Filter News
Area of Research
- (-) Clean Energy (86)
- (-) Materials (85)
- (-) Neutron Science (15)
- Advanced Manufacturing (4)
- Biology and Environment (15)
- Building Technologies (3)
- Computer Science (3)
- Energy Sciences (1)
- Fusion and Fission (6)
- Fusion Energy (1)
- Isotope Development and Production (1)
- Isotopes (11)
- Materials Characterization (2)
- Materials for Computing (15)
- Materials Under Extremes (1)
- National Security (3)
- Nuclear Science and Technology (6)
- Supercomputing (28)
News Type
News Topics
- (-) Buildings (21)
- (-) Chemical Sciences (25)
- (-) Energy Storage (60)
- (-) Frontier (3)
- (-) Isotopes (7)
- (-) Materials (70)
- (-) Space Exploration (5)
- 3-D Printing/Advanced Manufacturing (60)
- Advanced Reactors (4)
- Artificial Intelligence (8)
- Big Data (3)
- Bioenergy (20)
- Biology (12)
- Biomedical (12)
- Biotechnology (4)
- Clean Water (5)
- Climate Change (14)
- Composites (15)
- Computer Science (29)
- Coronavirus (12)
- Critical Materials (18)
- Cybersecurity (7)
- Decarbonization (15)
- Environment (34)
- Exascale Computing (2)
- Fossil Energy (1)
- Fusion (5)
- Grid (26)
- High-Performance Computing (6)
- Hydropower (2)
- ITER (1)
- Machine Learning (7)
- Materials Science (67)
- Mathematics (1)
- Mercury (2)
- Microscopy (18)
- Molten Salt (3)
- Nanotechnology (32)
- National Security (5)
- Net Zero (2)
- Neutron Science (65)
- Nuclear Energy (10)
- Partnerships (11)
- Physics (19)
- Polymers (16)
- Quantum Computing (2)
- Quantum Science (17)
- Renewable Energy (1)
- Security (4)
- Simulation (2)
- Statistics (1)
- Summit (5)
- Sustainable Energy (52)
- Transformational Challenge Reactor (3)
- Transportation (47)
Media Contacts

A collection of seven technologies for lithium recovery developed by scientists from ORNL has been licensed to Element3, a Texas-based company focused on extracting lithium from wastewater produced by oil and gas production.
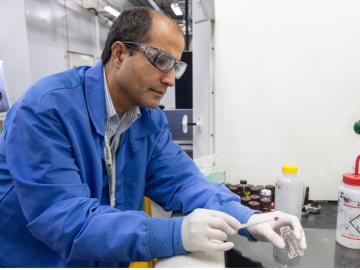
Electric vehicles can drive longer distances if their lithium-ion batteries deliver more energy in a lighter package. A prime weight-loss candidate is the current collector, a component that often adds 10% to the weight of a battery cell without contributing energy.

Four scientists affiliated with ORNL were named Battelle Distinguished Inventors during the lab’s annual Innovation Awards on Dec. 1 in recognition of being granted 14 or more United States patents.

Used lithium-ion batteries from cell phones, laptops and a growing number of electric vehicles are piling up, but options for recycling them remain limited mostly to burning or chemically dissolving shredded batteries.
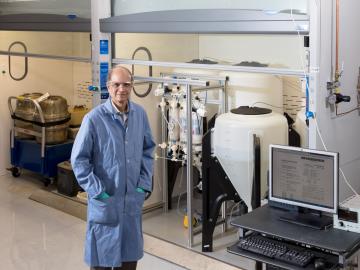
Caldera Holding, the owner and developer of Missouri’s Pea Ridge iron mine, has entered a nonexclusive research and development licensing agreement with ORNL to apply a membrane solvent extraction technique, or MSX, developed by ORNL researchers to mined ores.

Guided by machine learning, chemists at ORNL designed a record-setting carbonaceous supercapacitor material that stores four times more energy than the best commercial material.
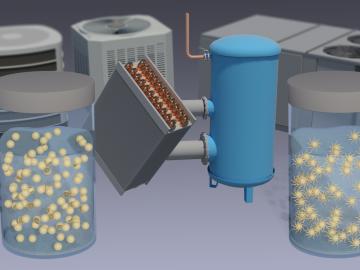
ORNL researchers demonstrated that an additive made from polymers and electrolytes improves the thermal performance and stability of salt hydrate phase change materials, or PCMs, a finding that could advance their integration into carbon-reducing heat pumps.
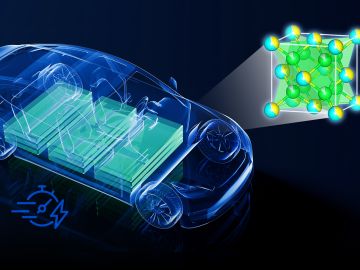
Currently, the biggest hurdle for electric vehicles, or EVs, is the development of advanced battery technology to extend driving range, safety and reliability.
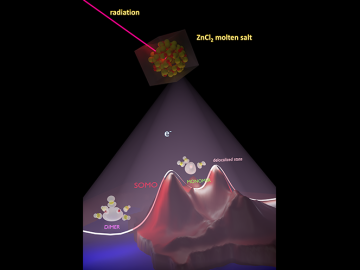
In a finding that helps elucidate how molten salts in advanced nuclear reactors might behave, scientists have shown how electrons interacting with the ions of the molten salt can form three states with different properties. Understanding these states can help predict the impact of radiation on the performance of salt-fueled reactors.
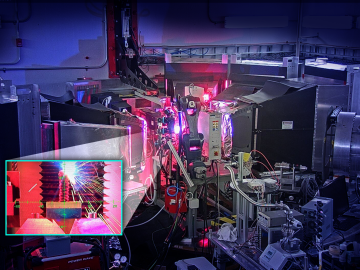
Using neutrons to see the additive manufacturing process at the atomic level, scientists have shown that they can measure strain in a material as it evolves and track how atoms move in response to stress.