Filter News
Area of Research
- (-) Materials for Computing (4)
- (-) Neutron Science (9)
- Advanced Manufacturing (14)
- Biology and Environment (27)
- Building Technologies (1)
- Clean Energy (80)
- Computational Engineering (2)
- Computer Science (8)
- Electricity and Smart Grid (2)
- Fusion and Fission (4)
- Fusion Energy (1)
- Materials (17)
- Mathematics (1)
- National Security (17)
- Nuclear Science and Technology (2)
- Quantum information Science (7)
- Sensors and Controls (1)
- Supercomputing (34)
News Topics
- (-) 3-D Printing/Advanced Manufacturing (5)
- (-) Big Data (1)
- (-) Clean Water (2)
- (-) Machine Learning (3)
- (-) Mathematics (1)
- (-) Quantum Science (3)
- Artificial Intelligence (5)
- Bioenergy (4)
- Biology (2)
- Biomedical (8)
- Chemical Sciences (4)
- Climate Change (1)
- Computer Science (11)
- Coronavirus (6)
- Decarbonization (2)
- Energy Storage (6)
- Environment (4)
- Fossil Energy (1)
- High-Performance Computing (1)
- Materials (16)
- Materials Science (19)
- Microscopy (5)
- Nanotechnology (9)
- National Security (1)
- Neutron Science (58)
- Nuclear Energy (2)
- Physics (2)
- Polymers (3)
- Quantum Computing (1)
- Security (1)
- Simulation (1)
- Space Exploration (2)
- Summit (2)
- Sustainable Energy (3)
- Transportation (5)
Media Contacts

Scientists at ORNL have developed 3D-printed collimator techniques that can be used to custom design collimators that better filter out noise during different types of neutron scattering experiments

How do you get water to float in midair? With a WAND2, of course. But it’s hardly magic. In fact, it’s a scientific device used by scientists to study matter.
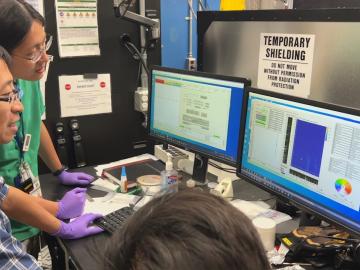
Neutron experiments can take days to complete, requiring researchers to work long shifts to monitor progress and make necessary adjustments. But thanks to advances in artificial intelligence and machine learning, experiments can now be done remotely and in half the time.

A team led by the U.S. Department of Energy’s Oak Ridge National Laboratory demonstrated the viability of a “quantum entanglement witness” capable of proving the presence of entanglement between magnetic particles, or spins, in a quantum material.
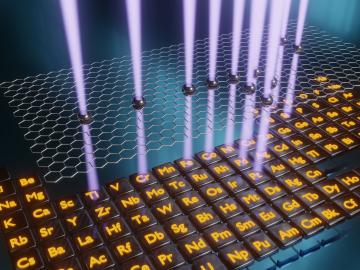
Oak Ridge National Laboratory scientists demonstrated that an electron microscope can be used to selectively remove carbon atoms from graphene’s atomically thin lattice and stitch transition-metal dopant atoms in their place.
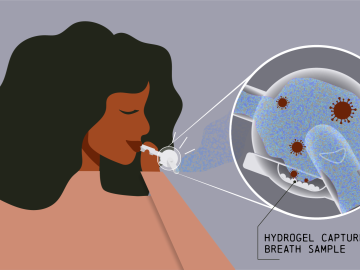
Collaborators at Oak Ridge National Laboratory and the University of Tennessee Health Science Center are developing a breath-sampling whistle that could make COVID-19 screening easy to do at home.

The ExOne Company, the global leader in industrial sand and metal 3D printers using binder jetting technology, announced it has reached a commercial license agreement with Oak Ridge National Laboratory to 3D print parts in aluminum-infiltrated boron carbide.
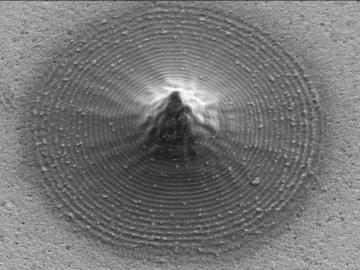
Scientists at Oak Ridge National Laboratory and the University of Tennessee designed and demonstrated a method to make carbon-based materials that can be used as electrodes compatible with a specific semiconductor circuitry.
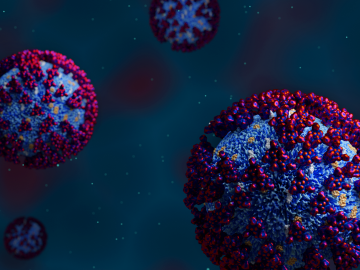
In the race to identify solutions to the COVID-19 pandemic, researchers at the Department of Energy’s Oak Ridge National Laboratory are joining the fight by applying expertise in computational science, advanced manufacturing, data science and neutron science.
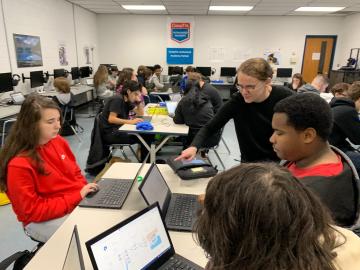
ORNL computer scientist Catherine Schuman returned to her alma mater, Harriman High School, to lead Hour of Code activities and talk to students about her job as a researcher.