Filter News
Area of Research
- Advanced Manufacturing (14)
- Biological Systems (1)
- Biology and Environment (18)
- Building Technologies (1)
- Clean Energy (64)
- Computational Biology (2)
- Fusion and Fission (4)
- Fusion Energy (2)
- Isotopes (5)
- Materials (56)
- Materials for Computing (13)
- National Security (4)
- Neutron Science (18)
- Nuclear Science and Technology (4)
- Quantum information Science (1)
- Supercomputing (23)
- Transportation Systems (1)
News Type
News Topics
- (-) 3-D Printing/Advanced Manufacturing (64)
- (-) Biomedical (37)
- (-) Composites (14)
- (-) Materials Science (68)
- (-) Nanotechnology (28)
- Advanced Reactors (19)
- Artificial Intelligence (51)
- Big Data (36)
- Bioenergy (61)
- Biology (70)
- Biotechnology (12)
- Buildings (34)
- Chemical Sciences (26)
- Clean Water (27)
- Climate Change (64)
- Computer Science (117)
- Coronavirus (28)
- Critical Materials (12)
- Cybersecurity (17)
- Decarbonization (47)
- Emergency (2)
- Energy Storage (58)
- Environment (141)
- Exascale Computing (23)
- Fossil Energy (3)
- Frontier (21)
- Fusion (36)
- Grid (41)
- High-Performance Computing (51)
- Hydropower (11)
- Irradiation (2)
- Isotopes (28)
- ITER (5)
- Machine Learning (29)
- Materials (72)
- Mathematics (6)
- Mercury (10)
- Microelectronics (2)
- Microscopy (30)
- Molten Salt (6)
- National Security (33)
- Net Zero (7)
- Neutron Science (70)
- Nuclear Energy (67)
- Partnerships (12)
- Physics (29)
- Polymers (15)
- Quantum Computing (19)
- Quantum Science (35)
- Renewable Energy (1)
- Security (11)
- Simulation (32)
- Software (1)
- Space Exploration (21)
- Statistics (1)
- Summit (36)
- Sustainable Energy (79)
- Transformational Challenge Reactor (3)
- Transportation (60)
Media Contacts
Simulations performed on the Summit supercomputer at ORNL are cutting through that time and expense by helping researchers digitally customize the ideal alloy.
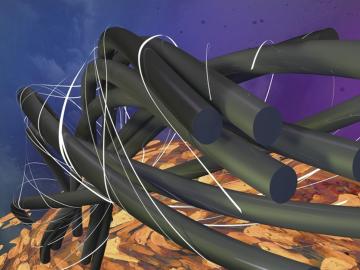
Scientists at ORNL have developed a method that demonstrates how fiber-reinforced polymer composite materials used in the automotive, aerospace and renewable energy industries can be made stronger and tougher to better withstand mechanical or structural stresses over time.
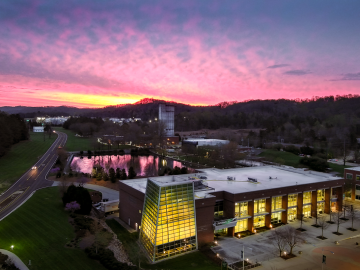
Rishi Pillai and his research team from ORNL will receive a Best Paper award from the American Society of Mechanical Engineers International Gas Turbine Institute in June at the Turbo Expo 2024 in London.
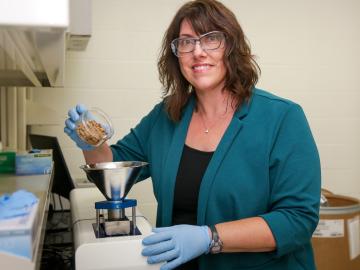
ORNL’s Erin Webb is co-leading a new Circular Bioeconomy Systems Convergent Research Initiative focused on advancing production and use of renewable carbon from Tennessee to meet societal needs.

Scientists at ORNL have developed 3D-printed collimator techniques that can be used to custom design collimators that better filter out noise during different types of neutron scattering experiments
ORNL scientists have determined how to avoid costly and potentially irreparable damage to large metallic parts fabricated through additive manufacturing, also known as 3D printing, that is caused by residual stress in the material.

SkyNano, an Innovation Crossroads alumnus, held a ribbon-cutting for their new facility. SkyNano exemplifies using DOE resources to build a successful clean energy company, making valuable carbon nanotubes from waste CO2.
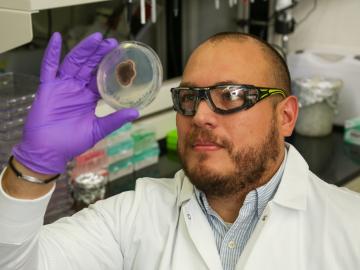
New computational framework speeds discovery of fungal metabolites, key to plant health and used in drug therapies and for other uses.
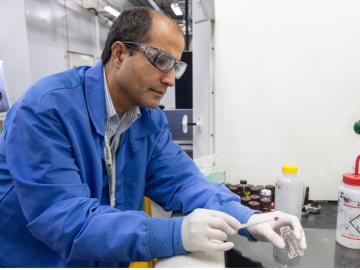
Electric vehicles can drive longer distances if their lithium-ion batteries deliver more energy in a lighter package. A prime weight-loss candidate is the current collector, a component that often adds 10% to the weight of a battery cell without contributing energy.
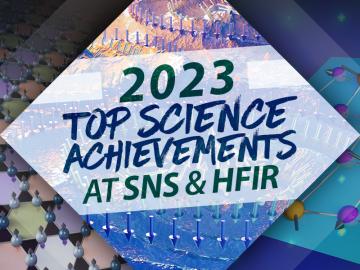
The 2023 top science achievements from HFIR and SNS feature a broad range of materials research published in high impact journals such as Nature and Advanced Materials.