
Filter News
Area of Research
- (-) Advanced Manufacturing (1)
- (-) Neutron Science (14)
- (-) Nuclear Science and Technology (10)
- Biology and Environment (86)
- Biology and Soft Matter (1)
- Clean Energy (49)
- Climate and Environmental Systems (3)
- Computational Biology (1)
- Computer Science (1)
- Fusion and Fission (9)
- Fusion Energy (1)
- Isotopes (22)
- Materials (35)
- Materials for Computing (4)
- National Security (25)
- Sensors and Controls (1)
- Supercomputing (58)
News Type
News Topics
- (-) Advanced Reactors (6)
- (-) Artificial Intelligence (6)
- (-) Climate Change (1)
- (-) Environment (6)
- (-) Isotopes (4)
- (-) Security (2)
- 3-D Printing/Advanced Manufacturing (17)
- Big Data (2)
- Bioenergy (7)
- Biology (5)
- Biomedical (10)
- Biotechnology (1)
- Chemical Sciences (1)
- Clean Water (2)
- Composites (1)
- Computer Science (16)
- Coronavirus (9)
- Cybersecurity (2)
- Decarbonization (3)
- Energy Storage (4)
- Fossil Energy (1)
- Frontier (1)
- Fusion (8)
- High-Performance Computing (2)
- Machine Learning (4)
- Materials (11)
- Materials Science (23)
- Mathematics (1)
- Microscopy (2)
- Molten Salt (1)
- Nanotechnology (8)
- National Security (2)
- Neutron Science (74)
- Nuclear Energy (25)
- Physics (9)
- Polymers (1)
- Quantum Computing (1)
- Quantum Science (5)
- Space Exploration (5)
- Summit (6)
- Sustainable Energy (5)
- Transformational Challenge Reactor (4)
- Transportation (3)
Media Contacts
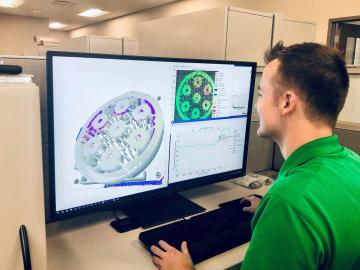
Oak Ridge National Laboratory researchers have developed artificial intelligence software for powder bed 3D printers that assesses the quality of parts in real time, without the need for expensive characterization equipment.
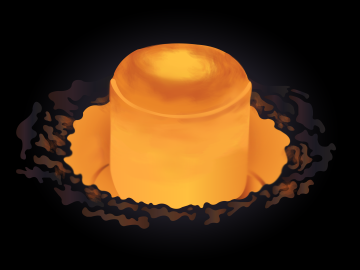
After its long journey to Mars beginning this summer, NASA’s Perseverance rover will be powered across the planet’s surface in part by plutonium produced at the Department of Energy’s Oak Ridge National Laboratory.
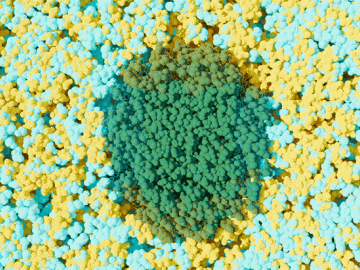
Scientists at ORNL used neutron scattering and supercomputing to better understand how an organic solvent and water work together to break down plant biomass, creating a pathway to significantly improve the production of renewable
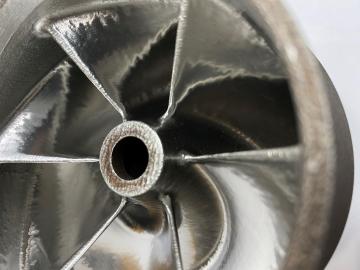
Scientists at the Department of Energy Manufacturing Demonstration Facility at ORNL have their eyes on the prize: the Transformational Challenge Reactor, or TCR, a microreactor built using 3D printing and other new approaches that will be up and running by 2023.
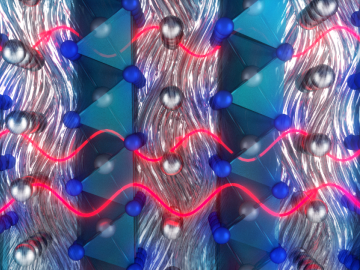
Research by an international team led by Duke University and the Department of Energy’s Oak Ridge National Laboratory scientists could speed the way to safer rechargeable batteries for consumer electronics such as laptops and cellphones.

Researchers at the Department of Energy’s Oak Ridge National Laboratory are refining their design of a 3D-printed nuclear reactor core, scaling up the additive manufacturing process necessary to build it, and developing methods
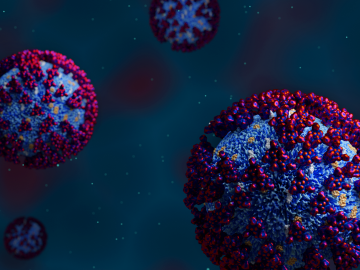
In the race to identify solutions to the COVID-19 pandemic, researchers at the Department of Energy’s Oak Ridge National Laboratory are joining the fight by applying expertise in computational science, advanced manufacturing, data science and neutron science.
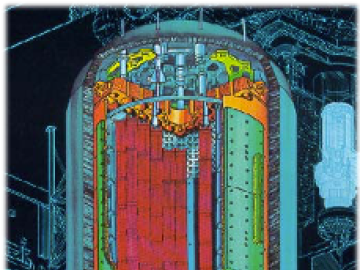
A software package, 10 years in the making, that can predict the behavior of nuclear reactors’ cores with stunning accuracy has been licensed commercially for the first time.
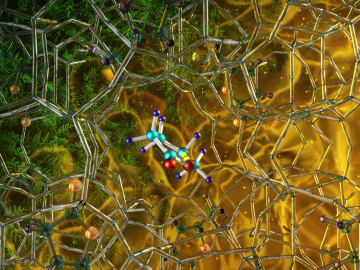
Illustration of the optimized zeolite catalyst, or NbAlS-1, which enables a highly efficient chemical reaction to create butene, a renewable source of energy, without expending high amounts of energy for the conversion. Credit: Jill Hemman, Oak Ridge National Laboratory/U.S. Dept. of Energy
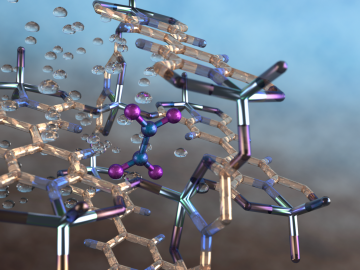
An international team of scientists, led by the University of Manchester, has developed a metal-organic framework, or MOF, material