Filter News
Area of Research
- Advanced Manufacturing (11)
- Biological Systems (1)
- Biology and Environment (11)
- Building Technologies (1)
- Clean Energy (30)
- Computational Biology (1)
- Fusion Energy (2)
- Isotopes (3)
- Materials (11)
- Materials for Computing (2)
- National Security (1)
- Neutron Science (2)
- Nuclear Science and Technology (1)
- Quantum information Science (1)
- Supercomputing (6)
- Transportation Systems (1)
News Type
News Topics
- (-) 3-D Printing/Advanced Manufacturing (30)
- (-) Bioenergy (15)
- (-) Composites (9)
- (-) Decarbonization (8)
- (-) Frontier (1)
- (-) Isotopes (5)
- (-) Physics (4)
- (-) Summit (6)
- Advanced Reactors (13)
- Artificial Intelligence (13)
- Big Data (15)
- Biology (17)
- Biomedical (11)
- Biotechnology (3)
- Buildings (18)
- Chemical Sciences (7)
- Clean Water (13)
- Climate Change (21)
- Computer Science (39)
- Coronavirus (11)
- Critical Materials (12)
- Cybersecurity (3)
- Energy Storage (31)
- Environment (43)
- Exascale Computing (1)
- Fusion (9)
- Grid (20)
- High-Performance Computing (11)
- Hydropower (6)
- Irradiation (2)
- ITER (3)
- Machine Learning (10)
- Materials (35)
- Materials Science (33)
- Mathematics (1)
- Mercury (3)
- Microscopy (11)
- Molten Salt (5)
- Nanotechnology (12)
- National Security (3)
- Net Zero (1)
- Neutron Science (27)
- Nuclear Energy (18)
- Partnerships (1)
- Polymers (8)
- Quantum Computing (4)
- Quantum Science (10)
- Security (1)
- Simulation (6)
- Space Exploration (10)
- Statistics (1)
- Sustainable Energy (44)
- Transportation (35)
Media Contacts

In a step toward advancing small modular nuclear reactor designs, scientists at Oak Ridge National Laboratory have run reactor simulations on ORNL supercomputer Summit with greater-than-expected computational efficiency.
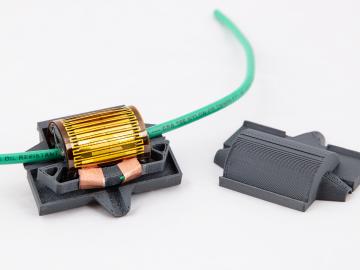
Scientists at Oak Ridge National Laboratory have developed a low-cost, printed, flexible sensor that can wrap around power cables to precisely monitor electrical loads from household appliances to support grid operations.

Physicists turned to the “doubly magic” tin isotope Sn-132, colliding it with a target at Oak Ridge National Laboratory to assess its properties as it lost a neutron to become Sn-131.

The construction industry may soon benefit from 3D printed molds to make concrete facades, promising lower cost and production time. Researchers at Oak Ridge National Laboratory are evaluating the performance of 3D printed molds used to precast concrete facades in a 42-story buildin...
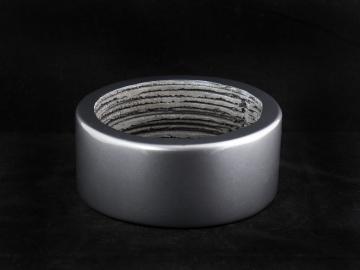
Oak Ridge National Laboratory scientists have improved a mixture of materials used to 3D print permanent magnets with increased density, which could yield longer lasting, better performing magnets for electric motors, sensors and vehicle applications. Building on previous research, ...
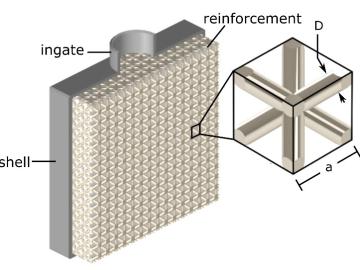
A new manufacturing method created by Oak Ridge National Laboratory and Rice University combines 3D printing with traditional casting to produce damage-tolerant components composed of multiple materials. Composite components made by pouring an aluminum alloy over a printed steel lattice showed an order of magnitude greater damage tolerance than aluminum alone.