Filter News
Area of Research
- (-) Advanced Manufacturing (14)
- (-) Materials for Computing (7)
- Biology and Environment (33)
- Building Technologies (1)
- Clean Energy (84)
- Computational Engineering (2)
- Computer Science (8)
- Electricity and Smart Grid (2)
- Fusion and Fission (19)
- Fusion Energy (9)
- Isotopes (2)
- Materials (36)
- Mathematics (1)
- National Security (19)
- Neutron Science (12)
- Nuclear Science and Technology (26)
- Nuclear Systems Modeling, Simulation and Validation (1)
- Quantum information Science (7)
- Sensors and Controls (1)
- Supercomputing (39)
News Type
News Topics
- (-) 3-D Printing/Advanced Manufacturing (16)
- (-) Microscopy (3)
- (-) Nuclear Energy (1)
- (-) Quantum Science (2)
- Advanced Reactors (1)
- Bioenergy (1)
- Biology (1)
- Biomedical (1)
- Chemical Sciences (2)
- Climate Change (1)
- Composites (3)
- Computer Science (5)
- Coronavirus (3)
- Decarbonization (1)
- Energy Storage (2)
- Fusion (1)
- Materials (14)
- Materials Science (15)
- Nanotechnology (6)
- Neutron Science (5)
- Polymers (2)
- Quantum Computing (1)
- Simulation (1)
- Space Exploration (1)
- Sustainable Energy (6)
- Transportation (3)
Media Contacts

Scientists at ORNL have developed 3-D-printed collimator techniques that can be used to custom design collimators that better filter out noise during different types of neutron scattering experiments
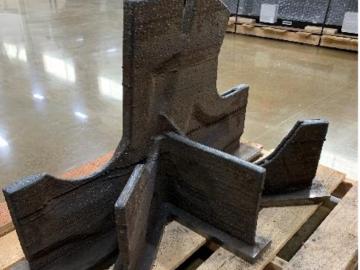
Oak Ridge National Laboratory researchers recently used large-scale additive manufacturing with metal to produce a full-strength steel component for a wind turbine, proving the technique as a viable alternative to

A team led by the U.S. Department of Energy’s Oak Ridge National Laboratory demonstrated the viability of a “quantum entanglement witness” capable of proving the presence of entanglement between magnetic particles, or spins, in a quantum material.
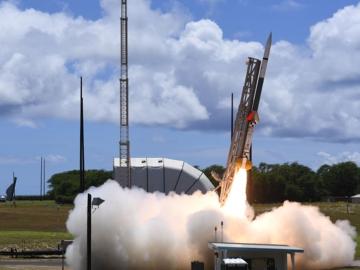
Oak Ridge National Laboratory researchers have developed a novel process to manufacture extreme heat resistant carbon-carbon composites. The performance of these materials will be tested in a U.S. Navy rocket that NASA will launch this fall.

A research team at Oak Ridge National Laboratory have 3D printed a thermal protection shield, or TPS, for a capsule that will launch with the Cygnus cargo spacecraft as part of the supply mission to the International Space Station.
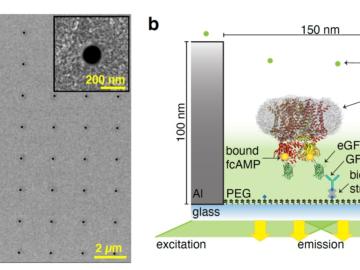
Researchers working with Oak Ridge National Laboratory developed a new method to observe how proteins, at the single-molecule level, bind with other molecules and more accurately pinpoint certain molecular behavior in complex
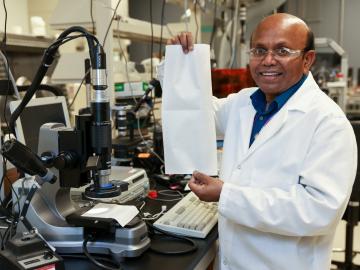
When COVID-19 was declared a pandemic in March 2020, Oak Ridge National Laboratory’s Parans Paranthaman suddenly found himself working from home like millions of others.
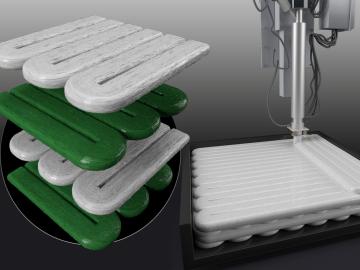
Oak Ridge National Laboratory researchers combined additive manufacturing with conventional compression molding to produce high-performance thermoplastic composites reinforced with short carbon fibers.
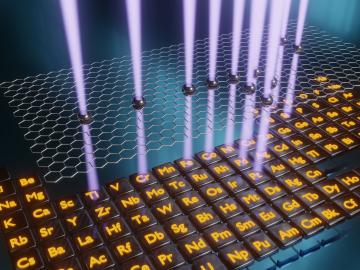
Oak Ridge National Laboratory scientists demonstrated that an electron microscope can be used to selectively remove carbon atoms from graphene’s atomically thin lattice and stitch transition-metal dopant atoms in their place.

A team of Oak Ridge National Laboratory researchers demonstrated that an additively manufactured hot stamping die – a tool used to create car body components – cooled faster than those produced by conventional manufacturing methods.