Filter News
Area of Research
- (-) Advanced Manufacturing (10)
- (-) Isotopes (4)
- Biological Systems (1)
- Biology and Environment (26)
- Clean Energy (77)
- Computational Biology (1)
- Computational Engineering (1)
- Electricity and Smart Grid (1)
- Fusion and Fission (6)
- Materials (32)
- Materials for Computing (5)
- National Security (9)
- Neutron Science (15)
- Nuclear Science and Technology (5)
- Supercomputing (45)
News Topics
- (-) 3-D Printing/Advanced Manufacturing (10)
- (-) Biomedical (4)
- Artificial Intelligence (1)
- Bioenergy (1)
- Climate Change (1)
- Computer Science (2)
- Cybersecurity (1)
- Environment (1)
- Isotopes (21)
- Machine Learning (1)
- Materials (5)
- Materials Science (3)
- National Security (1)
- Neutron Science (2)
- Nuclear Energy (4)
- Security (1)
- Space Exploration (3)
- Sustainable Energy (2)
- Transformational Challenge Reactor (1)
Media Contacts

Scientists at ORNL have developed 3D-printed collimator techniques that can be used to custom design collimators that better filter out noise during different types of neutron scattering experiments
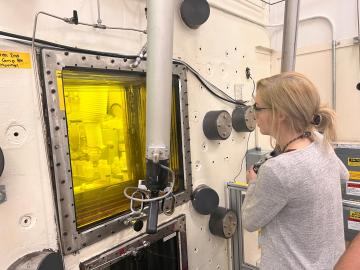
Raina Setzer knows the work she does matters. That’s because she’s already seen it from the other side. Setzer, a radiochemical processing technician in Oak Ridge National Laboratory’s Isotope Processing and Manufacturing Division, joined the lab in June 2023.

As a medical isotope, thorium-228 has a lot of potential — and Oak Ridge National Laboratory produces a lot.
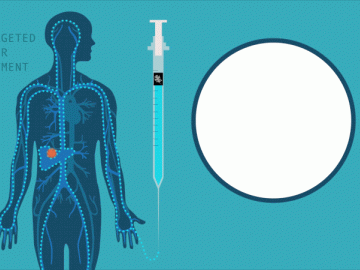
A rare isotope in high demand for treating cancer is now more available to pharmaceutical companies developing and testing new drugs.

The ExOne Company, the global leader in industrial sand and metal 3D printers using binder jetting technology, announced it has reached a commercial license agreement with Oak Ridge National Laboratory to 3D print parts in aluminum-infiltrated boron carbide.
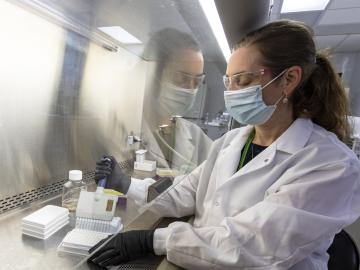
When Sandra Davern looks to the future, she sees individualized isotopes sent into the body with a specific target: cancer cells.
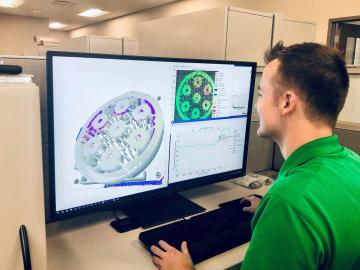
Oak Ridge National Laboratory researchers have developed artificial intelligence software for powder bed 3D printers that assesses the quality of parts in real time, without the need for expensive characterization equipment.
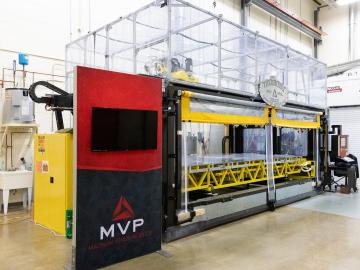
ORNL has licensed two additive manufacturing-related technologies that aim to streamline and ramp up production processes to Knoxville-based Magnum Venus Products, Inc., a global manufacturer of fluid movement and product solutions for industrial applications in composites and adhesives.
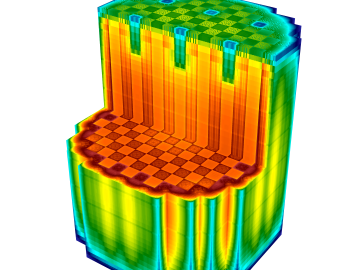
OAK RIDGE, Tenn., Feb. 19, 2020 — The U.S. Department of Energy’s Oak Ridge National Laboratory and the Tennessee Valley Authority have signed a memorandum of understanding to evaluate a new generation of flexible, cost-effective advanced nuclear reactors.
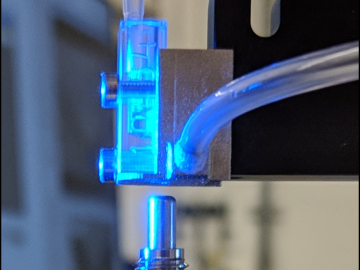
Researchers at the Department of Energy’s Oak Ridge National Laboratory have received five 2019 R&D 100 Awards, increasing the lab’s total to 221 since the award’s inception in 1963.