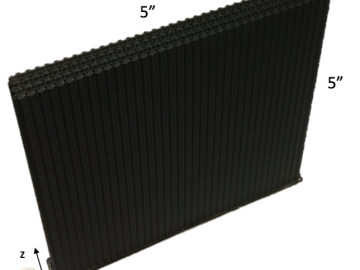
A team including Oak Ridge National Laboratory and University of Tennessee researchers demonstrated a novel 3D printing approach called Z-pinning that can increase the material’s strength and toughness by more than three and a half times compared to conventional additive manufacturing processes.
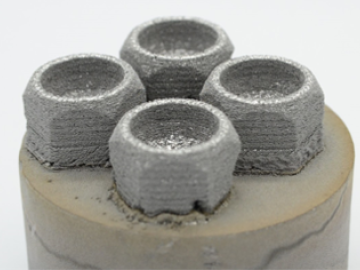
Using additive manufacturing, scientists experimenting with tungsten at Oak Ridge National Laboratory hope to unlock new potential of the high-performance heat-transferring material used to protect components from the plasma inside a fusion reactor. Fusion requires hydrogen isotopes to reach millions of degrees.
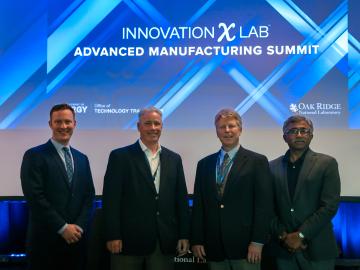
OAK RIDGE, Tenn., May 8, 2019—Oak Ridge National Laboratory and Lincoln Electric (NASDAQ: LECO) announced their continued collaboration on large-scale, robotic additive manufacturing technology at the Department of Energy’s Advanced Manufacturing InnovationXLab Summit.
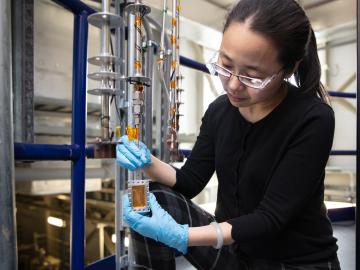
Researchers at the Department of Energy’s Oak Ridge National Laboratory, Pacific Northwest National Laboratory and Washington State University teamed up to investigate the complex dynamics of low-water liquids that challenge nuclear waste processing at federal cleanup sites.
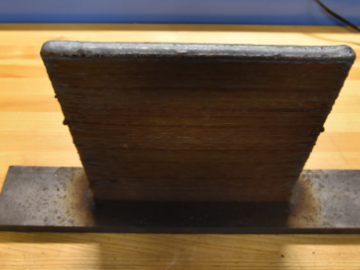
A novel additive manufacturing method developed by researchers at Oak Ridge National Laboratory could be a promising alternative for low-cost, high-quality production of large-scale metal parts with less material waste.

In a step toward advancing small modular nuclear reactor designs, scientists at Oak Ridge National Laboratory have run reactor simulations on ORNL supercomputer Summit with greater-than-expected computational efficiency.
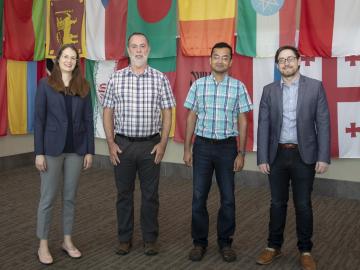
Scientists at the Department of Energy’s Oak Ridge National Laboratory are working to understand both the complex nature of uranium and the various oxide forms it can take during processing steps that might occur throughout the nuclear fuel cycle.
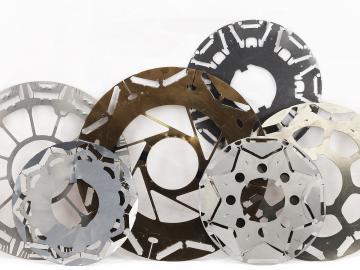
Oak Ridge National Laboratory scientists have created open source software that scales up analysis of motor designs to run on the fastest computers available, including those accessible to outside users at the Oak Ridge Leadership Computing Facility.
OAK RIDGE, Tenn., Feb. 12, 2019—A team of researchers from the Department of Energy’s Oak Ridge and Los Alamos National Laboratories has partnered with EPB, a Chattanooga utility and telecommunications company, to demonstrate the effectiveness of metro-scale quantum key distribution (QKD).
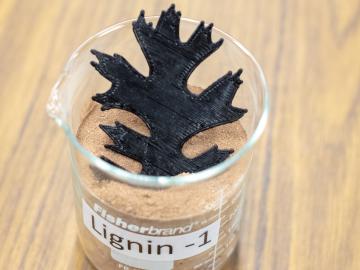
Scientists at the Department of Energy’s Oak Ridge National Laboratory have created a recipe for a renewable 3D printing feedstock that could spur a profitable new use for an intractable biorefinery byproduct: lignin.