Filter News
Area of Research
- Advanced Manufacturing (3)
- Biological Systems (1)
- Biology and Environment (34)
- Clean Energy (48)
- Computational Biology (1)
- Electricity and Smart Grid (1)
- Fusion and Fission (6)
- Isotopes (1)
- Materials (35)
- Materials for Computing (5)
- National Security (9)
- Neutron Science (34)
- Nuclear Science and Technology (5)
- Quantum information Science (1)
- Supercomputing (36)
News Type
News Topics
- (-) 3-D Printing/Advanced Manufacturing (34)
- (-) Bioenergy (48)
- (-) Composites (5)
- (-) Exascale Computing (22)
- (-) Frontier (21)
- (-) Grid (21)
- (-) Materials Science (38)
- (-) Neutron Science (43)
- (-) Physics (25)
- Advanced Reactors (7)
- Artificial Intelligence (39)
- Big Data (21)
- Biology (53)
- Biomedical (26)
- Biotechnology (10)
- Buildings (17)
- Chemical Sciences (21)
- Clean Water (14)
- Climate Change (45)
- Computer Science (78)
- Coronavirus (17)
- Critical Materials (1)
- Cybersecurity (14)
- Decarbonization (42)
- Emergency (2)
- Energy Storage (28)
- Environment (100)
- Fossil Energy (4)
- Fusion (28)
- High-Performance Computing (40)
- Hydropower (5)
- Isotopes (23)
- ITER (2)
- Machine Learning (19)
- Materials (39)
- Mathematics (5)
- Mercury (7)
- Microelectronics (2)
- Microscopy (19)
- Molten Salt (1)
- Nanotechnology (16)
- National Security (30)
- Net Zero (7)
- Nuclear Energy (50)
- Partnerships (12)
- Polymers (7)
- Quantum Computing (15)
- Quantum Science (25)
- Renewable Energy (1)
- Security (10)
- Simulation (26)
- Software (1)
- Space Exploration (11)
- Summit (30)
- Sustainable Energy (39)
- Transformational Challenge Reactor (3)
- Transportation (26)
Media Contacts
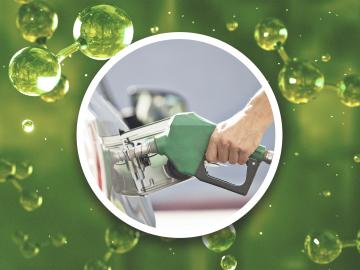
The U.S. Environmental Protection Agency has approved the registration and use of a renewable gasoline blendstock developed by Vertimass LLC and ORNL that can significantly reduce the emissions profile of vehicles when added to conventional fuels.

Scientists at Oak Ridge National Laboratory and six other Department of Energy national laboratories have developed a United States-based perspective for achieving net-zero carbon emissions.
Simulations performed on the Summit supercomputer at ORNL are cutting through that time and expense by helping researchers digitally customize the ideal alloy.
Integral to the functionality of ORNL's Frontier supercomputer is its ability to store the vast amounts of data it produces onto its file system, Orion. But even more important to the computational scientists running simulations on Frontier is their capability to quickly write and read to Orion along with effectively analyzing all that data. And that’s where ADIOS comes in.

ORNL researchers modeled how hurricane cloud cover would affect solar energy generation as a storm followed 10 possible trajectories over the Caribbean and Southern U.S.
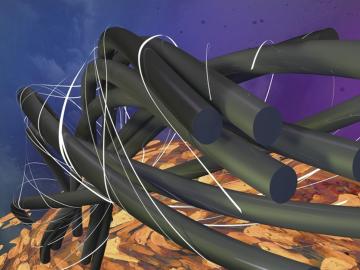
Scientists at ORNL have developed a method that demonstrates how fiber-reinforced polymer composite materials used in the automotive, aerospace and renewable energy industries can be made stronger and tougher to better withstand mechanical or structural stresses over time.
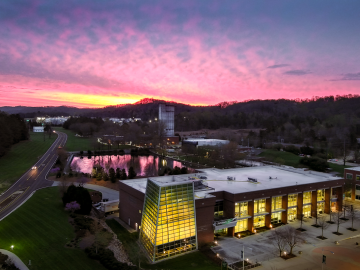
Rishi Pillai and his research team from ORNL will receive a Best Paper award from the American Society of Mechanical Engineers International Gas Turbine Institute in June at the Turbo Expo 2024 in London.
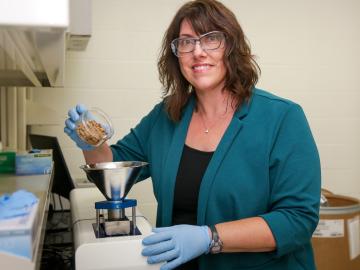
ORNL’s Erin Webb is co-leading a new Circular Bioeconomy Systems Convergent Research Initiative focused on advancing production and use of renewable carbon from Tennessee to meet societal needs.

Scientists at ORNL have developed 3D-printed collimator techniques that can be used to custom design collimators that better filter out noise during different types of neutron scattering experiments
ORNL scientists have determined how to avoid costly and potentially irreparable damage to large metallic parts fabricated through additive manufacturing, also known as 3D printing, that is caused by residual stress in the material.