Filter News
Area of Research
- (-) Clean Energy (77)
- (-) Supercomputing (35)
- Advanced Manufacturing (15)
- Biology and Environment (38)
- Building Technologies (3)
- Computational Engineering (1)
- Computer Science (8)
- Energy Sciences (1)
- Fusion and Fission (5)
- Fusion Energy (3)
- Isotopes (18)
- Materials (25)
- Materials for Computing (7)
- National Security (15)
- Neutron Science (7)
- Nuclear Science and Technology (5)
- Quantum information Science (7)
News Type
News Topics
- (-) 3-D Printing/Advanced Manufacturing (46)
- (-) Big Data (18)
- (-) Machine Learning (10)
- (-) Quantum Science (14)
- (-) Sustainable Energy (43)
- Advanced Reactors (3)
- Artificial Intelligence (24)
- Bioenergy (14)
- Biology (12)
- Biomedical (14)
- Biotechnology (3)
- Buildings (25)
- Chemical Sciences (6)
- Clean Water (7)
- Climate Change (26)
- Composites (11)
- Computer Science (71)
- Coronavirus (16)
- Critical Materials (7)
- Cybersecurity (7)
- Decarbonization (21)
- Energy Storage (42)
- Environment (45)
- Exascale Computing (13)
- Fossil Energy (1)
- Frontier (14)
- Fusion (1)
- Grid (28)
- High-Performance Computing (23)
- Hydropower (2)
- Materials (22)
- Materials Science (22)
- Mathematics (3)
- Mercury (2)
- Microelectronics (1)
- Microscopy (6)
- Nanotechnology (8)
- National Security (4)
- Net Zero (3)
- Neutron Science (8)
- Nuclear Energy (6)
- Partnerships (4)
- Physics (3)
- Polymers (8)
- Quantum Computing (14)
- Security (3)
- Simulation (12)
- Software (1)
- Space Exploration (5)
- Statistics (1)
- Summit (28)
- Transportation (46)
Media Contacts
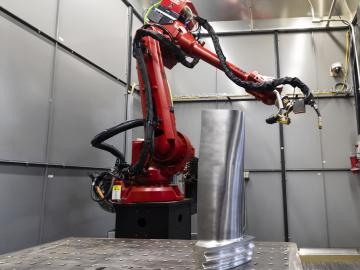
Researchers at ORNL became the first to 3D-print large rotating steam turbine blades for generating energy in power plants.
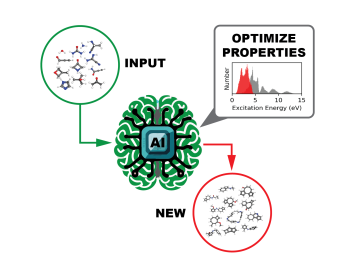
A team of computational scientists at ORNL has generated and released datasets of unprecedented scale that provide the ultraviolet visible spectral properties of over 10 million organic molecules.

Scientists at ORNL used their knowledge of complex ecosystem processes, energy systems, human dynamics, computational science and Earth-scale modeling to inform the nation’s latest National Climate Assessment, which draws attention to vulnerabilities and resilience opportunities in every region of the country.
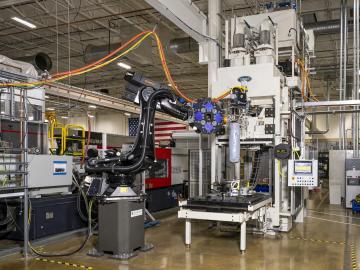
An Oak Ridge National Laboratory-developed advanced manufacturing technology, AMCM, was recently licensed by Orbital Composites and enables the rapid production of composite-based components, which could accelerate the decarbonization of vehicles
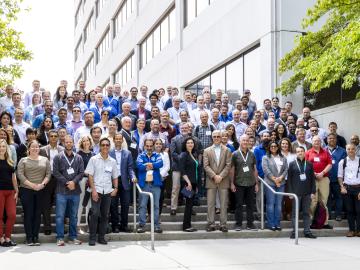
ORNL hosted its annual Smoky Mountains Computational Sciences and Engineering Conference in person for the first time since the COVID-19 pandemic.

Oak Ridge National Laboratory researchers have conducted a comprehensive life cycle, cost and carbon emissions analysis on 3D-printed molds for precast concrete and determined the method is economically beneficial compared to conventional wood molds.

Yarom Polsky, director of the Manufacturing Science Division, or MSD, at the Department of Energy’s Oak Ridge National Laboratory, has been elected a Fellow of the American Society of Mechanical Engineers, or ASME.
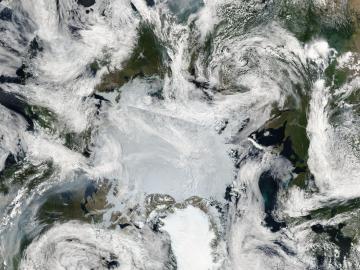
Wildfires have shaped the environment for millennia, but they are increasing in frequency, range and intensity in response to a hotter climate. The phenomenon is being incorporated into high-resolution simulations of the Earth’s climate by scientists at the Department of Energy’s Oak Ridge National Laboratory, with a mission to better understand and predict environmental change.
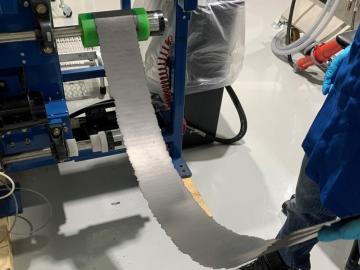
Early experiments at the Department of Energy’s Oak Ridge National Laboratory have revealed significant benefits to a dry battery manufacturing process. This eliminates the use of solvents and is more affordable, while showing promise for delivering a battery that is durable, less weighed down by inactive elements, and able to maintain a high capacity after use.
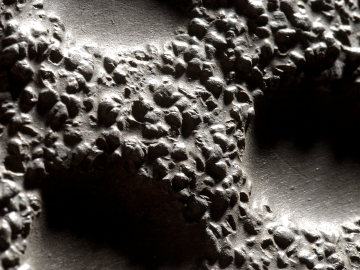
For more than 100 years, Magotteaux has provided grinding materials and castings for the mining, cement and aggregates industries. The company, based in Belgium, began its international expansion in 1968. Its second international plant has been a critical part of the Pulaski, Tennessee, economy since 1972.