Filter News
Area of Research
- Advanced Manufacturing (12)
- Biology and Environment (8)
- Building Technologies (1)
- Clean Energy (35)
- Computational Biology (1)
- Computer Science (1)
- Fusion and Fission (1)
- Fusion Energy (2)
- Isotopes (3)
- Materials (9)
- Materials for Computing (3)
- National Security (3)
- Neutron Science (3)
- Nuclear Science and Technology (1)
- Quantum information Science (3)
- Supercomputing (11)
News Type
News Topics
- (-) 3-D Printing/Advanced Manufacturing (43)
- (-) Biomedical (19)
- (-) Quantum Science (12)
- (-) Summit (8)
- Advanced Reactors (15)
- Artificial Intelligence (17)
- Big Data (21)
- Bioenergy (32)
- Biology (38)
- Biotechnology (7)
- Buildings (27)
- Chemical Sciences (17)
- Clean Water (19)
- Climate Change (36)
- Composites (11)
- Computer Science (52)
- Coronavirus (17)
- Critical Materials (13)
- Cybersecurity (9)
- Decarbonization (23)
- Energy Storage (45)
- Environment (80)
- Exascale Computing (4)
- Frontier (4)
- Fusion (16)
- Grid (27)
- High-Performance Computing (20)
- Hydropower (8)
- Irradiation (2)
- Isotopes (14)
- ITER (4)
- Machine Learning (15)
- Materials (42)
- Materials Science (45)
- Mathematics (5)
- Mercury (7)
- Microscopy (20)
- Molten Salt (5)
- Nanotechnology (18)
- National Security (18)
- Net Zero (3)
- Neutron Science (35)
- Nuclear Energy (32)
- Partnerships (1)
- Physics (20)
- Polymers (14)
- Quantum Computing (5)
- Security (7)
- Simulation (10)
- Space Exploration (10)
- Statistics (1)
- Sustainable Energy (57)
- Transportation (47)
Media Contacts
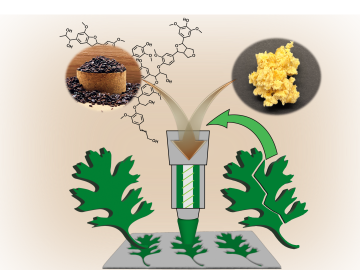
Oak Ridge National Laboratory scientists ingeniously created a sustainable, soft material by combining rubber with woody reinforcements and incorporating “smart” linkages between the components that unlock on demand.
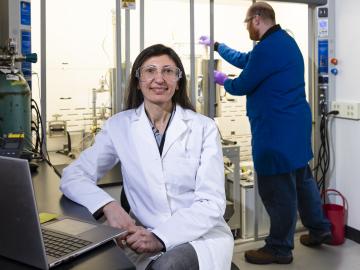
Canan Karakaya, a R&D Staff member in the Chemical Process Scale-Up group at ORNL, was inspired to become a chemical engineer after she experienced a magical transformation that turned ammonia gas into ammonium nitrate, turning a liquid into white flakes gently floating through the air.
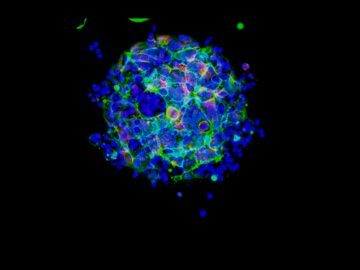
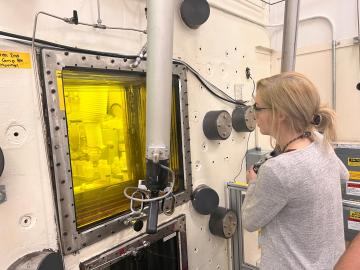
Raina Setzer knows the work she does matters. That’s because she’s already seen it from the other side. Setzer, a radiochemical processing technician in Oak Ridge National Laboratory’s Isotope Processing and Manufacturing Division, joined the lab in June 2023.
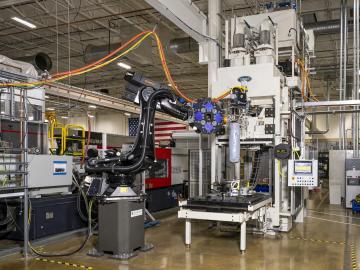
An Oak Ridge National Laboratory-developed advanced manufacturing technology, AMCM, was recently licensed by Orbital Composites and enables the rapid production of composite-based components, which could accelerate the decarbonization of vehicles

Oak Ridge National Laboratory researchers have conducted a comprehensive life cycle, cost and carbon emissions analysis on 3D-printed molds for precast concrete and determined the method is economically beneficial compared to conventional wood molds.
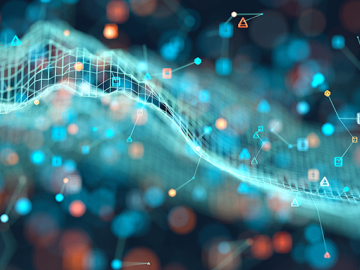
A study led by Oak Ridge National Laboratory researchers identifies a new potential application in quantum computing that could be part of the next computational revolution.

A new report published by ORNL assessed how advanced manufacturing and materials, such as 3D printing and novel component coatings, could offer solutions to modernize the existing fleet and design new approaches to hydropower.
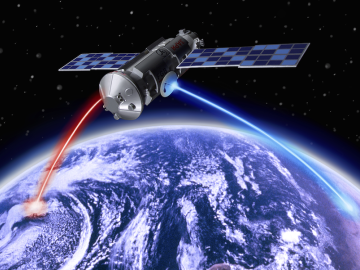
A study by Oak Ridge National Laboratory researchers has demonstrated how satellites could enable more efficient, secure quantum networks.

ORNL researchers have identified a mechanism in a 3D-printed alloy – termed “load shuffling” — that could enable the design of better-performing lightweight materials for vehicles.