Filter News
Area of Research
- (-) Advanced Manufacturing (13)
- (-) Materials for Computing (8)
- Biology and Environment (7)
- Building Technologies (1)
- Clean Energy (60)
- Computational Engineering (1)
- Computer Science (6)
- Electricity and Smart Grid (1)
- Fusion and Fission (5)
- Fusion Energy (6)
- Isotopes (1)
- Materials (22)
- National Security (9)
- Neutron Science (4)
- Nuclear Science and Technology (5)
- Quantum information Science (3)
- Sensors and Controls (1)
- Supercomputing (8)
News Type
News Topics
- (-) 3-D Printing/Advanced Manufacturing (14)
- (-) Fusion (1)
- (-) Materials (10)
- (-) Quantum Science (1)
- Advanced Reactors (1)
- Biomedical (1)
- Chemical Sciences (1)
- Composites (3)
- Computer Science (1)
- Coronavirus (2)
- Materials Science (10)
- Microscopy (2)
- Nanotechnology (3)
- Neutron Science (1)
- Nuclear Energy (1)
- Polymers (1)
- Space Exploration (1)
- Sustainable Energy (5)
- Transportation (1)
Media Contacts
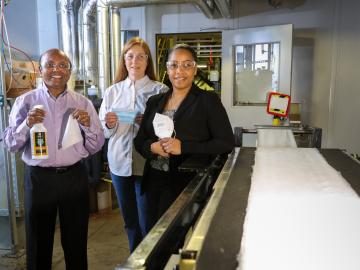
Oak Ridge National Laboratory researchers collaborated with Iowa State University and RJ Lee Group to demonstrate a safe and effective antiviral coating for N95 masks. The coating destroys the COVID-19-causing coronavirus and could enable reuse of masks made from various fabrics.
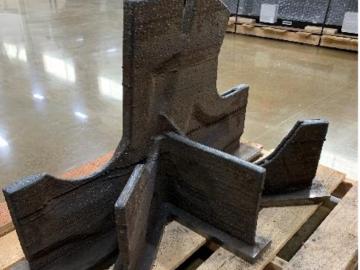
Oak Ridge National Laboratory researchers recently used large-scale additive manufacturing with metal to produce a full-strength steel component for a wind turbine, proving the technique as a viable alternative to
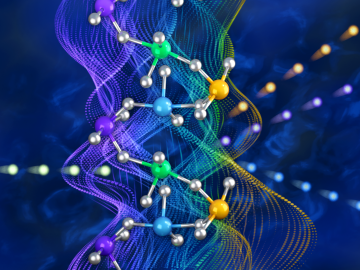
A discovery by Oak Ridge National Laboratory researchers may aid the design of materials that better manage heat.

Oak Ridge National Laboratory researchers determined that designing polymers specifically with upcycling in mind could reduce future plastic waste considerably and facilitate a circular economy where the material is used repeatedly.
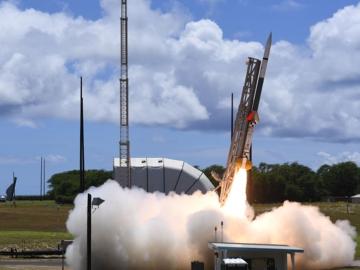
Oak Ridge National Laboratory researchers have developed a novel process to manufacture extreme heat resistant carbon-carbon composites. The performance of these materials will be tested in a U.S. Navy rocket that NASA will launch this fall.

A research team at Oak Ridge National Laboratory have 3D printed a thermal protection shield, or TPS, for a capsule that will launch with the Cygnus cargo spacecraft as part of the supply mission to the International Space Station.
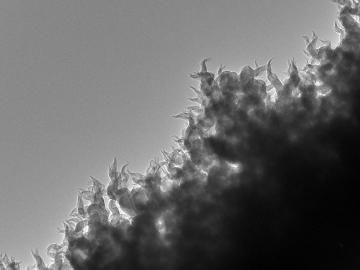
In a new twist to an existing award-winning ORNL technology, researchers have developed an electrocatalyst that enables water and carbon dioxide to be split and the atoms recombined to form higher weight hydrocarbons for gasoline, diesel and jet fuel.
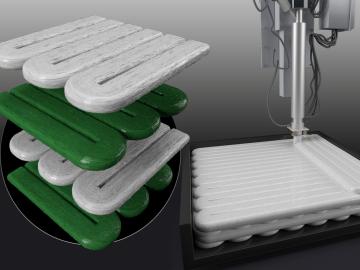
Oak Ridge National Laboratory researchers combined additive manufacturing with conventional compression molding to produce high-performance thermoplastic composites reinforced with short carbon fibers.
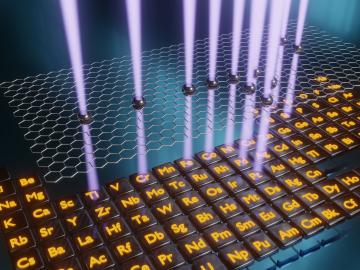
Oak Ridge National Laboratory scientists demonstrated that an electron microscope can be used to selectively remove carbon atoms from graphene’s atomically thin lattice and stitch transition-metal dopant atoms in their place.

A team of Oak Ridge National Laboratory researchers demonstrated that an additively manufactured hot stamping die – a tool used to create car body components – cooled faster than those produced by conventional manufacturing methods.