Filter News
Area of Research
- (-) Clean Energy (90)
- (-) National Security (20)
- (-) Neutron Science (17)
- Advanced Manufacturing (14)
- Biological Systems (1)
- Biology and Environment (86)
- Biology and Soft Matter (1)
- Building Technologies (1)
- Climate and Environmental Systems (4)
- Computational Biology (2)
- Computational Engineering (2)
- Computer Science (5)
- Fusion and Fission (18)
- Fusion Energy (11)
- Isotopes (20)
- Materials (35)
- Materials for Computing (2)
- Mathematics (1)
- Nuclear Science and Technology (14)
- Quantum information Science (1)
- Supercomputing (36)
News Type
News Topics
- (-) 3-D Printing/Advanced Manufacturing (48)
- (-) Biomedical (11)
- (-) Composites (11)
- (-) Cybersecurity (14)
- (-) Environment (41)
- (-) Machine Learning (13)
- (-) Space Exploration (5)
- Advanced Reactors (2)
- Artificial Intelligence (14)
- Big Data (8)
- Bioenergy (16)
- Biology (9)
- Biotechnology (3)
- Buildings (24)
- Chemical Sciences (6)
- Clean Water (9)
- Climate Change (17)
- Computer Science (31)
- Coronavirus (12)
- Critical Materials (4)
- Decarbonization (21)
- Energy Storage (44)
- Fossil Energy (2)
- Grid (32)
- High-Performance Computing (7)
- Hydropower (2)
- Materials (25)
- Materials Science (24)
- Mathematics (3)
- Mercury (2)
- Microelectronics (1)
- Microscopy (6)
- Nanotechnology (7)
- National Security (23)
- Net Zero (2)
- Neutron Science (57)
- Nuclear Energy (7)
- Partnerships (4)
- Physics (2)
- Polymers (7)
- Quantum Computing (1)
- Quantum Science (4)
- Security (9)
- Simulation (2)
- Statistics (1)
- Summit (5)
- Sustainable Energy (41)
- Transportation (45)
Media Contacts

Scientists at ORNL have developed 3D-printed collimator techniques that can be used to custom design collimators that better filter out noise during different types of neutron scattering experiments
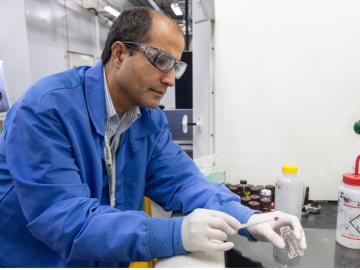
Electric vehicles can drive longer distances if their lithium-ion batteries deliver more energy in a lighter package. A prime weight-loss candidate is the current collector, a component that often adds 10% to the weight of a battery cell without contributing energy.

Jack Orebaugh, a forensic anthropology major at the University of Tennessee, Knoxville, has a big heart for families with missing loved ones. When someone disappears in an area of dense vegetation, search and recovery efforts can be difficult, especially when a missing person’s last location is unknown. Recognizing the agony of not knowing what happened to a family or friend, Orebaugh decided to use his internship at the Department of Energy’s Oak Ridge National Laboratory to find better ways to search for lost and deceased people using cameras and drones.
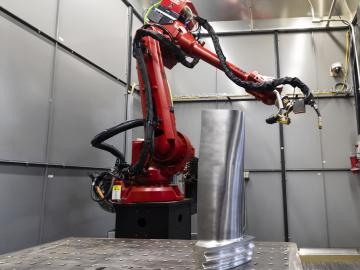
Researchers at ORNL became the first to 3D-print large rotating steam turbine blades for generating energy in power plants.

Digital twins are exactly what they sound like: virtual models of physical reality that continuously update to reflect changes in the real world.

How do you get water to float in midair? With a WAND2, of course. But it’s hardly magic. In fact, it’s a scientific device used by scientists to study matter.
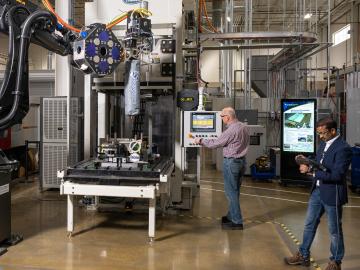
Researchers at ORNL are extending the boundaries of composite-based materials used in additive manufacturing, or AM. ORNL is working with industrial partners who are exploring AM, also known as 3D printing, as a path to higher production levels and fewer supply chain interruptions.

In fiscal year 2023 — Oct. 1–Sept. 30, 2023 — Oak Ridge National Laboratory was awarded more than $8 million in technology maturation funding through the Department of Energy’s Technology Commercialization Fund, or TCF.
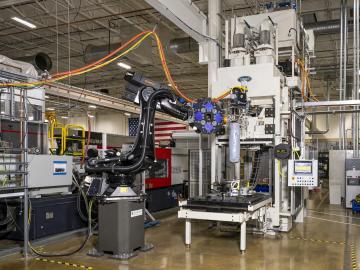
An Oak Ridge National Laboratory-developed advanced manufacturing technology, AMCM, was recently licensed by Orbital Composites and enables the rapid production of composite-based components, which could accelerate the decarbonization of vehicles

Oak Ridge National Laboratory researchers have conducted a comprehensive life cycle, cost and carbon emissions analysis on 3D-printed molds for precast concrete and determined the method is economically beneficial compared to conventional wood molds.