Filter News
Area of Research
- (-) Computational Biology (2)
- (-) Fusion and Fission (4)
- (-) Materials (10)
- (-) Nuclear Science and Technology (9)
- Advanced Manufacturing (1)
- Biological Systems (1)
- Biology and Environment (18)
- Clean Energy (10)
- Computational Engineering (1)
- Computer Science (5)
- Fusion Energy (7)
- Isotopes (4)
- Materials for Computing (3)
- National Security (8)
- Neutron Science (13)
- Nuclear Systems Modeling, Simulation and Validation (1)
- Quantum information Science (7)
- Supercomputing (59)
News Type
News Topics
- (-) Advanced Reactors (12)
- (-) Artificial Intelligence (6)
- (-) Biomedical (7)
- (-) Quantum Science (1)
- (-) Summit (2)
- 3-D Printing/Advanced Manufacturing (14)
- Big Data (2)
- Bioenergy (3)
- Biology (2)
- Buildings (2)
- Chemical Sciences (12)
- Clean Water (3)
- Composites (6)
- Computer Science (12)
- Coronavirus (4)
- Critical Materials (5)
- Cybersecurity (1)
- Decarbonization (3)
- Energy Storage (14)
- Environment (9)
- Exascale Computing (2)
- Frontier (1)
- Fusion (25)
- Grid (2)
- High-Performance Computing (5)
- Isotopes (10)
- ITER (4)
- Machine Learning (2)
- Materials (31)
- Materials Science (36)
- Mathematics (1)
- Microscopy (12)
- Molten Salt (5)
- Nanotechnology (16)
- Net Zero (1)
- Neutron Science (17)
- Nuclear Energy (51)
- Partnerships (3)
- Physics (15)
- Polymers (10)
- Quantum Computing (2)
- Security (2)
- Simulation (2)
- Space Exploration (5)
- Sustainable Energy (8)
- Transformational Challenge Reactor (3)
- Transportation (11)
Media Contacts

ORNL hosted its fourth Artificial Intelligence for Robust Engineering and Science, or AIRES, workshop from April 18-20. Over 100 attendees from government, academia and industry convened to identify research challenges and investment areas, carving the future of the discipline.

Oak Ridge National Laboratory researchers serendipitously discovered when they automated the beam of an electron microscope to precisely drill holes in the atomically thin lattice of graphene, the drilled holes closed up.
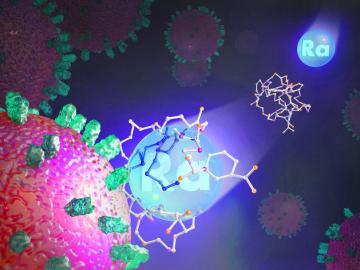
Researchers at ORNL explored radium’s chemistry to advance cancer treatments using ionizing radiation.

A study led by researchers at ORNL could help make materials design as customizable as point-and-click.
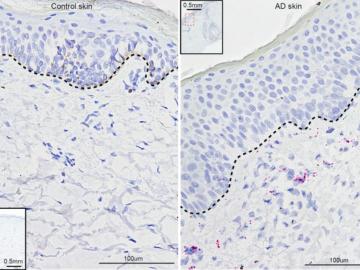
University of Pennsylvania researchers called on computational systems biology expertise at Oak Ridge National Laboratory to analyze large datasets of single-cell RNA sequencing from skin samples afflicted with atopic dermatitis.

Staff at Oak Ridge National Laboratory organized transport for a powerful component that is critical to the world’s largest experiment, the international ITER project.
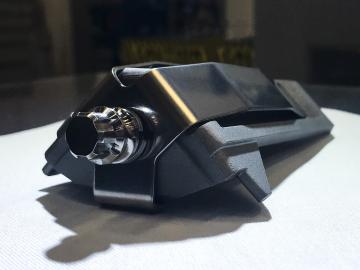
Four first-of-a-kind 3D-printed fuel assembly brackets, produced at the Department of Energy’s Manufacturing Demonstration Facility at Oak Ridge National Laboratory, have been installed and are now under routine operating

An ORNL-led team comprising researchers from multiple DOE national laboratories is using artificial intelligence and computational screening techniques – in combination with experimental validation – to identify and design five promising drug therapy approaches to target the SARS-CoV-2 virus.
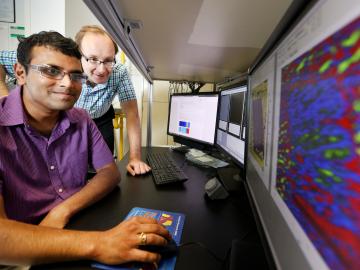
At the Department of Energy’s Oak Ridge National Laboratory, scientists use artificial intelligence, or AI, to accelerate the discovery and development of materials for energy and information technologies.
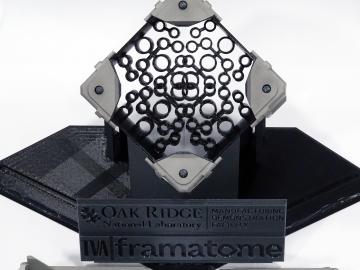
The Transformational Challenge Reactor, or TCR, a microreactor built using 3D printing and other new advanced technologies, could be operational by 2024.