Filter News
Area of Research
News Topics
- (-) 3-D Printing/Advanced Manufacturing (20)
- (-) Frontier (19)
- (-) Materials (59)
- Advanced Reactors (3)
- Artificial Intelligence (26)
- Big Data (10)
- Bioenergy (22)
- Biology (29)
- Biomedical (7)
- Biotechnology (6)
- Buildings (14)
- Chemical Sciences (24)
- Clean Water (5)
- Climate Change (31)
- Composites (6)
- Computer Science (23)
- Coronavirus (4)
- Critical Materials (6)
- Cybersecurity (9)
- Decarbonization (30)
- Education (3)
- Emergency (1)
- Energy Storage (21)
- Environment (43)
- Exascale Computing (15)
- Fossil Energy (2)
- Fusion (9)
- Grid (16)
- High-Performance Computing (33)
- Hydropower (3)
- Irradiation (2)
- Isotopes (11)
- Machine Learning (15)
- Materials Science (16)
- Mathematics (2)
- Mercury (2)
- Microelectronics (2)
- Microscopy (7)
- Molten Salt (1)
- Nanotechnology (7)
- National Security (21)
- Net Zero (5)
- Neutron Science (32)
- Nuclear Energy (21)
- Partnerships (24)
- Physics (14)
- Polymers (4)
- Quantum Computing (12)
- Quantum Science (9)
- Renewable Energy (2)
- Security (3)
- Simulation (29)
- Software (1)
- Space Exploration (4)
- Summit (9)
- Sustainable Energy (17)
- Transportation (18)
Media Contacts
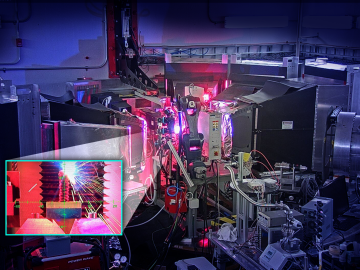
Using neutrons to see the additive manufacturing process at the atomic level, scientists have shown that they can measure strain in a material as it evolves and track how atoms move in response to stress.
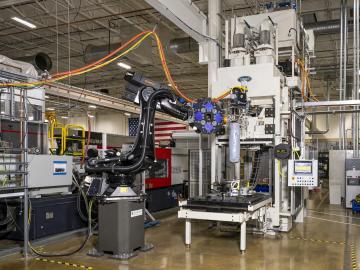
An Oak Ridge National Laboratory-developed advanced manufacturing technology, AMCM, was recently licensed by Orbital Composites and enables the rapid production of composite-based components, which could accelerate the decarbonization of vehicles
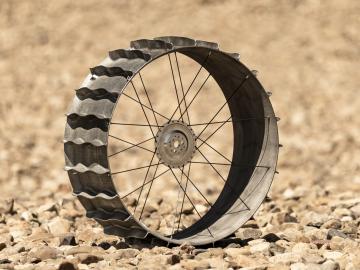
Researchers at the Department of Energy’s Oak Ridge National Laboratory, in collaboration with NASA, are taking additive manufacturing to the final frontier by 3D printing the same kind of wheel as the design used by NASA for its robotic lunar rover, demonstrating the technology for specialized parts needed for space exploration.

ORNL, a bastion of nuclear physics research for the past 80 years, is poised to strengthen its programs and service to the United States over the next decade if national recommendations of the Nuclear Science Advisory Committee, or NSAC, are enacted.
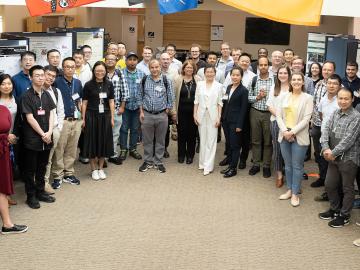
When the second collaborative ORNL-Vanderbilt University workshop took place on Sept. 18-19 at ORNL, about 70 researchers and students assembled to share thoughts concerning a broad spectrum of topics.
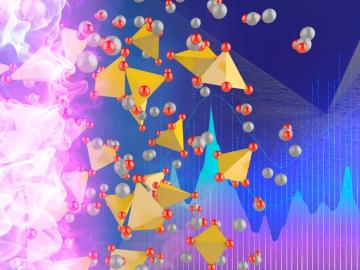
As current courses through a battery, its materials erode over time. Mechanical influences such as stress and strain affect this trajectory, although their impacts on battery efficacy and longevity are not fully understood.
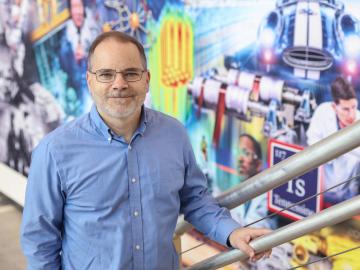
ORNL has been selected to lead an Energy Earthshot Research Center, or EERC, focused on developing chemical processes that use sustainable methods instead of burning fossil fuels to radically reduce industrial greenhouse gas emissions to stem climate change and limit the crisis of a rapidly warming planet.
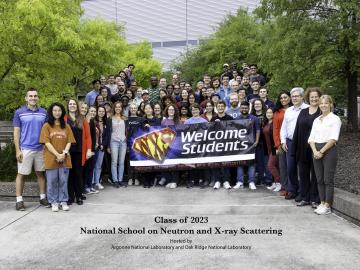
In 2023, the National School on X-ray and Neutron Scattering, or NXS, marked its 25th year during its annual program, held August 6–18 at the Department of Energy’s Oak Ridge and Argonne National Laboratories.
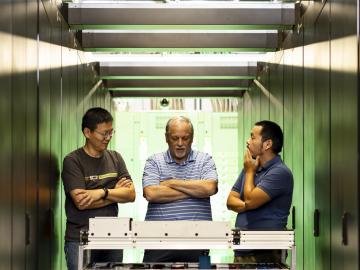
As Frontier, the world’s first exascale supercomputer, was being assembled at the Oak Ridge Leadership Computing Facility in 2021, understanding its performance on mixed-precision calculations remained a difficult prospect.

Oak Ridge National Laboratory researchers have conducted a comprehensive life cycle, cost and carbon emissions analysis on 3D-printed molds for precast concrete and determined the method is economically beneficial compared to conventional wood molds.