Filter News
Area of Research
- (-) Fusion and Fission (2)
- (-) Materials (4)
- Advanced Manufacturing (1)
- Biology and Environment (6)
- Clean Energy (21)
- Computational Engineering (2)
- Computer Science (5)
- Electricity and Smart Grid (1)
- Fusion Energy (8)
- Mathematics (1)
- National Security (2)
- Nuclear Science and Technology (6)
- Nuclear Systems Modeling, Simulation and Validation (1)
- Quantum information Science (1)
- Sensors and Controls (1)
- Supercomputing (3)
News Topics
- (-) Advanced Reactors (2)
- (-) Clean Water (1)
- (-) Fusion (4)
- (-) Molten Salt (1)
- 3-D Printing/Advanced Manufacturing (6)
- Bioenergy (1)
- Biomedical (2)
- Buildings (1)
- Chemical Sciences (4)
- Composites (4)
- Computer Science (1)
- Coronavirus (1)
- Critical Materials (5)
- Decarbonization (1)
- Energy Storage (7)
- Environment (1)
- Isotopes (2)
- ITER (2)
- Materials (12)
- Materials Science (19)
- Microscopy (6)
- Nanotechnology (8)
- Neutron Science (4)
- Nuclear Energy (3)
- Physics (2)
- Polymers (6)
- Quantum Computing (1)
- Quantum Science (1)
- Space Exploration (1)
- Sustainable Energy (3)
- Transportation (6)
Media Contacts

Staff at Oak Ridge National Laboratory organized transport for a powerful component that is critical to the world’s largest experiment, the international ITER project.

Equipment and expertise from Oak Ridge National Laboratory will allow scientists studying fusion energy and technologies to acquire crucial data during landmark fusion experiments in Europe.
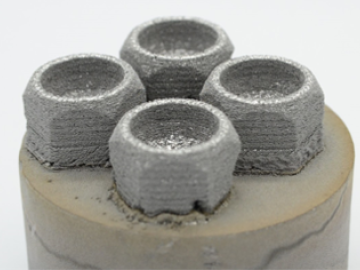
Using additive manufacturing, scientists experimenting with tungsten at Oak Ridge National Laboratory hope to unlock new potential of the high-performance heat-transferring material used to protect components from the plasma inside a fusion reactor. Fusion requires hydrogen isotopes to reach millions of degrees.
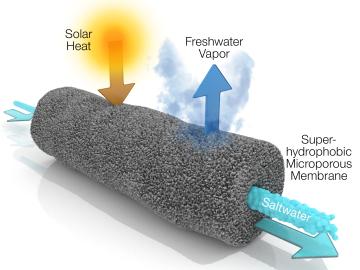
A new method developed at Oak Ridge National Laboratory improves the energy efficiency of a desalination process known as solar-thermal evaporation.

Scientists have tested a novel heat-shielding graphite foam, originally created at Oak Ridge National Laboratory, at Germany’s Wendelstein 7-X stellarator with promising results for use in plasma-facing components of fusion reactors.
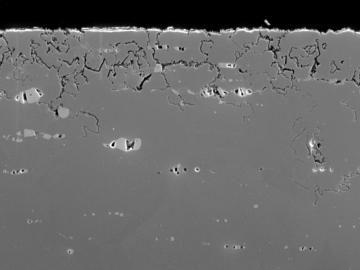
Oak Ridge National Laboratory scientists analyzed more than 50 years of data showing puzzlingly inconsistent trends about corrosion of structural alloys in molten salts and found one factor mattered most—salt purity.