
Filter News
Area of Research
- Advanced Manufacturing (7)
- Biology and Environment (3)
- Clean Energy (26)
- Computer Science (2)
- Electricity and Smart Grid (1)
- Fusion and Fission (2)
- Isotopes (1)
- Materials (2)
- Materials for Computing (8)
- National Security (1)
- Neutron Science (3)
- Quantum information Science (3)
- Sensors and Controls (1)
- Supercomputing (3)
News Type
News Topics
- (-) 3-D Printing/Advanced Manufacturing (19)
- (-) Big Data (4)
- (-) Grid (8)
- (-) Materials (21)
- (-) Quantum Science (7)
- Advanced Reactors (2)
- Artificial Intelligence (5)
- Bioenergy (12)
- Biology (18)
- Biomedical (6)
- Biotechnology (4)
- Buildings (9)
- Chemical Sciences (3)
- Clean Water (8)
- Climate Change (10)
- Composites (3)
- Computer Science (21)
- Coronavirus (6)
- Critical Materials (2)
- Cybersecurity (2)
- Decarbonization (6)
- Energy Storage (13)
- Environment (36)
- Exascale Computing (2)
- Frontier (1)
- Fusion (3)
- High-Performance Computing (14)
- Isotopes (8)
- ITER (3)
- Materials Science (14)
- Mathematics (1)
- Mercury (3)
- Microscopy (6)
- Nanotechnology (5)
- National Security (4)
- Net Zero (1)
- Neutron Science (11)
- Nuclear Energy (4)
- Physics (2)
- Polymers (2)
- Quantum Computing (2)
- Security (2)
- Space Exploration (4)
- Statistics (1)
- Summit (4)
- Sustainable Energy (29)
- Transportation (17)
Media Contacts
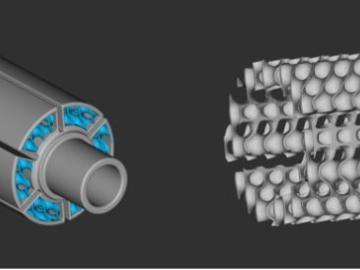
Additive manufacturing can make the design and production of specialized tools for geothermal energy cheaper and more efficient, according to a study by Oak Ridge National Laboratory.
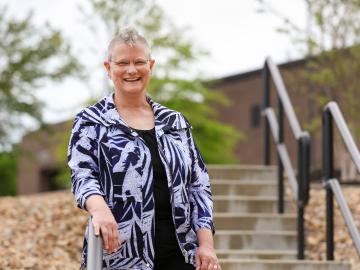
As a computer engineer at Oak Ridge National Laboratory, Gina Accawi has long been the quiet and steady force behind some of the Department of Energy’s most widely used online tools and applications.
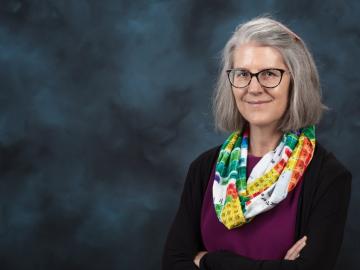
Deborah Frincke, one of the nation’s preeminent computer scientists and cybersecurity experts, serves as associate laboratory director of ORNL’s National Security Science Directorate. Credit: Carlos Jones/ORNL, U.S. Dept. of Energy
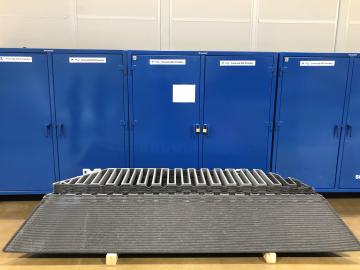
Oak Ridge National Laboratory researchers, in collaboration with Cincinnati Inc., demonstrated the potential for using multimaterials and recycled composites in large-scale applications by 3D printing a mold that replicated a single facet of a
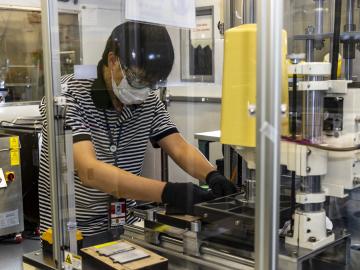
In his career focused on energy storage science, Jianlin Li has learned that discovering new ways to process and assemble batteries is just as important as the development of new materials.
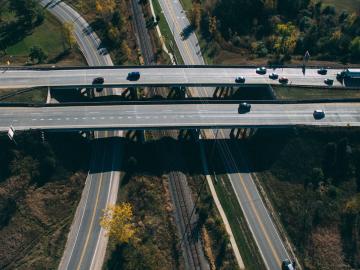
Through a consortium of Department of Energy national laboratories, ORNL scientists are applying their expertise to provide solutions that enable the commercialization of emission-free hydrogen fuel cell technology for heavy-duty
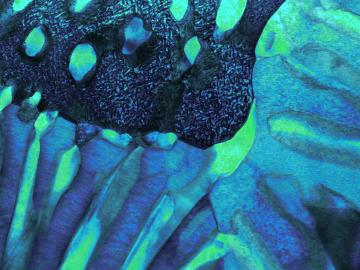
Oak Ridge National Laboratory scientists proved molybdenum titanium carbide, a refractory metal alloy that can withstand extreme temperature environments, can also be crack free and dense when produced with electron beam powder bed fusion.
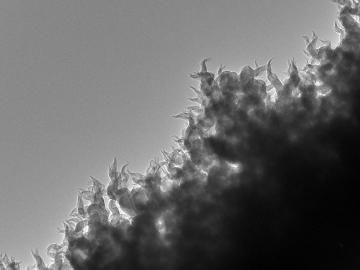
In a new twist to an existing award-winning ORNL technology, researchers have developed an electrocatalyst that enables water and carbon dioxide to be split and the atoms recombined to form higher weight hydrocarbons for gasoline, diesel and jet fuel.
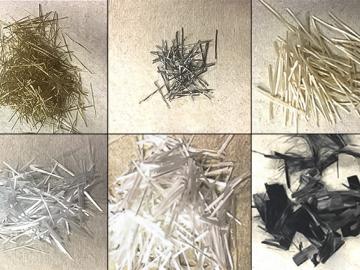
A team of researchers at Oak Ridge National Laboratory and the University of Tennessee have developed a concrete mix that demonstrated high early strength within six hours of mixing, potentially doubling the production capacity for the precast industry.
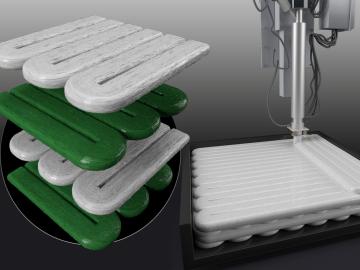
Oak Ridge National Laboratory researchers combined additive manufacturing with conventional compression molding to produce high-performance thermoplastic composites reinforced with short carbon fibers.