Filter News
Area of Research
- (-) Clean Energy (58)
- (-) National Security (7)
- Advanced Manufacturing (3)
- Biological Systems (1)
- Biology and Environment (77)
- Biology and Soft Matter (1)
- Climate and Environmental Systems (1)
- Fusion and Fission (6)
- Materials (22)
- Materials for Computing (2)
- Neutron Science (8)
- Nuclear Science and Technology (3)
- Quantum information Science (2)
- Supercomputing (27)
News Topics
- (-) 3-D Printing/Advanced Manufacturing (23)
- (-) Bioenergy (11)
- (-) Composites (2)
- (-) Decarbonization (16)
- (-) Environment (21)
- (-) Microscopy (2)
- (-) Polymers (1)
- Advanced Reactors (2)
- Artificial Intelligence (8)
- Big Data (4)
- Biology (6)
- Biomedical (3)
- Biotechnology (2)
- Buildings (11)
- Chemical Sciences (3)
- Clean Water (3)
- Climate Change (11)
- Computer Science (15)
- Coronavirus (6)
- Cybersecurity (13)
- Energy Storage (20)
- Fossil Energy (1)
- Grid (16)
- High-Performance Computing (5)
- Machine Learning (8)
- Materials (6)
- Materials Science (6)
- Mathematics (1)
- Mercury (1)
- Microelectronics (1)
- Nanotechnology (3)
- National Security (23)
- Net Zero (1)
- Neutron Science (4)
- Nuclear Energy (4)
- Partnerships (4)
- Quantum Science (2)
- Security (8)
- Simulation (1)
- Space Exploration (1)
- Summit (3)
- Sustainable Energy (14)
- Transportation (17)
Media Contacts

Jack Orebaugh, a forensic anthropology major at the University of Tennessee, Knoxville, has a big heart for families with missing loved ones. When someone disappears in an area of dense vegetation, search and recovery efforts can be difficult, especially when a missing person’s last location is unknown. Recognizing the agony of not knowing what happened to a family or friend, Orebaugh decided to use his internship at the Department of Energy’s Oak Ridge National Laboratory to find better ways to search for lost and deceased people using cameras and drones.
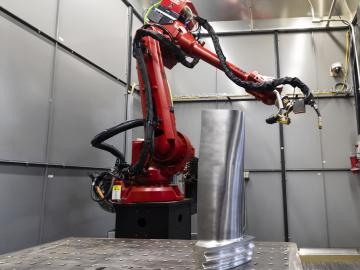
Researchers at ORNL became the first to 3D-print large rotating steam turbine blades for generating energy in power plants.
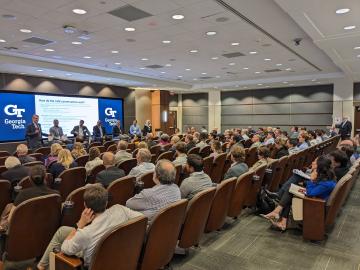
ORNL's Climate Change Science Institute and the Georgia Institute of Technology hosted a Southeast Decarbonization Workshop in November that drew scientists and representatives from government, industry, non-profits and other organizations to
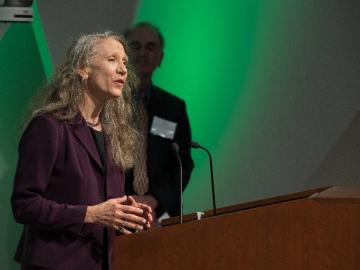
The founder of a startup company who is working with ORNL has won an Environmental Protection Agency Green Chemistry Challenge Award for a unique air pollution control technology.
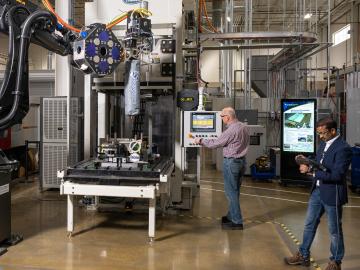
Researchers at ORNL are extending the boundaries of composite-based materials used in additive manufacturing, or AM. ORNL is working with industrial partners who are exploring AM, also known as 3D printing, as a path to higher production levels and fewer supply chain interruptions.

In fiscal year 2023 — Oct. 1–Sept. 30, 2023 — Oak Ridge National Laboratory was awarded more than $8 million in technology maturation funding through the Department of Energy’s Technology Commercialization Fund, or TCF.
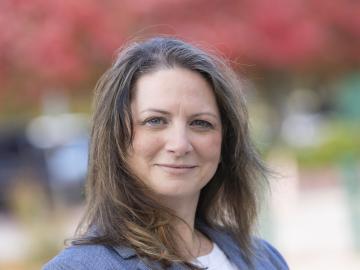
Michelle Kidder, a senior R&D staff scientist at ORNL, has received the American Chemical Society’s Energy and Fuels Division’s Mid-Career Award for sustained and distinguished contributions to the field of energy and fuel chemistry.

ORNL, the Department of Energy’s largest multidisciplinary laboratory, and Fairbanks Morse Defense, a portfolio company of Arcline Investment Management, have entered into a Memorandum of Understanding to collaborate on the development and integration of alternative fuel technologies aimed at reducing the marine engine’s reliance on fossil fuels.

Yarom Polsky, director of the Manufacturing Science Division, or MSD, at the Department of Energy’s Oak Ridge National Laboratory, has been elected a Fellow of the American Society of Mechanical Engineers, or ASME.
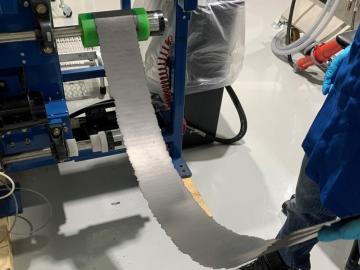
Early experiments at the Department of Energy’s Oak Ridge National Laboratory have revealed significant benefits to a dry battery manufacturing process. This eliminates the use of solvents and is more affordable, while showing promise for delivering a battery that is durable, less weighed down by inactive elements, and able to maintain a high capacity after use.