Filter News
Area of Research
- (-) Advanced Manufacturing (3)
- (-) Neutron Science (6)
- Biology and Environment (10)
- Clean Energy (61)
- Computer Science (2)
- Energy Sciences (1)
- Fusion and Fission (2)
- Fusion Energy (1)
- Isotopes (10)
- Materials (39)
- Materials for Computing (4)
- National Security (3)
- Nuclear Science and Technology (3)
- Supercomputing (18)
News Topics
- (-) Composites (4)
- (-) Energy Storage (4)
- (-) Frontier (1)
- 3-D Printing/Advanced Manufacturing (21)
- Advanced Reactors (1)
- Artificial Intelligence (3)
- Big Data (1)
- Bioenergy (5)
- Biology (4)
- Biomedical (6)
- Biotechnology (1)
- Chemical Sciences (1)
- Climate Change (1)
- Computer Science (11)
- Coronavirus (5)
- Cybersecurity (4)
- Decarbonization (1)
- Environment (4)
- Fusion (2)
- Grid (1)
- High-Performance Computing (1)
- Machine Learning (1)
- Materials (13)
- Materials Science (20)
- Microscopy (2)
- Nanotechnology (7)
- National Security (1)
- Neutron Science (63)
- Nuclear Energy (4)
- Physics (9)
- Quantum Science (9)
- Security (1)
- Space Exploration (3)
- Summit (4)
- Sustainable Energy (7)
- Transformational Challenge Reactor (1)
- Transportation (3)
Media Contacts
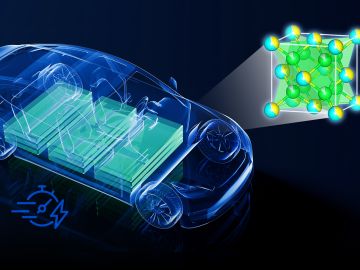
Currently, the biggest hurdle for electric vehicles, or EVs, is the development of advanced battery technology to extend driving range, safety and reliability.
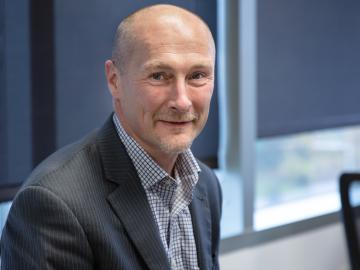
Paul Langan will join ORNL in the spring as associate laboratory director for the Biological and Environmental Systems Science Directorate.
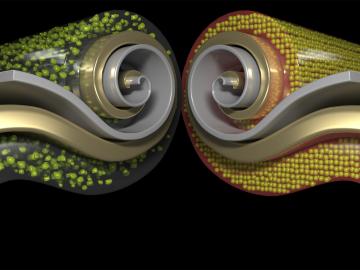
Researchers at ORNL have developed a new method for producing a key component of lithium-ion batteries. The result is a more affordable battery from a faster, less wasteful process that uses less toxic material.

Researchers at ORNL and the University of Tennessee, Knoxville, discovered a key material needed for fast-charging lithium-ion batteries. The commercially relevant approach opens a potential pathway to improve charging speeds for electric vehicles.

A research team at Oak Ridge National Laboratory have 3D printed a thermal protection shield, or TPS, for a capsule that will launch with the Cygnus cargo spacecraft as part of the supply mission to the International Space Station.
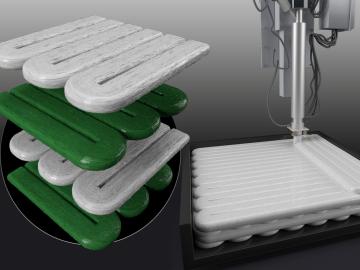
Oak Ridge National Laboratory researchers combined additive manufacturing with conventional compression molding to produce high-performance thermoplastic composites reinforced with short carbon fibers.
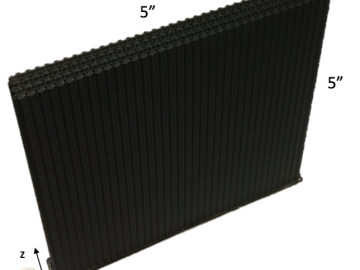
A team including Oak Ridge National Laboratory and University of Tennessee researchers demonstrated a novel 3D printing approach called Z-pinning that can increase the material’s strength and toughness by more than three and a half times compared to conventional additive manufacturing processes.
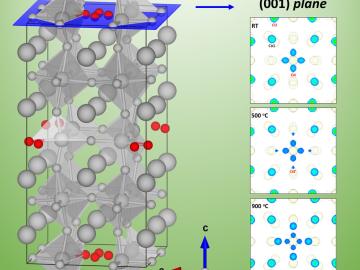
A University of South Carolina research team is investigating the oxygen reduction performance of energy conversion materials called perovskites by using neutron diffraction at Oak Ridge National Laboratory’s Spallation Neutron Source.
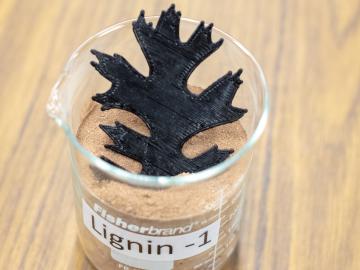
Scientists at the Department of Energy’s Oak Ridge National Laboratory have created a recipe for a renewable 3D printing feedstock that could spur a profitable new use for an intractable biorefinery byproduct: lignin.