Filter News
Area of Research
- (-) Clean Energy (33)
- (-) Neutron Science (15)
- Advanced Manufacturing (2)
- Biology and Environment (12)
- Computational Biology (1)
- Fusion and Fission (3)
- Fusion Energy (1)
- Isotopes (3)
- Materials (39)
- Materials for Computing (5)
- National Security (10)
- Nuclear Science and Technology (1)
- Quantum information Science (2)
- Supercomputing (31)
News Type
News Topics
- (-) Artificial Intelligence (6)
- (-) Materials (9)
- (-) Microscopy (3)
- (-) Nanotechnology (4)
- (-) Polymers (2)
- (-) Security (4)
- (-) Space Exploration (2)
- (-) Transportation (21)
- 3-D Printing/Advanced Manufacturing (27)
- Advanced Reactors (2)
- Big Data (2)
- Bioenergy (12)
- Biology (5)
- Biomedical (7)
- Biotechnology (1)
- Buildings (14)
- Chemical Sciences (4)
- Clean Water (5)
- Climate Change (8)
- Composites (2)
- Computer Science (13)
- Coronavirus (9)
- Critical Materials (1)
- Cybersecurity (5)
- Decarbonization (19)
- Energy Storage (25)
- Environment (23)
- Fossil Energy (2)
- Grid (15)
- High-Performance Computing (3)
- Machine Learning (3)
- Materials Science (12)
- Mathematics (2)
- Mercury (1)
- Microelectronics (1)
- National Security (2)
- Net Zero (1)
- Neutron Science (35)
- Nuclear Energy (3)
- Partnerships (4)
- Physics (1)
- Quantum Computing (1)
- Quantum Science (2)
- Simulation (1)
- Summit (4)
- Sustainable Energy (16)
Media Contacts

Scientists at ORNL have developed 3D-printed collimator techniques that can be used to custom design collimators that better filter out noise during different types of neutron scattering experiments
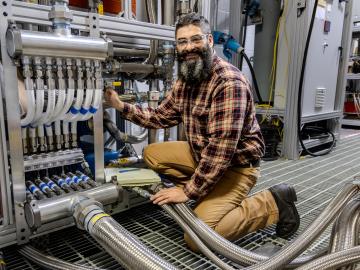
Within the Department of Energy’s National Transportation Research Center at ORNL’s Hardin Valley Campus, scientists investigate engines designed to help the U.S. pivot to a clean mobility future.
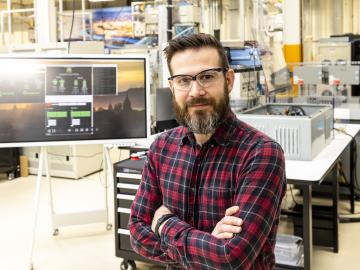
Steven Campbell can often be found deep among tall cases of power electronics, hunkered in his oversized blue lab coat, with 1500 volts of electricity flowing above his head. When interrupted in his laboratory at ORNL, Campbell will usually smile and duck his head.
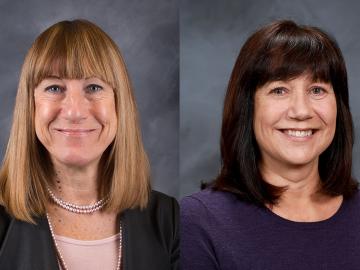
ORNL’s Fulvia Pilat and Karren More recently participated in the inaugural 2023 Nanotechnology Infrastructure Leaders Summit and Workshop at the White House.
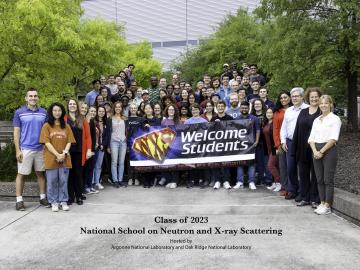
In 2023, the National School on X-ray and Neutron Scattering, or NXS, marked its 25th year during its annual program, held August 6–18 at the Department of Energy’s Oak Ridge and Argonne National Laboratories.
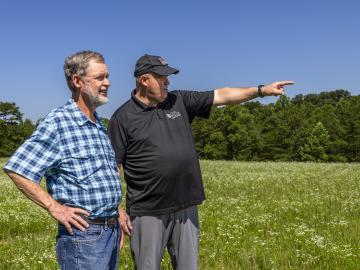
Carl Dukes’ career as an adept communicator got off to a slow start: He was about 5 years old when he spoke for the first time. “I’ve been making up for lost time ever since,” joked Dukes, a technical professional at the Department of Energy’s Oak Ridge National Laboratory.
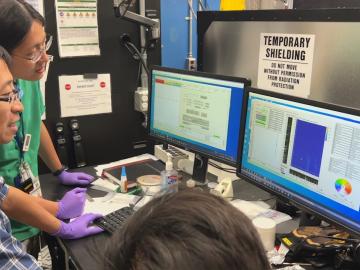
Neutron experiments can take days to complete, requiring researchers to work long shifts to monitor progress and make necessary adjustments. But thanks to advances in artificial intelligence and machine learning, experiments can now be done remotely and in half the time.

Subho Mukherjee, an R&D associate in the Vehicle Power Electronics Research group at the Department of Energy’s Oak Ridge National Laboratory, has been elevated to the grade of senior member of the Institute of Electrical and Electronics Engineers.

Researchers at the Department of Energy’s Oak Ridge National Laboratory were the first to use neutron reflectometry to peer inside a working solid-state battery and monitor its electrochemistry.
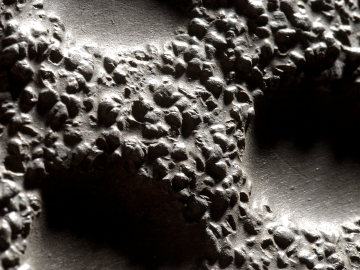
For more than 100 years, Magotteaux has provided grinding materials and castings for the mining, cement and aggregates industries. The company, based in Belgium, began its international expansion in 1968. Its second international plant has been a critical part of the Pulaski, Tennessee, economy since 1972.