Filter News
Area of Research
- (-) Clean Energy (20)
- Advanced Manufacturing (1)
- Biology and Environment (22)
- Computational Biology (2)
- Computational Engineering (1)
- Computer Science (4)
- Fuel Cycle Science and Technology (1)
- Fusion and Fission (16)
- Fusion Energy (13)
- Isotopes (1)
- Materials (18)
- Materials for Computing (4)
- National Security (30)
- Neutron Science (7)
- Nuclear Science and Technology (15)
- Nuclear Systems Modeling, Simulation and Validation (1)
- Supercomputing (41)
News Type
News Topics
- (-) Advanced Reactors (2)
- (-) Coronavirus (7)
- (-) Machine Learning (2)
- (-) Mercury (2)
- (-) National Security (1)
- (-) Polymers (6)
- (-) Summit (2)
- 3-D Printing/Advanced Manufacturing (45)
- Artificial Intelligence (3)
- Big Data (1)
- Bioenergy (12)
- Biology (6)
- Biomedical (3)
- Biotechnology (2)
- Buildings (24)
- Chemical Sciences (4)
- Clean Water (7)
- Climate Change (14)
- Composites (11)
- Computer Science (20)
- Critical Materials (4)
- Cybersecurity (6)
- Decarbonization (19)
- Energy Storage (41)
- Environment (33)
- Fossil Energy (1)
- Grid (29)
- High-Performance Computing (3)
- Hydropower (2)
- Materials (17)
- Materials Science (13)
- Mathematics (2)
- Microelectronics (1)
- Microscopy (5)
- Nanotechnology (4)
- Net Zero (2)
- Neutron Science (2)
- Nuclear Energy (3)
- Partnerships (4)
- Physics (1)
- Quantum Science (7)
- Security (3)
- Simulation (2)
- Space Exploration (3)
- Statistics (1)
- Sustainable Energy (41)
- Transportation (43)
Media Contacts
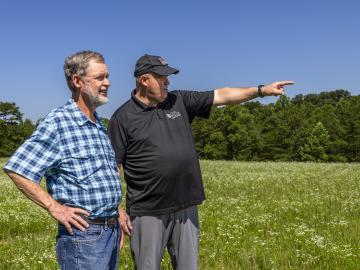
Carl Dukes’ career as an adept communicator got off to a slow start: He was about 5 years old when he spoke for the first time. “I’ve been making up for lost time ever since,” joked Dukes, a technical professional at the Department of Energy’s Oak Ridge National Laboratory.
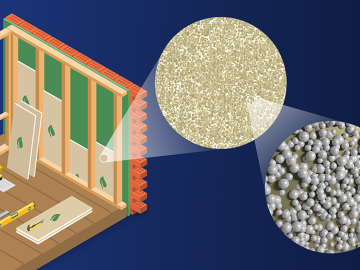
Scientists at ORNL developed a competitive, eco-friendly alternative made without harmful blowing agents.
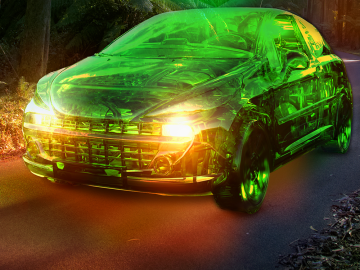
Oak Ridge National Laboratory scientists designed a recyclable polymer for carbon-fiber composites to enable circular manufacturing of parts that boost energy efficiency in automotive, wind power and aerospace applications.
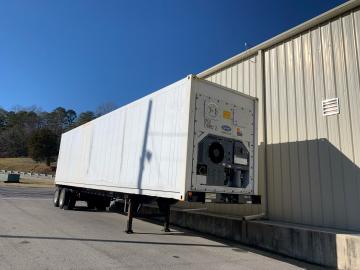
Oak Ridge National Laboratory researchers have retrofitted a commercial refrigeration container designed to ensure COVID-19 vaccines remain at ultra-low temperatures during long transport and while locally stored.
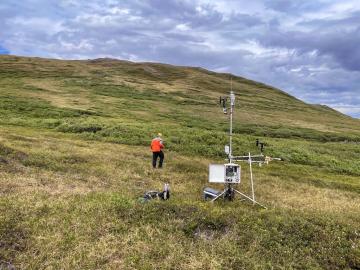
Improved data, models and analyses from ORNL scientists and many other researchers in the latest global climate assessment report provide new levels of certainty about what the future holds for the planet
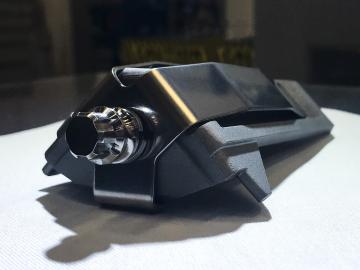
Four first-of-a-kind 3D-printed fuel assembly brackets, produced at the Department of Energy’s Manufacturing Demonstration Facility at Oak Ridge National Laboratory, have been installed and are now under routine operating

A collaboration between the ORNL and a Florida-based medical device manufacturer has led to the addition of 500 jobs in the Miami area to support the mass production of N95 respirator masks.
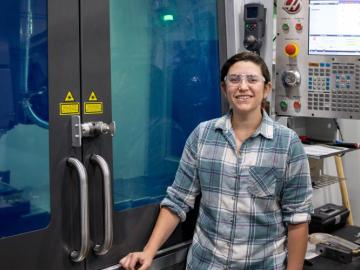
Growing up in Florida, Emma Betters was fascinated by rockets and for good reason. Any time she wanted to see a space shuttle launch from NASA’s nearby Kennedy Space Center, all she had to do was sit on her front porch.
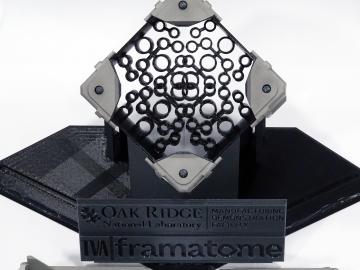
The Transformational Challenge Reactor, or TCR, a microreactor built using 3D printing and other new advanced technologies, could be operational by 2024.