Filter News
Area of Research
- (-) Advanced Manufacturing (4)
- (-) Materials for Computing (6)
- Biological Systems (1)
- Biology and Environment (27)
- Clean Energy (71)
- Fusion and Fission (1)
- Fusion Energy (1)
- Materials (40)
- National Security (6)
- Neutron Science (21)
- Nuclear Science and Technology (2)
- Quantum information Science (1)
- Supercomputing (31)
- Transportation Systems (2)
News Topics
- (-) Bioenergy (1)
- (-) Composites (4)
- (-) Coronavirus (2)
- (-) Transportation (3)
- 3-D Printing/Advanced Manufacturing (22)
- Advanced Reactors (1)
- Artificial Intelligence (1)
- Biomedical (2)
- Chemical Sciences (3)
- Computer Science (4)
- Cybersecurity (1)
- Energy Storage (2)
- Environment (1)
- Fusion (1)
- Isotopes (1)
- Machine Learning (1)
- Materials (12)
- Materials Science (15)
- Microscopy (3)
- Nanotechnology (4)
- National Security (1)
- Neutron Science (3)
- Nuclear Energy (2)
- Polymers (5)
- Quantum Science (2)
- Security (1)
- Space Exploration (2)
- Summit (1)
- Sustainable Energy (9)
- Transformational Challenge Reactor (1)
Media Contacts
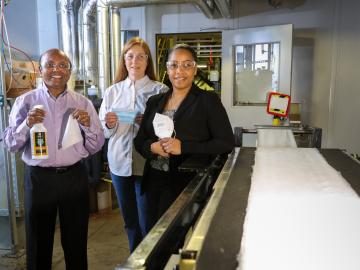
Oak Ridge National Laboratory researchers collaborated with Iowa State University and RJ Lee Group to demonstrate a safe and effective antiviral coating for N95 masks. The coating destroys the COVID-19-causing coronavirus and could enable reuse of masks made from various fabrics.
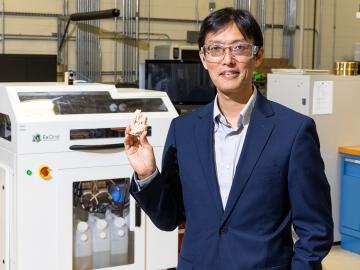
Researchers at ORNL designed a novel polymer to bind and strengthen silica sand for binder jet additive manufacturing, a 3D-printing method used by industries for prototyping and part production.

A research team at Oak Ridge National Laboratory have 3D printed a thermal protection shield, or TPS, for a capsule that will launch with the Cygnus cargo spacecraft as part of the supply mission to the International Space Station.
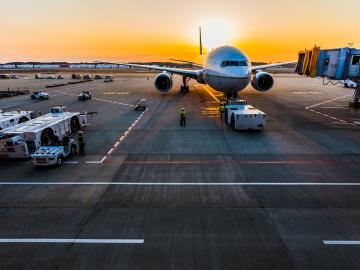
Oak Ridge National Laboratory researchers have developed a new catalyst for converting ethanol into C3+ olefins – the chemical
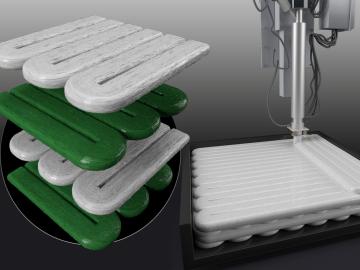
Oak Ridge National Laboratory researchers combined additive manufacturing with conventional compression molding to produce high-performance thermoplastic composites reinforced with short carbon fibers.
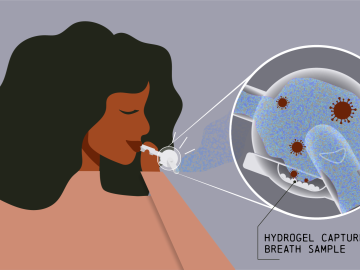
Collaborators at Oak Ridge National Laboratory and the University of Tennessee Health Science Center are developing a breath-sampling whistle that could make COVID-19 screening easy to do at home.
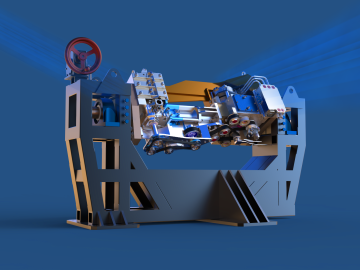
In the quest for advanced vehicles with higher energy efficiency and ultra-low emissions, ORNL researchers are accelerating a research engine that gives scientists and engineers an unprecedented view inside the atomic-level workings of combustion engines in real time.
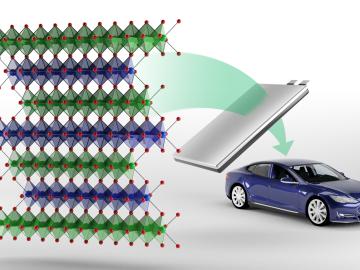
Oak Ridge National Laboratory researchers have developed a new family of cathodes with the potential to replace the costly cobalt-based cathodes typically found in today’s lithium-ion batteries that power electric vehicles and consumer electronics.
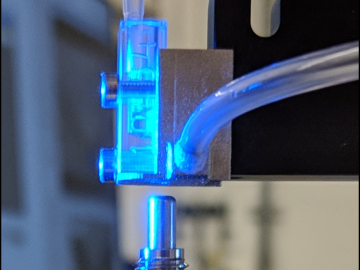
Researchers at the Department of Energy’s Oak Ridge National Laboratory have received five 2019 R&D 100 Awards, increasing the lab’s total to 221 since the award’s inception in 1963.
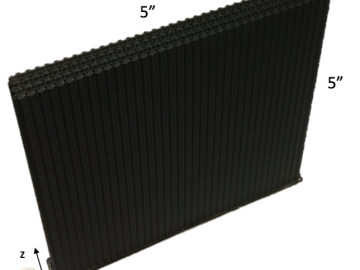
A team including Oak Ridge National Laboratory and University of Tennessee researchers demonstrated a novel 3D printing approach called Z-pinning that can increase the material’s strength and toughness by more than three and a half times compared to conventional additive manufacturing processes.