Filter News
Area of Research
- (-) Advanced Manufacturing (11)
- (-) Fusion Energy (3)
- (-) Materials (13)
- Biology and Environment (8)
- Building Technologies (2)
- Clean Energy (45)
- Climate and Environmental Systems (1)
- Computational Engineering (2)
- Computer Science (10)
- Electricity and Smart Grid (1)
- Isotopes (1)
- Materials for Computing (4)
- Mathematics (1)
- National Security (3)
- Neutron Science (23)
- Nuclear Science and Technology (4)
- Quantum information Science (3)
- Sensors and Controls (1)
- Supercomputing (17)
News Topics
- (-) 3-D Printing/Advanced Manufacturing (15)
- (-) Computer Science (3)
- (-) Neutron Science (4)
- (-) Quantum Science (1)
- (-) Space Exploration (2)
- Advanced Reactors (6)
- Bioenergy (1)
- Biomedical (2)
- Buildings (1)
- Chemical Sciences (4)
- Clean Water (1)
- Composites (7)
- Coronavirus (1)
- Critical Materials (5)
- Decarbonization (1)
- Energy Storage (7)
- Environment (1)
- Frontier (1)
- Fusion (6)
- Isotopes (2)
- Materials (16)
- Materials Science (21)
- Microscopy (6)
- Molten Salt (1)
- Nanotechnology (8)
- Nuclear Energy (6)
- Physics (2)
- Polymers (6)
- Quantum Computing (1)
- Summit (1)
- Sustainable Energy (7)
- Transportation (6)
Media Contacts

A team of Oak Ridge National Laboratory researchers demonstrated that an additively manufactured hot stamping die – a tool used to create car body components – cooled faster than those produced by conventional manufacturing methods.

Oak Ridge National Laboratory researchers have demonstrated that a new class of superalloys made of cobalt and nickel remains crack-free and defect-resistant in extreme heat, making them conducive for use in metal-based 3D printing applications.
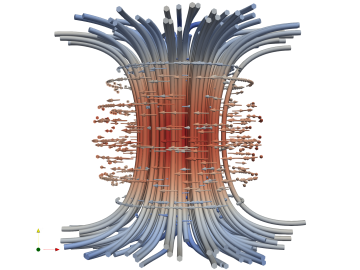
Combining expertise in physics, applied math and computing, Oak Ridge National Laboratory scientists are expanding the possibilities for simulating electromagnetic fields that underpin phenomena in materials design and telecommunications.
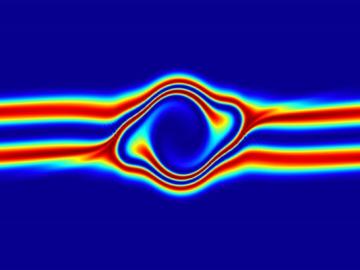
The prospect of simulating a fusion plasma is a step closer to reality thanks to a new computational tool developed by scientists in fusion physics, computer science and mathematics at ORNL.
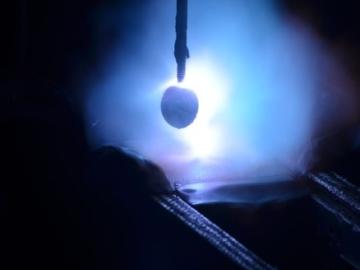
Researchers at Oak Ridge National Laboratory demonstrated that an additively manufactured polymer layer, when applied to carbon fiber reinforced plastic, or CFRP, can serve as an effective protector against aircraft lightning strikes.
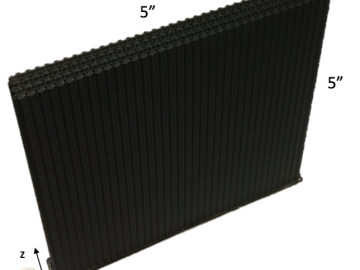
A team including Oak Ridge National Laboratory and University of Tennessee researchers demonstrated a novel 3D printing approach called Z-pinning that can increase the material’s strength and toughness by more than three and a half times compared to conventional additive manufacturing processes.
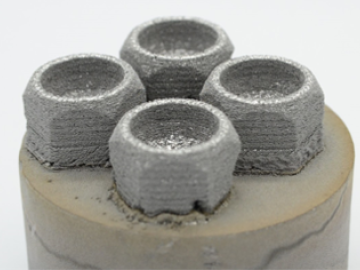
Using additive manufacturing, scientists experimenting with tungsten at Oak Ridge National Laboratory hope to unlock new potential of the high-performance heat-transferring material used to protect components from the plasma inside a fusion reactor. Fusion requires hydrogen isotopes to reach millions of degrees.

Researchers have pioneered a new technique using pressure to manipulate magnetism in thin film materials used to enhance performance in electronic devices.
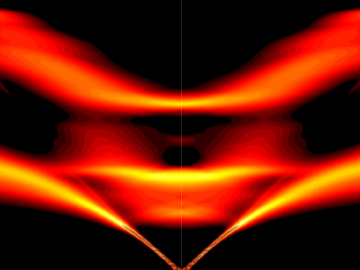
Scientists have discovered a way to alter heat transport in thermoelectric materials, a finding that may ultimately improve energy efficiency as the materials
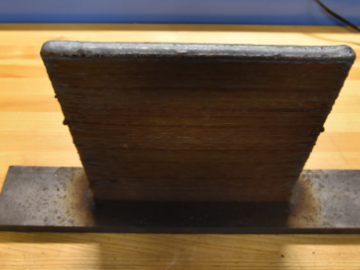
A novel additive manufacturing method developed by researchers at Oak Ridge National Laboratory could be a promising alternative for low-cost, high-quality production of large-scale metal parts with less material waste.