Filter News
Area of Research
- (-) Advanced Manufacturing (13)
- (-) Supercomputing (17)
- Biology and Environment (8)
- Building Technologies (1)
- Clean Energy (42)
- Computational Biology (1)
- Computational Engineering (1)
- Computer Science (6)
- Electricity and Smart Grid (1)
- Functional Materials for Energy (1)
- Fusion Energy (2)
- Materials (16)
- Materials for Computing (4)
- National Security (2)
- Neutron Science (2)
- Quantum information Science (4)
News Type
News Topics
- (-) 3-D Printing/Advanced Manufacturing (14)
- (-) Big Data (5)
- (-) Machine Learning (3)
- (-) Quantum Science (4)
- (-) Summit (7)
- Advanced Reactors (2)
- Artificial Intelligence (4)
- Bioenergy (1)
- Biology (2)
- Biomedical (5)
- Buildings (1)
- Chemical Sciences (2)
- Climate Change (3)
- Composites (3)
- Computer Science (23)
- Coronavirus (3)
- Critical Materials (3)
- Cybersecurity (2)
- Decarbonization (1)
- Energy Storage (4)
- Environment (5)
- Exascale Computing (4)
- Frontier (4)
- Fusion (2)
- Grid (1)
- High-Performance Computing (10)
- Isotopes (1)
- Materials (10)
- Materials Science (8)
- Microscopy (1)
- Molten Salt (1)
- Nanotechnology (3)
- National Security (1)
- Neutron Science (1)
- Nuclear Energy (3)
- Physics (1)
- Polymers (2)
- Quantum Computing (5)
- Security (1)
- Simulation (4)
- Software (1)
- Space Exploration (3)
- Sustainable Energy (7)
- Transportation (2)
Media Contacts
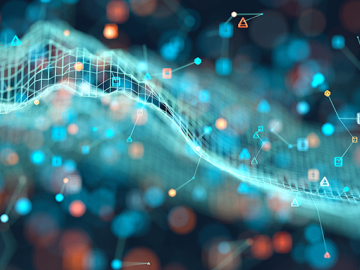
A study led by Oak Ridge National Laboratory researchers identifies a new potential application in quantum computing that could be part of the next computational revolution.
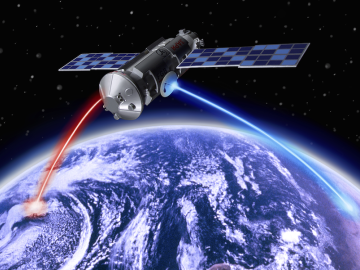
A study by Oak Ridge National Laboratory researchers has demonstrated how satellites could enable more efficient, secure quantum networks.
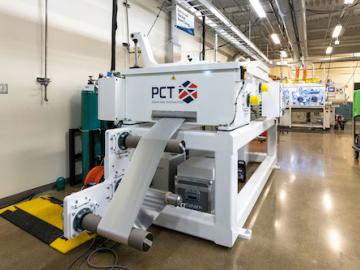
Researchers at the Department of Energy’s Oak Ridge National Laboratory and their technologies have received seven 2022 R&D 100 Awards, plus special recognition for a battery-related green technology product.
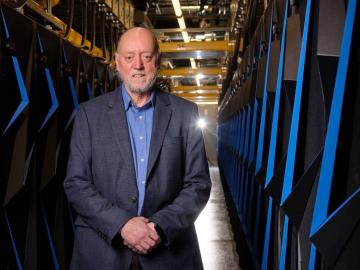
A force within the supercomputing community, Jack Dongarra developed software packages that became standard in the industry, allowing high-performance computers to become increasingly more powerful in recent decades.
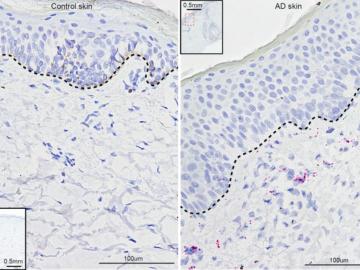
University of Pennsylvania researchers called on computational systems biology expertise at Oak Ridge National Laboratory to analyze large datasets of single-cell RNA sequencing from skin samples afflicted with atopic dermatitis.
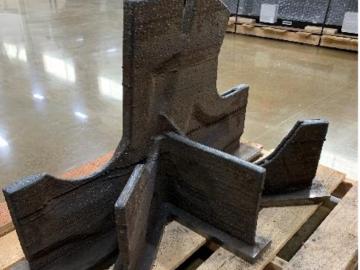
Oak Ridge National Laboratory researchers recently used large-scale additive manufacturing with metal to produce a full-strength steel component for a wind turbine, proving the technique as a viable alternative to
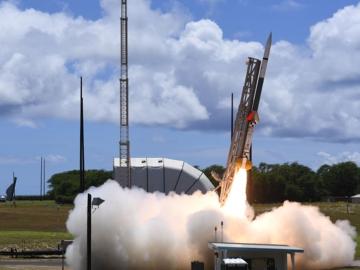
Oak Ridge National Laboratory researchers have developed a novel process to manufacture extreme heat resistant carbon-carbon composites. The performance of these materials will be tested in a U.S. Navy rocket that NASA will launch this fall.

A research team at Oak Ridge National Laboratory have 3D printed a thermal protection shield, or TPS, for a capsule that will launch with the Cygnus cargo spacecraft as part of the supply mission to the International Space Station.
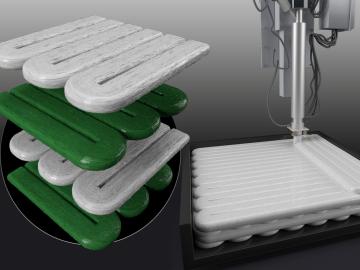
Oak Ridge National Laboratory researchers combined additive manufacturing with conventional compression molding to produce high-performance thermoplastic composites reinforced with short carbon fibers.

A team of Oak Ridge National Laboratory researchers demonstrated that an additively manufactured hot stamping die – a tool used to create car body components – cooled faster than those produced by conventional manufacturing methods.