Filter News
Area of Research
- (-) Clean Energy (30)
- Advanced Manufacturing (2)
- Biology and Environment (8)
- Computational Biology (1)
- Electricity and Smart Grid (2)
- Functional Materials for Energy (1)
- Fusion and Fission (25)
- Fusion Energy (4)
- Isotopes (5)
- Materials (47)
- Materials Characterization (1)
- Materials for Computing (8)
- Materials Under Extremes (1)
- National Security (12)
- Neutron Science (44)
- Nuclear Science and Technology (21)
- Supercomputing (20)
News Type
News Topics
- (-) Grid (14)
- (-) Materials Science (10)
- (-) Neutron Science (3)
- (-) Nuclear Energy (3)
- (-) Space Exploration (1)
- 3-D Printing/Advanced Manufacturing (33)
- Advanced Reactors (4)
- Artificial Intelligence (5)
- Big Data (2)
- Bioenergy (13)
- Biology (6)
- Biomedical (3)
- Biotechnology (1)
- Buildings (13)
- Chemical Sciences (7)
- Clean Water (3)
- Climate Change (10)
- Composites (4)
- Computer Science (10)
- Coronavirus (7)
- Critical Materials (1)
- Cybersecurity (6)
- Decarbonization (16)
- Energy Storage (30)
- Environment (26)
- Fossil Energy (1)
- Frontier (1)
- Fusion (1)
- High-Performance Computing (4)
- Isotopes (1)
- Machine Learning (2)
- Materials (13)
- Mathematics (1)
- Mercury (1)
- Microelectronics (1)
- Microscopy (4)
- Molten Salt (1)
- Nanotechnology (6)
- National Security (1)
- Net Zero (1)
- Partnerships (5)
- Physics (1)
- Polymers (3)
- Quantum Science (1)
- Security (3)
- Simulation (2)
- Summit (2)
- Sustainable Energy (19)
- Transformational Challenge Reactor (1)
- Transportation (22)
Media Contacts

Three researchers at ORNL have been named ORNL Corporate Fellows in recognition of significant career accomplishments and continued leadership in their scientific fields.
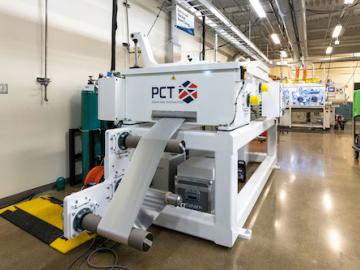
Researchers at the Department of Energy’s Oak Ridge National Laboratory and their technologies have received seven 2022 R&D 100 Awards, plus special recognition for a battery-related green technology product.
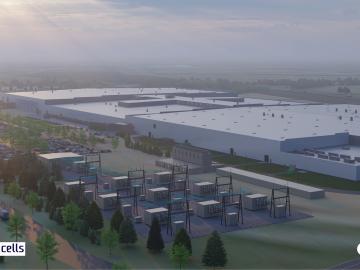
ORNL, TVA and TNECD were recognized by the Federal Laboratory Consortium for their impactful partnership that resulted in a record $2.3 billion investment by Ultium Cells, a General Motors and LG Energy Solution joint venture, to build a battery cell manufacturing plant in Spring Hill, Tennessee.
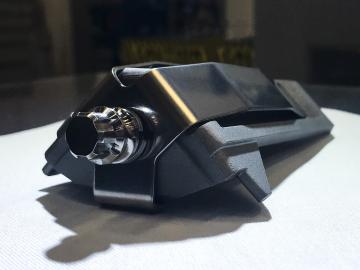
Four first-of-a-kind 3D-printed fuel assembly brackets, produced at the Department of Energy’s Manufacturing Demonstration Facility at Oak Ridge National Laboratory, have been installed and are now under routine operating
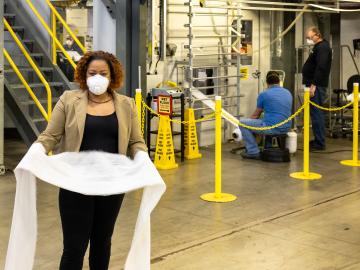
Three technologies developed by ORNL researchers have won National Technology Transfer Awards from the Federal Laboratory Consortium. One of the awards went to a team that adapted melt-blowing capabilities at DOE’s Carbon Fiber Technology Facility to enable the production of filter material for N95 masks in the fight against COVID-19.

The ExOne Company, the global leader in industrial sand and metal 3D printers using binder jetting technology, announced it has reached a commercial license agreement with Oak Ridge National Laboratory to 3D print parts in aluminum-infiltrated boron carbide.
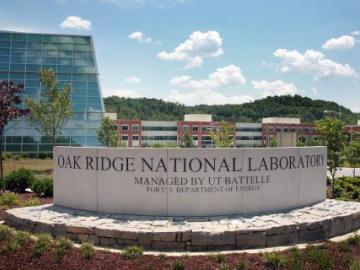
Seven ORNL scientists have been named among the 2020 Highly Cited Researchers list, according to Clarivate, a data analytics firm that specializes in scientific and academic research.
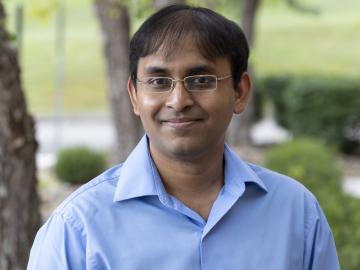
Planning for a digitized, sustainable smart power grid is a challenge to which Suman Debnath is using not only his own applied mathematics expertise, but also the wider communal knowledge made possible by his revival of a local chapter of the IEEE professional society.
A collaboration between the ORNL and a Florida-based medical device manufacturer has led to the addition of 500 jobs in the Miami area to support the mass production of N95 respirator masks.
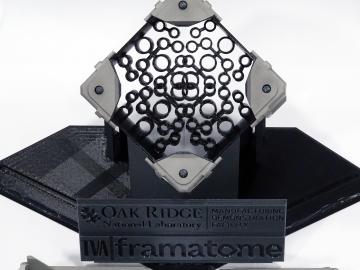
The Transformational Challenge Reactor, or TCR, a microreactor built using 3D printing and other new advanced technologies, could be operational by 2024.