Filter News
Area of Research
- (-) Clean Energy (126)
- Advanced Manufacturing (6)
- Biological Systems (2)
- Biology and Environment (116)
- Biology and Soft Matter (1)
- Building Technologies (2)
- Climate and Environmental Systems (4)
- Computational Biology (2)
- Computational Engineering (1)
- Computer Science (4)
- Electricity and Smart Grid (1)
- Energy Sciences (2)
- Functional Materials for Energy (2)
- Fusion and Fission (7)
- Fusion Energy (2)
- Isotopes (6)
- Materials (46)
- Materials for Computing (7)
- Mathematics (1)
- National Security (9)
- Neutron Science (17)
- Nuclear Science and Technology (2)
- Quantum information Science (1)
- Supercomputing (54)
News Type
News Topics
- (-) Bioenergy (15)
- (-) Biomedical (4)
- (-) Composites (13)
- (-) Energy Storage (51)
- (-) Environment (41)
- (-) Frontier (1)
- (-) Sustainable Energy (46)
- 3-D Printing/Advanced Manufacturing (56)
- Advanced Reactors (4)
- Artificial Intelligence (6)
- Big Data (3)
- Biology (8)
- Biotechnology (2)
- Buildings (26)
- Chemical Sciences (8)
- Clean Water (7)
- Climate Change (16)
- Computer Science (19)
- Coronavirus (9)
- Critical Materials (5)
- Cybersecurity (6)
- Decarbonization (20)
- Fossil Energy (1)
- Fusion (1)
- Grid (29)
- High-Performance Computing (5)
- Hydropower (2)
- Isotopes (1)
- Machine Learning (4)
- Materials (25)
- Materials Science (19)
- Mathematics (2)
- Mercury (2)
- Microelectronics (1)
- Microscopy (6)
- Molten Salt (1)
- Nanotechnology (7)
- National Security (1)
- Net Zero (2)
- Neutron Science (3)
- Nuclear Energy (4)
- Partnerships (5)
- Physics (1)
- Polymers (8)
- Quantum Science (1)
- Security (3)
- Simulation (3)
- Space Exploration (3)
- Statistics (1)
- Summit (2)
- Transformational Challenge Reactor (1)
- Transportation (48)
Media Contacts
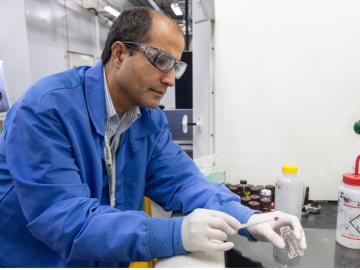
Electric vehicles can drive longer distances if their lithium-ion batteries deliver more energy in a lighter package. A prime weight-loss candidate is the current collector, a component that often adds 10% to the weight of a battery cell without contributing energy.
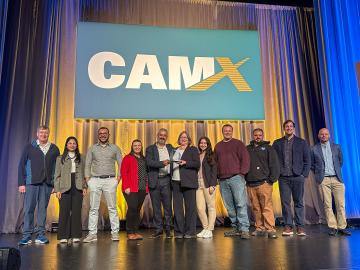
The Hub & Spoke Sustainable Materials & Manufacturing Alliance for Renewable Technologies, or SM2ART, program has been honored with the composites industry’s Combined Strength Award at the Composites and Advanced Materials Expo, or CAMX, 2023 in Atlanta. This distinction goes to the team that applies their knowledge, resources and talent to solve a problem by making the best use of composites materials.
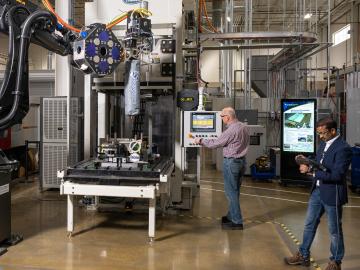
Researchers at ORNL are extending the boundaries of composite-based materials used in additive manufacturing, or AM. ORNL is working with industrial partners who are exploring AM, also known as 3D printing, as a path to higher production levels and fewer supply chain interruptions.

In fiscal year 2023 — Oct. 1–Sept. 30, 2023 — Oak Ridge National Laboratory was awarded more than $8 million in technology maturation funding through the Department of Energy’s Technology Commercialization Fund, or TCF.
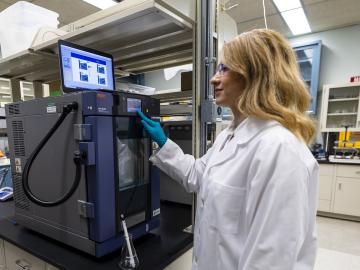
The common sounds in the background of daily life – like a refrigerator’s hum, an air conditioner’s whoosh and a heat pump’s buzz – often go unnoticed. These noises, however, are the heartbeat of a healthy building and integral for comfort and convenience.

Oak Ridge National Laboratory researchers are taking fast charging for electric vehicles, or EVs, to new extremes. A team of battery scientists recently developed a lithium-ion battery material that not only recharges 80% of its capacity in 10
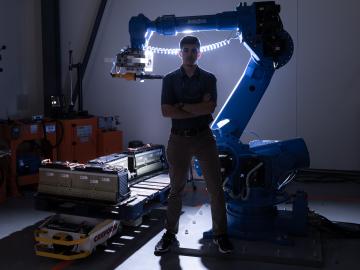
After being stabilized in an ambulance as he struggled to breathe, Jonathan Harter hit a low point. It was 2020, he was very sick with COVID-19, and his job as a lab technician at ORNL was ending along with his research funding.

Yarom Polsky, director of the Manufacturing Science Division, or MSD, at the Department of Energy’s Oak Ridge National Laboratory, has been elected a Fellow of the American Society of Mechanical Engineers, or ASME.
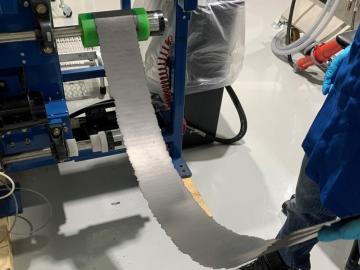
Early experiments at the Department of Energy’s Oak Ridge National Laboratory have revealed significant benefits to a dry battery manufacturing process. This eliminates the use of solvents and is more affordable, while showing promise for delivering a battery that is durable, less weighed down by inactive elements, and able to maintain a high capacity after use.
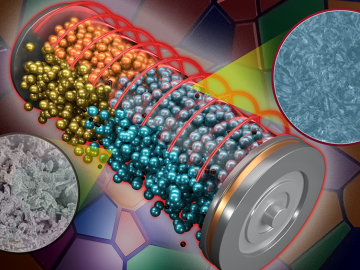
ORNL scientists found that a small tweak created big performance improvements in a type of solid-state battery, a technology considered vital to broader electric vehicle adoption.