
Filter News
Area of Research
News Type
News Topics
- (-) Composites (12)
- (-) Partnerships (27)
- 3-D Printing/Advanced Manufacturing (60)
- Advanced Reactors (13)
- Artificial Intelligence (59)
- Big Data (34)
- Bioenergy (57)
- Biology (66)
- Biomedical (35)
- Biotechnology (12)
- Buildings (30)
- Chemical Sciences (38)
- Clean Water (15)
- Climate Change (59)
- Computer Science (105)
- Coronavirus (21)
- Critical Materials (6)
- Cybersecurity (20)
- Decarbonization (50)
- Education (2)
- Emergency (2)
- Energy Storage (45)
- Environment (119)
- Exascale Computing (33)
- Fossil Energy (4)
- Frontier (30)
- Fusion (40)
- Grid (29)
- High-Performance Computing (60)
- Hydropower (5)
- Irradiation (1)
- Isotopes (39)
- ITER (3)
- Machine Learning (25)
- Materials (77)
- Materials Science (69)
- Mathematics (7)
- Mercury (7)
- Microelectronics (3)
- Microscopy (28)
- Molten Salt (2)
- Nanotechnology (28)
- National Security (54)
- Net Zero (9)
- Neutron Science (66)
- Nuclear Energy (69)
- Physics (37)
- Polymers (13)
- Quantum Computing (25)
- Quantum Science (36)
- Renewable Energy (1)
- Security (15)
- Simulation (38)
- Software (1)
- Space Exploration (13)
- Statistics (1)
- Summit (35)
- Sustainable Energy (56)
- Transformational Challenge Reactor (4)
- Transportation (38)
Media Contacts
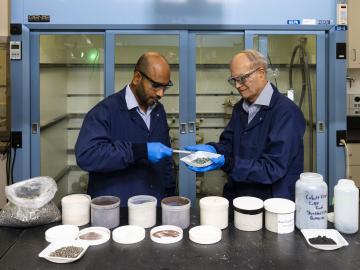
Scientists at ORNL have developed a technique for recovering and recycling critical materials that has garnered special recognition from a peer-reviewed materials journal and received a new phase of funding for research and development.
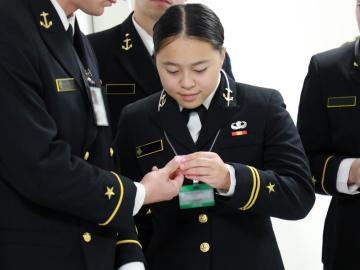
Nuclear engineering students from the United States Military Academy and United States Naval Academy are working with researchers at ORNL to complete design concepts for a nuclear propulsion rocket to go to space in 2027 as part of the Defense Advanced Research Projects Agency DRACO program.
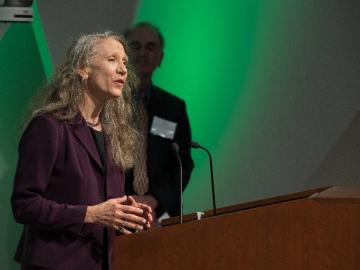
The founder of a startup company who is working with ORNL has won an Environmental Protection Agency Green Chemistry Challenge Award for a unique air pollution control technology.
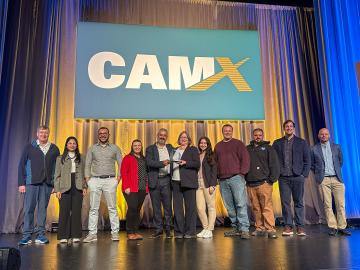
The Hub & Spoke Sustainable Materials & Manufacturing Alliance for Renewable Technologies, or SM2ART, program has been honored with the composites industry’s Combined Strength Award at the Composites and Advanced Materials Expo, or CAMX, 2023 in Atlanta. This distinction goes to the team that applies their knowledge, resources and talent to solve a problem by making the best use of composites materials.
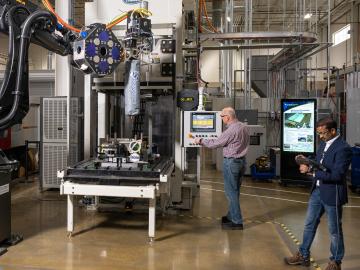
Researchers at ORNL are extending the boundaries of composite-based materials used in additive manufacturing, or AM. ORNL is working with industrial partners who are exploring AM, also known as 3D printing, as a path to higher production levels and fewer supply chain interruptions.

In fiscal year 2023 — Oct. 1–Sept. 30, 2023 — Oak Ridge National Laboratory was awarded more than $8 million in technology maturation funding through the Department of Energy’s Technology Commercialization Fund, or TCF.

Technologies developed by researchers at ORNL have received six 2023 R&D 100 Awards.
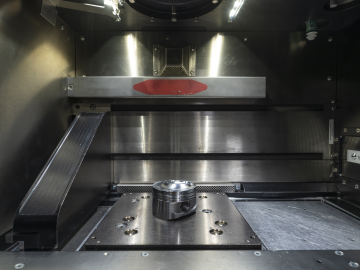
Dean Pierce of ORNL and a research team led by ORNL’s Alex Plotkowski were honored by DOE’s Vehicle Technologies Office for development of novel high-performance alloys that can withstand extreme environments.
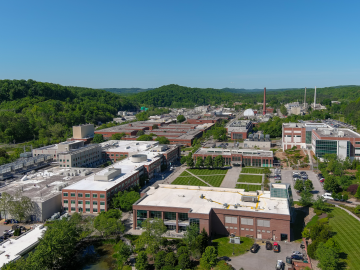
Four firms doing business with the Department of Energy’s Oak Ridge National Laboratory received ORNL Small Business Awards during an awards ceremony on June 29.
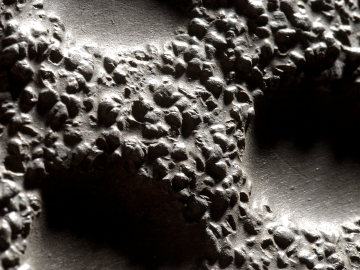
For more than 100 years, Magotteaux has provided grinding materials and castings for the mining, cement and aggregates industries. The company, based in Belgium, began its international expansion in 1968. Its second international plant has been a critical part of the Pulaski, Tennessee, economy since 1972.