Filter News
Area of Research
- (-) Clean Energy (125)
- (-) Supercomputing (69)
- Advanced Manufacturing (22)
- Biology and Environment (19)
- Building Technologies (1)
- Computational Biology (1)
- Computer Science (5)
- Electricity and Smart Grid (3)
- Functional Materials for Energy (1)
- Fusion and Fission (10)
- Fusion Energy (8)
- Materials (71)
- Materials for Computing (11)
- National Security (15)
- Neutron Science (102)
- Nuclear Science and Technology (17)
- Nuclear Systems Modeling, Simulation and Validation (1)
- Quantum information Science (9)
- Sensors and Controls (1)
News Topics
- (-) 3-D Printing/Advanced Manufacturing (80)
- (-) Advanced Reactors (7)
- (-) Frontier (28)
- (-) Grid (42)
- (-) Neutron Science (20)
- (-) Quantum Science (25)
- Artificial Intelligence (41)
- Big Data (24)
- Bioenergy (29)
- Biology (19)
- Biomedical (22)
- Biotechnology (6)
- Buildings (37)
- Chemical Sciences (16)
- Clean Water (8)
- Climate Change (35)
- Composites (17)
- Computer Science (107)
- Coronavirus (25)
- Critical Materials (12)
- Cybersecurity (14)
- Decarbonization (35)
- Energy Storage (75)
- Environment (68)
- Exascale Computing (23)
- Fossil Energy (2)
- Fusion (2)
- High-Performance Computing (39)
- Hydropower (2)
- Isotopes (1)
- Machine Learning (19)
- Materials (45)
- Materials Science (40)
- Mathematics (3)
- Mercury (3)
- Microelectronics (1)
- Microscopy (14)
- Molten Salt (1)
- Nanotechnology (15)
- National Security (11)
- Net Zero (4)
- Nuclear Energy (11)
- Partnerships (12)
- Physics (7)
- Polymers (13)
- Quantum Computing (19)
- Renewable Energy (1)
- Security (9)
- Simulation (16)
- Software (1)
- Space Exploration (6)
- Statistics (1)
- Summit (43)
- Sustainable Energy (71)
- Transformational Challenge Reactor (3)
- Transportation (69)
Media Contacts
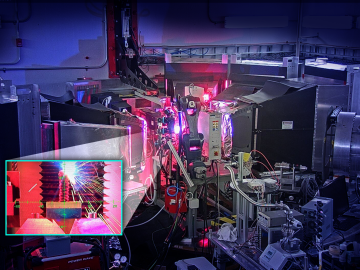
Using neutrons to see the additive manufacturing process at the atomic level, scientists have shown that they can measure strain in a material as it evolves and track how atoms move in response to stress.
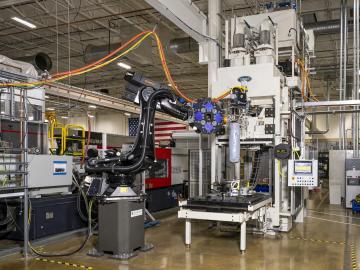
An Oak Ridge National Laboratory-developed advanced manufacturing technology, AMCM, was recently licensed by Orbital Composites and enables the rapid production of composite-based components, which could accelerate the decarbonization of vehicles
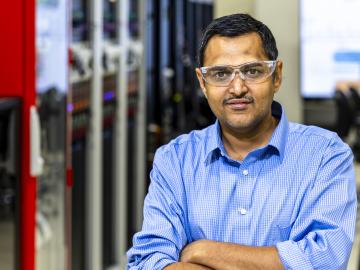
Sreenivasa Jaldanki, a researcher in the Grid Systems Modeling and Controls group at the Department of Energy’s Oak Ridge National Laboratory, was recently elevated to senior membership in the Institute of Electrical and Electronics Engineers, or IEEE.
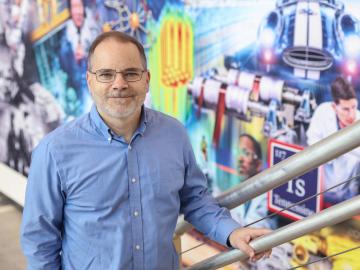
ORNL has been selected to lead an Energy Earthshot Research Center, or EERC, focused on developing chemical processes that use sustainable methods instead of burning fossil fuels to radically reduce industrial greenhouse gas emissions to stem climate change and limit the crisis of a rapidly warming planet.
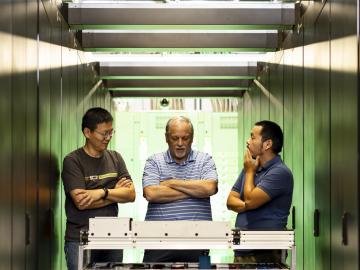
As Frontier, the world’s first exascale supercomputer, was being assembled at the Oak Ridge Leadership Computing Facility in 2021, understanding its performance on mixed-precision calculations remained a difficult prospect.

Oak Ridge National Laboratory researchers have conducted a comprehensive life cycle, cost and carbon emissions analysis on 3D-printed molds for precast concrete and determined the method is economically beneficial compared to conventional wood molds.

Outside the high-performance computing, or HPC, community, exascale may seem more like fodder for science fiction than a powerful tool for scientific research. Yet, when seen through the lens of real-world applications, exascale computing goes from ethereal concept to tangible reality with exceptional benefits.
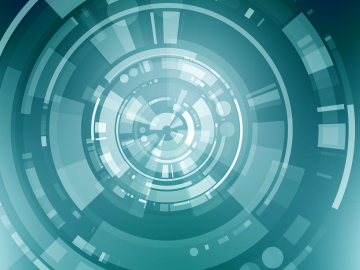
A new nanoscience study led by a researcher at ORNL takes a big-picture look at how scientists study materials at the smallest scales.

A licensing agreement between the Department of Energy’s Oak Ridge National Laboratory and research partner ZEISS will enable industrial X-ray computed tomography, or CT, to perform rapid evaluations of 3D-printed components using ORNL’s machine
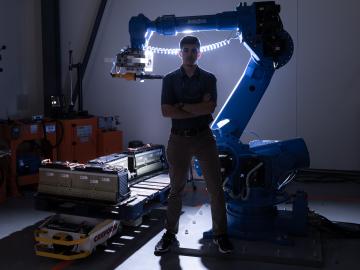
After being stabilized in an ambulance as he struggled to breathe, Jonathan Harter hit a low point. It was 2020, he was very sick with COVID-19, and his job as a lab technician at ORNL was ending along with his research funding.