Filter News
Area of Research
- (-) Advanced Manufacturing (14)
- (-) Building Technologies (3)
- (-) Computational Engineering (1)
- (-) Electricity and Smart Grid (2)
- Biology and Environment (17)
- Clean Energy (88)
- Computer Science (7)
- Energy Sciences (1)
- Functional Materials for Energy (1)
- Fusion and Fission (7)
- Fusion Energy (6)
- Isotopes (7)
- Materials (29)
- Materials for Computing (6)
- National Security (6)
- Neutron Science (3)
- Nuclear Science and Technology (14)
- Nuclear Systems Modeling, Simulation and Validation (1)
- Quantum information Science (1)
- Sensors and Controls (1)
- Supercomputing (14)
- Transportation Systems (2)
News Topics
- (-) 3-D Printing/Advanced Manufacturing (13)
- (-) Big Data (1)
- (-) Grid (2)
- (-) Nuclear Energy (1)
- (-) Sustainable Energy (7)
- Advanced Reactors (1)
- Artificial Intelligence (2)
- Bioenergy (1)
- Buildings (4)
- Clean Water (1)
- Climate Change (1)
- Composites (3)
- Computer Science (4)
- Cybersecurity (1)
- Decarbonization (1)
- Energy Storage (1)
- Environment (2)
- Frontier (1)
- Fusion (1)
- High-Performance Computing (1)
- Machine Learning (2)
- Materials (5)
- Materials Science (5)
- Mathematics (1)
- Simulation (1)
- Space Exploration (1)
Media Contacts
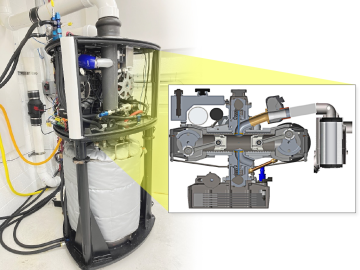
ORNL researchers, in collaboration with Enginuity Power Systems, demonstrated that a micro combined heat and power prototype, or mCHP, with a piston engine can achieve an overall energy efficiency greater than 93%.
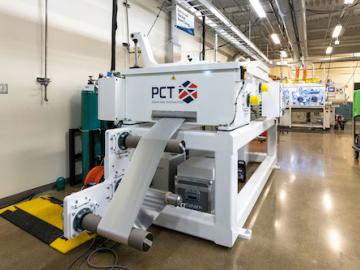
Researchers at the Department of Energy’s Oak Ridge National Laboratory and their technologies have received seven 2022 R&D 100 Awards, plus special recognition for a battery-related green technology product.
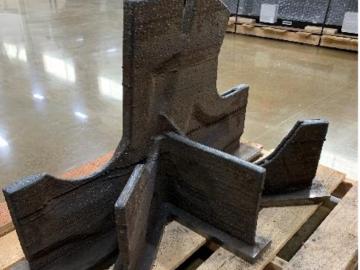
Oak Ridge National Laboratory researchers recently used large-scale additive manufacturing with metal to produce a full-strength steel component for a wind turbine, proving the technique as a viable alternative to

Oak Ridge National Laboratory researchers determined that designing polymers specifically with upcycling in mind could reduce future plastic waste considerably and facilitate a circular economy where the material is used repeatedly.
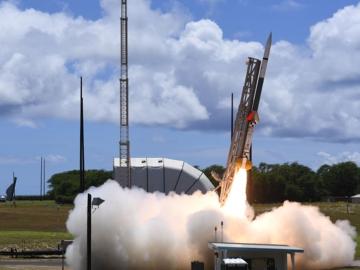
Oak Ridge National Laboratory researchers have developed a novel process to manufacture extreme heat resistant carbon-carbon composites. The performance of these materials will be tested in a U.S. Navy rocket that NASA will launch this fall.

A research team at Oak Ridge National Laboratory have 3D printed a thermal protection shield, or TPS, for a capsule that will launch with the Cygnus cargo spacecraft as part of the supply mission to the International Space Station.
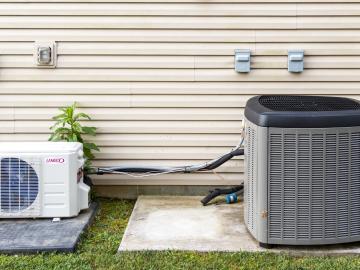
Oak Ridge National Laboratory researchers designed and field-tested an algorithm that could help homeowners maintain comfortable temperatures year-round while minimizing utility costs.
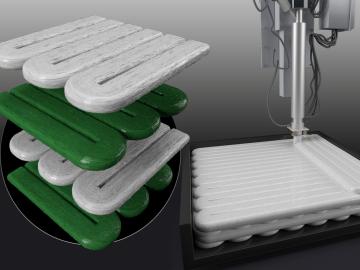
Oak Ridge National Laboratory researchers combined additive manufacturing with conventional compression molding to produce high-performance thermoplastic composites reinforced with short carbon fibers.

A team of Oak Ridge National Laboratory researchers demonstrated that an additively manufactured hot stamping die – a tool used to create car body components – cooled faster than those produced by conventional manufacturing methods.
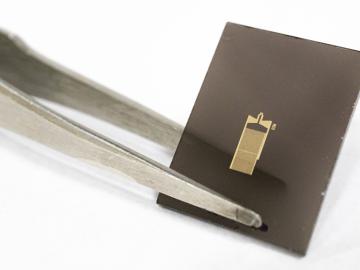
A method developed at Oak Ridge National Laboratory to print high-fidelity, passive sensors for energy applications can reduce the cost of monitoring critical power grid assets.