Filter News
Area of Research
- (-) Clean Energy (66)
- (-) Computational Biology (2)
- (-) National Security (21)
- (-) Quantum information Science (7)
- Advanced Manufacturing (14)
- Biology and Environment (35)
- Building Technologies (2)
- Climate and Environmental Systems (1)
- Computational Engineering (2)
- Computer Science (12)
- Fusion and Fission (3)
- Fusion Energy (3)
- Materials (19)
- Materials for Computing (8)
- Mathematics (1)
- Neutron Science (12)
- Nuclear Science and Technology (3)
- Supercomputing (82)
News Type
News Topics
- (-) 3-D Printing/Advanced Manufacturing (46)
- (-) Big Data (7)
- (-) Computer Science (30)
- (-) Machine Learning (10)
- (-) Mercury (2)
- (-) Quantum Science (8)
- (-) Summit (5)
- Advanced Reactors (2)
- Artificial Intelligence (10)
- Bioenergy (13)
- Biology (10)
- Biomedical (6)
- Biotechnology (3)
- Buildings (24)
- Chemical Sciences (4)
- Clean Water (7)
- Climate Change (17)
- Composites (11)
- Coronavirus (10)
- Critical Materials (4)
- Cybersecurity (15)
- Decarbonization (20)
- Energy Storage (41)
- Environment (37)
- Fossil Energy (1)
- Grid (33)
- High-Performance Computing (8)
- Hydropower (2)
- Materials (18)
- Materials Science (15)
- Mathematics (2)
- Microelectronics (1)
- Microscopy (5)
- Nanotechnology (5)
- National Security (23)
- Net Zero (2)
- Neutron Science (5)
- Nuclear Energy (5)
- Partnerships (4)
- Physics (1)
- Polymers (6)
- Security (9)
- Simulation (2)
- Space Exploration (3)
- Statistics (1)
- Sustainable Energy (41)
- Transportation (44)
Media Contacts
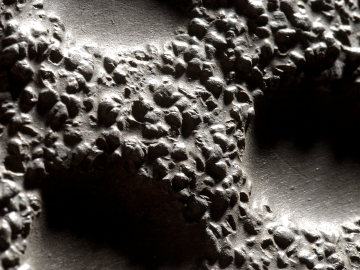
For more than 100 years, Magotteaux has provided grinding materials and castings for the mining, cement and aggregates industries. The company, based in Belgium, began its international expansion in 1968. Its second international plant has been a critical part of the Pulaski, Tennessee, economy since 1972.
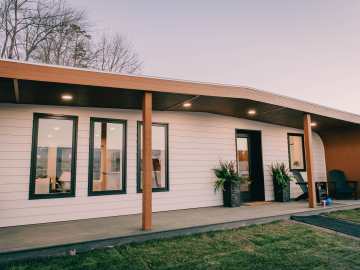
On the grounds of the University of Maine’s Advanced Structures and Composites Center sits the nation’s first additively manufactured home made entirely from biobased materials - BioHome3D.

A new report published by ORNL assessed how advanced manufacturing and materials, such as 3D printing and novel component coatings, could offer solutions to modernize the existing fleet and design new approaches to hydropower.

ORNL researchers have identified a mechanism in a 3D-printed alloy – termed “load shuffling” — that could enable the design of better-performing lightweight materials for vehicles.
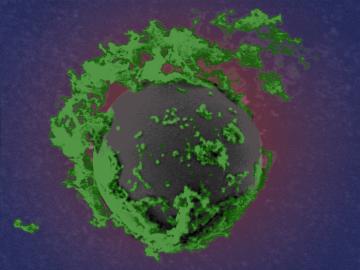
The presence of minerals called ash in plants makes little difference to the fitness of new naturally derived compound materials designed for additive manufacturing, an Oak Ridge National Laboratory-led team found.
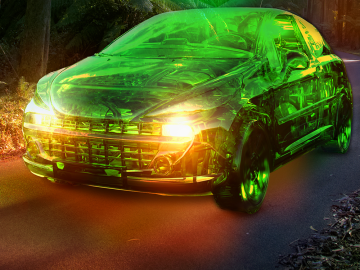
Oak Ridge National Laboratory scientists designed a recyclable polymer for carbon-fiber composites to enable circular manufacturing of parts that boost energy efficiency in automotive, wind power and aerospace applications.
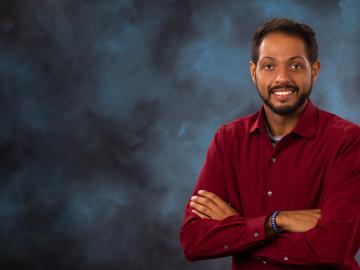
Having lived on three continents spanning the world’s four hemispheres, Philipe Ambrozio Dias understands the difficulties of moving to a new place.
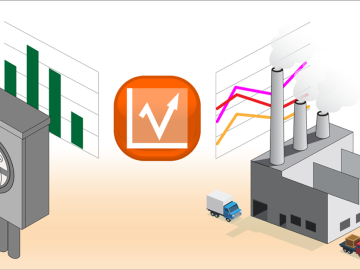
Researchers at ORNL have developed an online tool that offers industrial plants an easier way to track and download information about their energy footprint and carbon emissions.
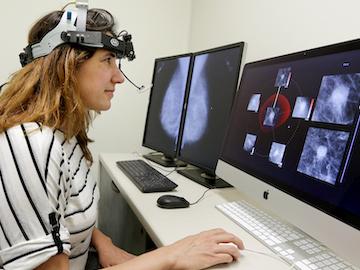
Cameras see the world differently than humans. Resolution, equipment, lighting, distance and atmospheric conditions can impact how a person interprets objects on a photo.
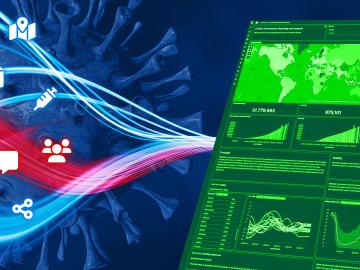
When the COVID-19 pandemic stunned the world in 2020, researchers at ORNL wondered how they could extend their support and help