Filter News
Area of Research
- (-) Clean Energy (35)
- (-) Fuel Cycle Science and Technology (1)
- (-) Materials (13)
- (-) Neutron Science (7)
- (-) Supercomputing (8)
- Advanced Manufacturing (3)
- Biological Systems (1)
- Biology and Environment (31)
- Fusion and Fission (4)
- Isotopes (1)
- Materials for Computing (2)
- National Security (25)
- Nuclear Science and Technology (3)
- Quantum information Science (2)
News Topics
- (-) 3-D Printing/Advanced Manufacturing (26)
- (-) Bioenergy (15)
- (-) Composites (3)
- (-) Microscopy (9)
- (-) National Security (5)
- Advanced Reactors (3)
- Artificial Intelligence (23)
- Big Data (13)
- Biology (9)
- Biomedical (13)
- Biotechnology (2)
- Buildings (12)
- Chemical Sciences (8)
- Clean Water (6)
- Climate Change (19)
- Computer Science (50)
- Coronavirus (12)
- Cybersecurity (7)
- Decarbonization (18)
- Energy Storage (23)
- Environment (35)
- Exascale Computing (12)
- Fossil Energy (2)
- Frontier (13)
- Fusion (2)
- Grid (13)
- High-Performance Computing (20)
- Isotopes (6)
- Machine Learning (9)
- Materials (28)
- Materials Science (26)
- Mathematics (2)
- Mercury (1)
- Microelectronics (1)
- Nanotechnology (11)
- Net Zero (2)
- Neutron Science (39)
- Nuclear Energy (13)
- Partnerships (5)
- Physics (13)
- Polymers (5)
- Quantum Computing (11)
- Quantum Science (11)
- Security (4)
- Simulation (10)
- Software (1)
- Space Exploration (4)
- Summit (22)
- Sustainable Energy (16)
- Transformational Challenge Reactor (2)
- Transportation (22)
Media Contacts

Scientists at ORNL have developed 3D-printed collimator techniques that can be used to custom design collimators that better filter out noise during different types of neutron scattering experiments
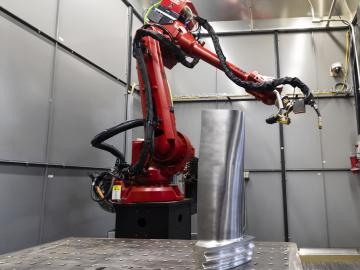
Researchers at ORNL became the first to 3D-print large rotating steam turbine blades for generating energy in power plants.

For years, Duane Starr led workshops at ORNL to help others from across the U.S. government understand uranium processing technologies. After his retirement, Starr donated a 5-foot-tall working model, built in his garage, that demonstrates vibration harmonics, consistent with operation of a super critical gas centrifuge rotor, a valuable resource to ongoing ORNL-led workshops.

Scientists at ORNL used their knowledge of complex ecosystem processes, energy systems, human dynamics, computational science and Earth-scale modeling to inform the nation’s latest National Climate Assessment, which draws attention to vulnerabilities and resilience opportunities in every region of the country.
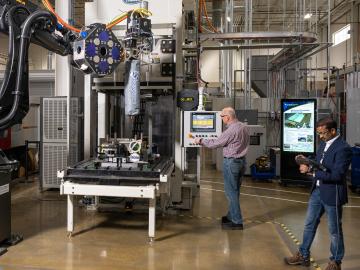
Researchers at ORNL are extending the boundaries of composite-based materials used in additive manufacturing, or AM. ORNL is working with industrial partners who are exploring AM, also known as 3D printing, as a path to higher production levels and fewer supply chain interruptions.

In fiscal year 2023 — Oct. 1–Sept. 30, 2023 — Oak Ridge National Laboratory was awarded more than $8 million in technology maturation funding through the Department of Energy’s Technology Commercialization Fund, or TCF.
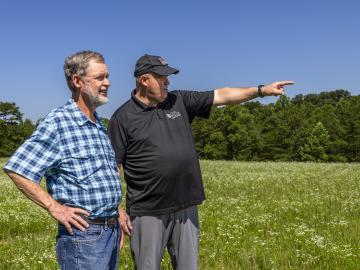
Carl Dukes’ career as an adept communicator got off to a slow start: He was about 5 years old when he spoke for the first time. “I’ve been making up for lost time ever since,” joked Dukes, a technical professional at the Department of Energy’s Oak Ridge National Laboratory.
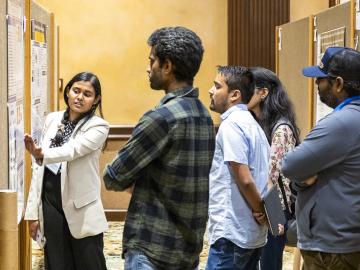
Speakers, scientific workshops, speed networking, a student poster showcase and more energized the Annual User Meeting of the Department of Energy’s Center for Nanophase Materials Sciences, or CNMS, Aug. 7-10, near Market Square in downtown Knoxville, Tennessee.

Yarom Polsky, director of the Manufacturing Science Division, or MSD, at the Department of Energy’s Oak Ridge National Laboratory, has been elected a Fellow of the American Society of Mechanical Engineers, or ASME.
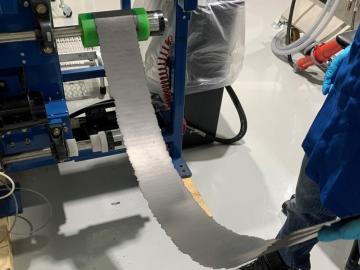
Early experiments at the Department of Energy’s Oak Ridge National Laboratory have revealed significant benefits to a dry battery manufacturing process. This eliminates the use of solvents and is more affordable, while showing promise for delivering a battery that is durable, less weighed down by inactive elements, and able to maintain a high capacity after use.