Filter News
Area of Research
- (-) Advanced Manufacturing (19)
- (-) National Security (6)
- Biological Systems (1)
- Biology and Environment (47)
- Building Technologies (1)
- Clean Energy (93)
- Computational Biology (1)
- Computational Engineering (2)
- Fusion and Fission (2)
- Fusion Energy (2)
- Materials (49)
- Materials for Computing (8)
- Mathematics (1)
- Neutron Science (10)
- Nuclear Science and Technology (6)
- Supercomputing (31)
News Type
News Topics
- (-) 3-D Printing/Advanced Manufacturing (21)
- (-) Bioenergy (2)
- (-) Chemical Sciences (2)
- (-) Composites (3)
- (-) Summit (1)
- Advanced Reactors (2)
- Artificial Intelligence (9)
- Big Data (2)
- Biology (2)
- Biomedical (1)
- Climate Change (2)
- Computer Science (13)
- Coronavirus (1)
- Cybersecurity (15)
- Energy Storage (2)
- Environment (2)
- Exascale Computing (1)
- Frontier (1)
- Fusion (2)
- Grid (4)
- High-Performance Computing (1)
- Machine Learning (7)
- Materials (5)
- Materials Science (5)
- National Security (21)
- Neutron Science (2)
- Nuclear Energy (5)
- Partnerships (4)
- Physics (1)
- Quantum Science (1)
- Security (8)
- Space Exploration (1)
- Sustainable Energy (7)
- Transformational Challenge Reactor (1)
- Transportation (2)
Media Contacts
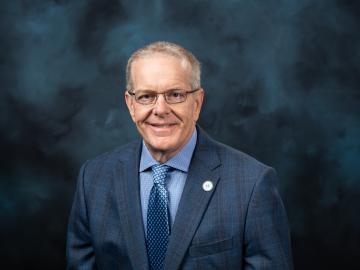
Craig Blue, Defense Manufacturing Program Director at the Department of Energy’s Oak Ridge National Laboratory, was recently elected to a two-year term on the Institute for Advanced Composites Manufacturing Innovation Consortium Council, a body of professionals from academia, state governments, and national laboratories that provides strategic direction and oversight to IACMI.

A partnership of ORNL, the Tennessee Department of Economic and Community Development, the Community Reuse Organization of East Tennessee and TVA that aims to attract nuclear energy-related firms to Oak Ridge has been recognized with a state and local economic development award from the Federal Laboratory Consortium.

Laboratory Director Thomas Zacharia presented five Director’s Awards during Saturday night's annual Awards Night event hosted by UT-Battelle, which manages ORNL for the Department of Energy.
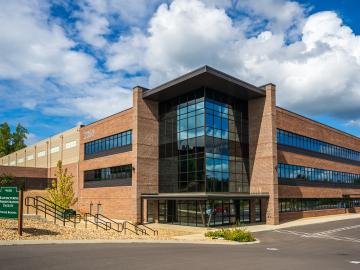
ORNL scientists will present new technologies available for licensing during the annual Technology Innovation Showcase. The event is 9 a.m. to 3 p.m. Thursday, June 16, at the Manufacturing Demonstration Facility at ORNL’s Hardin Valley campus.
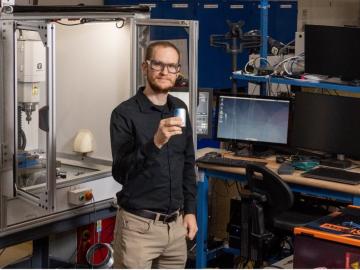
How an Alvin M. Weinberg Fellow is increasing security for critical infrastructure components
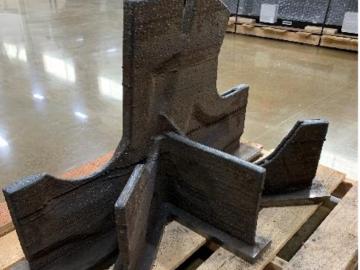
Oak Ridge National Laboratory researchers recently used large-scale additive manufacturing with metal to produce a full-strength steel component for a wind turbine, proving the technique as a viable alternative to
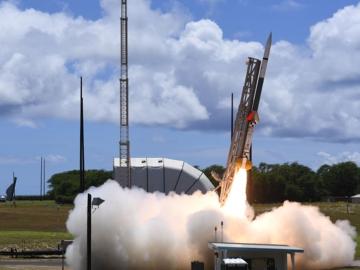
Oak Ridge National Laboratory researchers have developed a novel process to manufacture extreme heat resistant carbon-carbon composites. The performance of these materials will be tested in a U.S. Navy rocket that NASA will launch this fall.

A research team at Oak Ridge National Laboratory have 3D printed a thermal protection shield, or TPS, for a capsule that will launch with the Cygnus cargo spacecraft as part of the supply mission to the International Space Station.
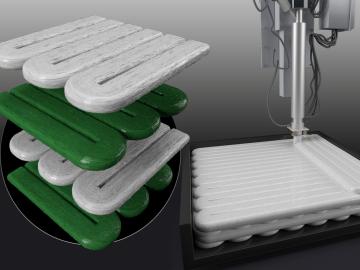
Oak Ridge National Laboratory researchers combined additive manufacturing with conventional compression molding to produce high-performance thermoplastic composites reinforced with short carbon fibers.

A team of Oak Ridge National Laboratory researchers demonstrated that an additively manufactured hot stamping die – a tool used to create car body components – cooled faster than those produced by conventional manufacturing methods.