Filter News
Area of Research
- (-) Clean Energy (29)
- Advanced Manufacturing (4)
- Biology and Environment (18)
- Climate and Environmental Systems (3)
- Computational Engineering (1)
- Computer Science (1)
- Isotopes (3)
- Materials (16)
- Materials for Computing (6)
- Mathematics (1)
- National Security (2)
- Neutron Science (5)
- Nuclear Science and Technology (1)
- Quantum information Science (1)
- Supercomputing (5)
News Topics
- (-) Clean Water (4)
- (-) Environment (15)
- (-) Materials (12)
- (-) Mercury (1)
- 3-D Printing/Advanced Manufacturing (23)
- Artificial Intelligence (1)
- Big Data (1)
- Bioenergy (2)
- Biology (2)
- Biomedical (1)
- Biotechnology (1)
- Buildings (13)
- Chemical Sciences (1)
- Climate Change (6)
- Composites (9)
- Computer Science (9)
- Coronavirus (2)
- Critical Materials (4)
- Decarbonization (4)
- Energy Storage (21)
- Grid (15)
- High-Performance Computing (1)
- Hydropower (2)
- Machine Learning (2)
- Materials Science (9)
- Mathematics (1)
- Microscopy (2)
- Nanotechnology (1)
- Net Zero (1)
- Nuclear Energy (1)
- Polymers (5)
- Simulation (1)
- Space Exploration (2)
- Statistics (1)
- Sustainable Energy (27)
- Transportation (26)
Media Contacts

A new report published by ORNL assessed how advanced manufacturing and materials, such as 3D printing and novel component coatings, could offer solutions to modernize the existing fleet and design new approaches to hydropower.

ORNL researchers have identified a mechanism in a 3D-printed alloy – termed “load shuffling” — that could enable the design of better-performing lightweight materials for vehicles.
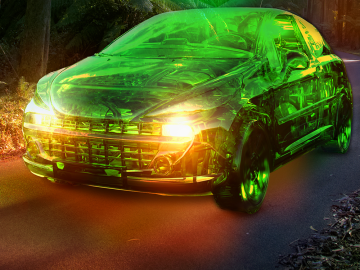
Oak Ridge National Laboratory scientists designed a recyclable polymer for carbon-fiber composites to enable circular manufacturing of parts that boost energy efficiency in automotive, wind power and aerospace applications.

Oak Ridge National Laboratory scientists worked with the Colorado School of Mines and Baylor University to develop and test control methods for autonomous water treatment plants that use less energy and generate less waste.
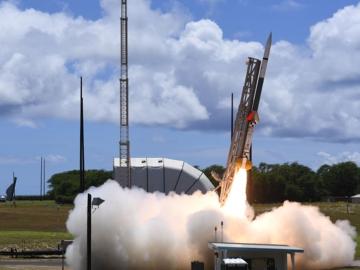
Oak Ridge National Laboratory researchers have developed a novel process to manufacture extreme heat resistant carbon-carbon composites. The performance of these materials will be tested in a U.S. Navy rocket that NASA will launch this fall.
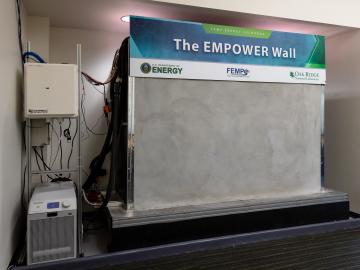
Oak Ridge National Laboratory researchers demonstrated that cooling cost savings could be achieved with a 3D printed concrete smart wall following a three-month field test.

A research team at Oak Ridge National Laboratory have 3D printed a thermal protection shield, or TPS, for a capsule that will launch with the Cygnus cargo spacecraft as part of the supply mission to the International Space Station.
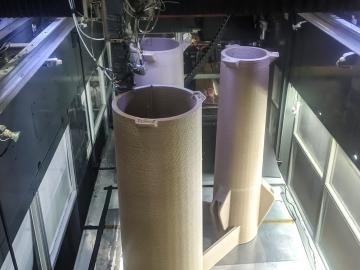
A team of researchers at Oak Ridge National Laboratory demonstrated the ability to additively manufacture power poles from bioderived and recycled materials, which could more quickly restore electricity after natural disasters.
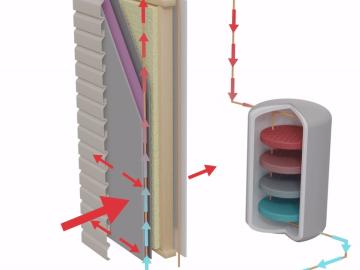
Researchers at Oak Ridge National Laboratory have developed a novel envelope system that diverts heat or coolness away from a building and stores it for future use.
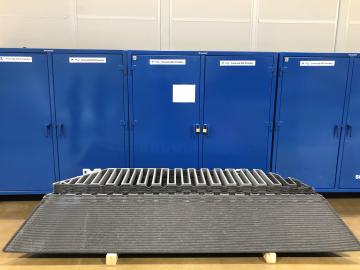
Oak Ridge National Laboratory researchers, in collaboration with Cincinnati Inc., demonstrated the potential for using multimaterials and recycled composites in large-scale applications by 3D printing a mold that replicated a single facet of a