Filter News
Area of Research
- (-) Advanced Manufacturing (12)
- (-) National Security (4)
- (-) Nuclear Science and Technology (11)
- Biological Systems (1)
- Biology and Environment (17)
- Building Technologies (3)
- Clean Energy (58)
- Computational Biology (1)
- Computational Engineering (1)
- Computer Science (6)
- Electricity and Smart Grid (1)
- Energy Sciences (2)
- Fusion and Fission (1)
- Fusion Energy (6)
- Isotopes (4)
- Materials (20)
- Materials for Computing (4)
- Neutron Science (8)
- Nuclear Systems Modeling, Simulation and Validation (1)
- Quantum information Science (1)
- Sensors and Controls (1)
- Supercomputing (10)
News Topics
- (-) 3-D Printing/Advanced Manufacturing (11)
- (-) Big Data (2)
- (-) Biomedical (1)
- (-) Cybersecurity (1)
- (-) Energy Storage (1)
- (-) Grid (2)
- (-) Isotopes (1)
- (-) Nuclear Energy (11)
- (-) Space Exploration (3)
- (-) Sustainable Energy (4)
- Advanced Reactors (5)
- Composites (3)
- Computer Science (2)
- Coronavirus (1)
- Environment (1)
- Fusion (2)
- Materials (4)
- Materials Science (4)
- Molten Salt (3)
- Neutron Science (2)
- Security (1)
- Summit (1)
- Transportation (1)
Media Contacts
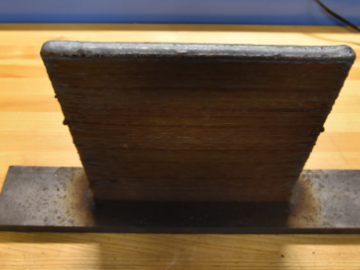
A novel additive manufacturing method developed by researchers at Oak Ridge National Laboratory could be a promising alternative for low-cost, high-quality production of large-scale metal parts with less material waste.
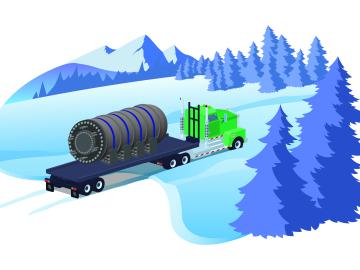
Oak Ridge National Laboratory scientists are evaluating paths for licensing remotely operated microreactors, which could provide clean energy sources to hard-to-reach communities, such as isolated areas in Alaska.
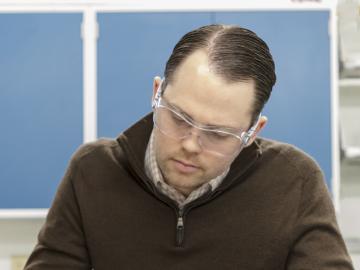
Oak Ridge National Laboratory is using ultrasonic additive manufacturing to embed highly accurate fiber optic sensors in heat- and radiation-resistant materials, allowing for real-time monitoring that could lead to greater insights and safer reactors.
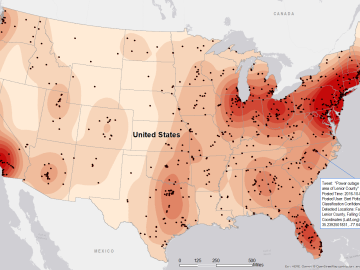
Gleaning valuable data from social platforms such as Twitter—particularly to map out critical location information during emergencies— has become more effective and efficient thanks to Oak Ridge National Laboratory.

By automating the production of neptunium oxide-aluminum pellets, Oak Ridge National Laboratory scientists have eliminated a key bottleneck when producing plutonium-238 used by NASA to fuel deep space exploration.
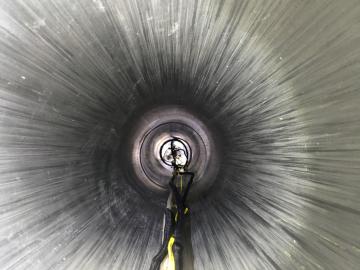
Scientists from Oak Ridge National Laboratory performed a corrosion test in a neutron radiation field to support the continued development of molten salt reactors.

The construction industry may soon benefit from 3D printed molds to make concrete facades, promising lower cost and production time. Researchers at Oak Ridge National Laboratory are evaluating the performance of 3D printed molds used to precast concrete facades in a 42-story buildin...